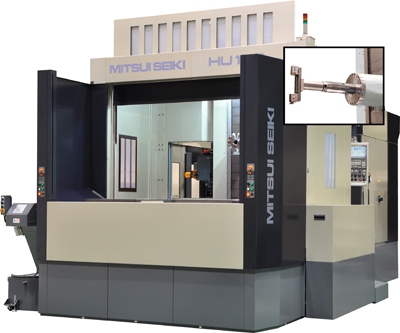
The newest addition to Mitsui Seiki's heavy-duty series of HU100 horizontal machining centers is engineered for precision boring of large parts in energy-related industries as well as other critical applications.
The quill spindle configuration of the new HU100 Quill Spindle is well suited for boring of oil and gas field valves and fittings in addition to other fluid-transfer components. The 4.4" (110mm)-dia. quill has a W-axis stroke of 12" (300mm) and produces hole pitch accuracy within 1.5µm and hexagon angle error within 0.002ÌÜÅÁ.
The machine features X-Y axis stroke of 40" (1,000mm) and Z stroke of 52" (1,300mm) standard, and a 40" X 40" (1,000mm x 1,000mm) table that can handle a 6,600 lb (3,000 kg) maximum work load. The work envelope has capacity for workpieces up to 60" (1,500mm) in diameter. As with the entire line of HU100 machining centers, a variety of increased strokes and weight capacities are available to suit the customer's application. Rigidity, squareness and parallelism of the machine's construction result in positioning accuracy of 3µm (+/- 0.0001").
With maximum/continuous power of 47 hp (25kW)/29 hp (22 kW) and maximum/continuous torque of 873 lb-ft (1184 nm)/737 lb-ft (1,000 nm), the machine spindle offers speeds from 15-3,000 rpm. A standard 60-tool capacity automatic tool changer adds flexibility and extends machine uptime.
Mitsui Seiki (U.S.A.) Inc. vice president Tom Dolan said, "The HU100 Quill Spindle HMC, with its ability to achieve extremely accurate boring for large, complex parts, is a further example of Mitsui Seiki's ability to offer manufacturers of high-end energy-related parts a full spectrum of milling and boring solutions. Together with other machines such as our Vertex -5XB 5-axis VMC for industrial gas turbine blades and HU-5X 5-axis trunnion high-production HMCs, Mitsui Seiki provides a wide variety of ways to help our customers maximize their productivity and profitability."
Contact Details
Related Glossary Terms
- boring
boring
Enlarging a hole that already has been drilled or cored. Generally, it is an operation of truing the previously drilled hole with a single-point, lathe-type tool. Boring is essentially internal turning, in that usually a single-point cutting tool forms the internal shape. Some tools are available with two cutting edges to balance cutting forces.
- centers
centers
Cone-shaped pins that support a workpiece by one or two ends during machining. The centers fit into holes drilled in the workpiece ends. Centers that turn with the workpiece are called “live” centers; those that do not are called “dead” centers.
- gang cutting ( milling)
gang cutting ( milling)
Machining with several cutters mounted on a single arbor, generally for simultaneous cutting.
- milling
milling
Machining operation in which metal or other material is removed by applying power to a rotating cutter. In vertical milling, the cutting tool is mounted vertically on the spindle. In horizontal milling, the cutting tool is mounted horizontally, either directly on the spindle or on an arbor. Horizontal milling is further broken down into conventional milling, where the cutter rotates opposite the direction of feed, or “up” into the workpiece; and climb milling, where the cutter rotates in the direction of feed, or “down” into the workpiece. Milling operations include plane or surface milling, endmilling, facemilling, angle milling, form milling and profiling.
- pitch
pitch
1. On a saw blade, the number of teeth per inch. 2. In threading, the number of threads per inch.
- work envelope
work envelope
Cube, sphere, cylinder or other physical space within which the cutting tool is capable of reaching.