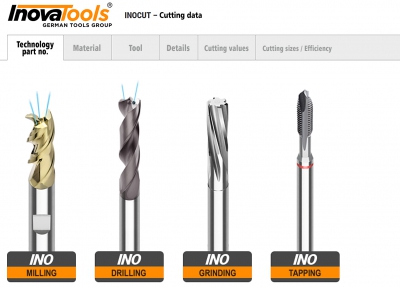
In an age of smartphones, laptops and tablets, ordering tools online easily and conveniently is not witchcraft. High-performance apps have made the process simple enough for anyone to use. However, you have to go into greater detail to separate the wheat from the chaff, for example, identifying the right tool for a particular cutting application by using the cutting data calculator. Easy to understand, error-free, secure and fast are the key requirements. With INOCUT, tool manufacturer Inovatools has provided a high-performance application for this purpose. It is available at www.schnittdaten.eu and www.inovatools.eu.
Buying a tool is a matter of trust. Personal contact between manufacturer and customer through expert, customized, in-person consulting on the customer's premises or by telephone continue to be important sales channels. Douglas Kline, managing director at Inovatools USA LLC, said, "In addition to personal contact with the aid of our catalogs and brochures, growing numbers of existing and new customers are choosing to buy through our online shop, INOSHOP. By going there, they can stay up to date around the clock, find out about availability and enjoy the many benefits of a modern web-based ordering system."
Inovatools also provides useful apps, which make purchasing even easier. For example, there is the INOQR code reader, which builds a digital bridge from the tool catalog to INOSHOP. Once the desired tool has been scanned, the user is directed to the correct item number.
The INOCUT cutting data app provides a specific recommendation for cutting values depending on the working cross-section, material and tool. Depending on the technology selected, such as milling, drilling, grinding or tapping, six material groups are available with a total of 24 subcategories. Tools are then offered and sorted by first choice on the basis of a tool category or shape search.
Depending on the technology, a specific cross-section, copy milling or the maximum machine speed can be calculated via a checkbox. The efficiency (machining volume – Q) is shown by means of a diagram and can be compared with specific tools via a computer function.
Kline said, "Whether you're on the road, working at the machine or in a meeting, INOCUT means that you can find products quickly and easily, enabling you to make an informed decision and make a purchase quickly. After all, INOCUT is linked directly to our INOSHOP, which means that the tools can be ordered directly."
Contact Details
Related Glossary Terms
- gang cutting ( milling)
gang cutting ( milling)
Machining with several cutters mounted on a single arbor, generally for simultaneous cutting.
- grinding
grinding
Machining operation in which material is removed from the workpiece by a powered abrasive wheel, stone, belt, paste, sheet, compound, slurry, etc. Takes various forms: surface grinding (creates flat and/or squared surfaces); cylindrical grinding (for external cylindrical and tapered shapes, fillets, undercuts, etc.); centerless grinding; chamfering; thread and form grinding; tool and cutter grinding; offhand grinding; lapping and polishing (grinding with extremely fine grits to create ultrasmooth surfaces); honing; and disc grinding.
- milling
milling
Machining operation in which metal or other material is removed by applying power to a rotating cutter. In vertical milling, the cutting tool is mounted vertically on the spindle. In horizontal milling, the cutting tool is mounted horizontally, either directly on the spindle or on an arbor. Horizontal milling is further broken down into conventional milling, where the cutter rotates opposite the direction of feed, or “up” into the workpiece; and climb milling, where the cutter rotates in the direction of feed, or “down” into the workpiece. Milling operations include plane or surface milling, endmilling, facemilling, angle milling, form milling and profiling.
- tapping
tapping
Machining operation in which a tap, with teeth on its periphery, cuts internal threads in a predrilled hole having a smaller diameter than the tap diameter. Threads are formed by a combined rotary and axial-relative motion between tap and workpiece. See tap.