Contact Details
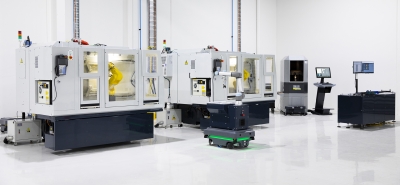
ANCA’s launch of integrated solutions with AIMS, connects sequential processes in tool manufacturing, to bank the benefits of automation and integration. AIMS facilitates streamlined tool production, linking separate processes to each other and factory IT systems. The future of toolmaking is here, with AIMS providing versatile, modular options for common manufacturing challenges to optimize cutting tool production.
AIMS offers functionality that is adaptable to each factory’s needs; from smaller scale, data-based options to the full AIMS setup across a series of machines with endless possibilities. Central to any AIMS system is the AIMS Server that manages data flows between the elements of the AIMS system and established IT platforms, such as your ERP system. Building on this, customers can choose from a suite of “auto” solutions for reducing production costs, resolving labor challenges and integrating systems to improve product and process quality. From transferring tools between operations with AutoFetch robot options; fully automated tool measurement and process compensation using AutoComp; and managing data via the AutoSet hub - AIMS delivers streamlined manufacturing, with connected tool production processes integrated to IT systems that takes tool production to the next level.
“ANCA is here to provide tool manufacturers with solutions to support production that work across all industries and applications and expand to complete tool production needs. This is a new landscape for interconnected technology, working end to end,” said Chris Hegarty, ANCA Group CEO.
“Integration and automation solutions provide infrastructure to manufacture tools with increased productivity and higher quality. ANCA has the industry-leading software and control capabilities to deliver a system for production management that tackles time, cost and labor inefficiencies where it counts.”
“We are delighted to be accelerating into the fourth industrial revolution with advanced, smart factory solutions for cutting tool makers – intelligent automation for connecting processes and data management.”
Connect, automate and create with AIMS
AIMS Project Lead, Duncan Thompson said: “Automated options that can be applied in the real world and tailored to a machine shop’s challenges, mean that tool manufacturers can reap the advantages of integrated processes and systems in a practical way.”
Over 70% of ANCA customers seek machines with robotic functionality. ANCA’s world-first technology developments utilize automation to gain efficiencies and have helped reduce production costs by 50%.
Duncan Thompson explains: “Our customers continue to look for custom solutions for increased automation in their operations and AIMS is ANCA’s holistic response; a tangible option for a smarter factory. Automation that works best is targeted to repetitive processes that can occur alongside value-adding individual skills. AIMS slots in to seamlessly automate routine processes.”
“Seeing this level of integration in action is pretty amazing. Our easy to view, virtual demonstration really highlights the ways that AIMS works to boost tool production. AIMS can be deployed to a single process or across an entire production line, towards end to end tool manufacturing.”
The AIMS online demo exhibits interconnected grinding technology solutions that eliminate wasteful manual handling, reduce machine downtime in between batches and take away the need to have operators constantly monitoring and adjusting production machines.
Related Glossary Terms
- grinding
grinding
Machining operation in which material is removed from the workpiece by a powered abrasive wheel, stone, belt, paste, sheet, compound, slurry, etc. Takes various forms: surface grinding (creates flat and/or squared surfaces); cylindrical grinding (for external cylindrical and tapered shapes, fillets, undercuts, etc.); centerless grinding; chamfering; thread and form grinding; tool and cutter grinding; offhand grinding; lapping and polishing (grinding with extremely fine grits to create ultrasmooth surfaces); honing; and disc grinding.