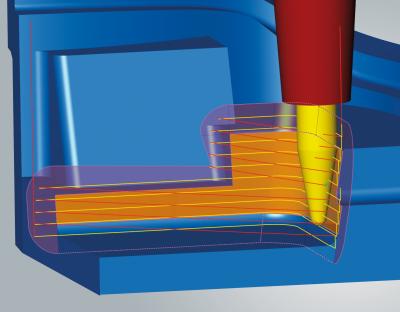
OPEN MIND Technologies AG has introduced hyperMILL 2018.2, the latest version of its advanced, comprehensive CAM software. hyperMILL 2018.2 offers a range of enhancements and new features for 3D Shape Z-level Finishing and 3D Optimized Roughing and greater CAD functionality.
For reduced programming times and improved milling, 3D Z-level Shape Finishing, available in hyperCAD®-S, has two new features. "Automatic face extension" can be used during CAM programming to automatically extend the selected milling surfaces, eliminating manual CAD work and resulting in cleaner corner cuts. Also, 3D Z-level Shape Finishing now has the ability to support conical barrel cutters in addition to general and tangential cutters.
During 3D Optimized Roughing, multiple allowances are now recognized and accounted for when using free tool geometries, resulting in easier programming and a high level of flexibility for defining special tools. hyperMILL 2018.2 can define different allowances and adapt the machining process accordingly. High-feed cutters have a special cutting geometry that is easy to define using tool management, and hyperMILL 2018.2 uses the free geometries of the cutting tool edge for calculation, simulation and collision checking.
"Keeping the hyperMILL suite at the forefront of CAM technology, we are pleased to offer our customers improved CAM strategies and enhanced CAD tools for even greater machining productivity through our new release of hyperMILL 2018.2," said Alan Levine, managing director of OPEN MIND Technologies USA Inc.
New hyperMILL 2018.2 functionality also includes several enhancements to its hyperCAD-S module, including the ability to measure and record the distances between two shapes such as face models, solids, meshes or stock. In addition, for easy changes to milling boundaries and turning contours, hyperMILL 2018.2 offers a "V sketch" command that assigns geometric constraints to 2D contours. When individual contours are changed, the sketch is automatically updated using their dependencies.
The electrode module, which provides quick designing of die-sinking electrodes, offers a new Virtual Electrode function for securely creating electrode copies which are checked for collisions, and can be assigned new technology values or the values of the master electrodes. For easier analysis, the reference system and eroding position for each electrode copy are included in a report.
Contact Details
Related Glossary Terms
- computer-aided design ( CAD)
computer-aided design ( CAD)
Product-design functions performed with the help of computers and special software.
- computer-aided manufacturing ( CAM)
computer-aided manufacturing ( CAM)
Use of computers to control machining and manufacturing processes.
- gang cutting ( milling)
gang cutting ( milling)
Machining with several cutters mounted on a single arbor, generally for simultaneous cutting.
- milling
milling
Machining operation in which metal or other material is removed by applying power to a rotating cutter. In vertical milling, the cutting tool is mounted vertically on the spindle. In horizontal milling, the cutting tool is mounted horizontally, either directly on the spindle or on an arbor. Horizontal milling is further broken down into conventional milling, where the cutter rotates opposite the direction of feed, or “up” into the workpiece; and climb milling, where the cutter rotates in the direction of feed, or “down” into the workpiece. Milling operations include plane or surface milling, endmilling, facemilling, angle milling, form milling and profiling.
- turning
turning
Workpiece is held in a chuck, mounted on a face plate or secured between centers and rotated while a cutting tool, normally a single-point tool, is fed into it along its periphery or across its end or face. Takes the form of straight turning (cutting along the periphery of the workpiece); taper turning (creating a taper); step turning (turning different-size diameters on the same work); chamfering (beveling an edge or shoulder); facing (cutting on an end); turning threads (usually external but can be internal); roughing (high-volume metal removal); and finishing (final light cuts). Performed on lathes, turning centers, chucking machines, automatic screw machines and similar machines.