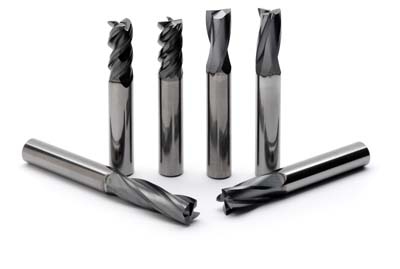
Achieve economy through production performance with Seco Tool Inc.'s new Jabro-Solid2 (Solid Square) carbide milling cutters available in sizes from 1⁄8" to 1". These versatile square-shoulder mills are for general machining applications across a wide range of material groups from carbon steels to gray cast iron to stainless and super alloys in both wet and dry applications. Benefits include reduced inventory, lower cost per cutter, lower cost per part and fewer tool changes, according to the company.
Seco is offering the Solid2 in a JS510 series for all basic operations in steel, stainless, and cast irons and available in 2-, 3- and 4-flute cutters for side milling and/or slotting. This series features an increased core diameter allowing larger cuts for reduced cycle times and costs. Also available is a higher performance JS550 series featuring double-core technology for added stability and reduced tool deflection, thus enabling higher cutting data. This series is available in 3- and 4-flute designs for slotting and side milling. The tools have a differential-pitch design for chatter-free machining. Both families are finished with a proprietary Siron-A coating and special edge preparation for smooth chip flow and longer tool life.
Contact Details
Related Glossary Terms
- alloys
alloys
Substances having metallic properties and being composed of two or more chemical elements of which at least one is a metal.
- carbon steels
carbon steels
Known as unalloyed steels and plain carbon steels. Contains, in addition to iron and carbon, manganese, phosphorus and sulfur. Characterized as low carbon, medium carbon, high carbon and free machining.
- cast irons
cast irons
Cast ferrous alloys containing carbon in excess of solubility in austenite that exists in the alloy at the eutectic temperature. Cast irons include gray cast iron, white cast iron, malleable cast iron and ductile, or nodular, cast iron. The word “cast” is often left out.
- edge preparation
edge preparation
Conditioning of the cutting edge, such as a honing or chamfering, to make it stronger and less susceptible to chipping. A chamfer is a bevel on the tool’s cutting edge; the angle is measured from the cutting face downward and generally varies from 25° to 45°. Honing is the process of rounding or blunting the cutting edge with abrasives, either manually or mechanically.
- gang cutting ( milling)
gang cutting ( milling)
Machining with several cutters mounted on a single arbor, generally for simultaneous cutting.
- milling
milling
Machining operation in which metal or other material is removed by applying power to a rotating cutter. In vertical milling, the cutting tool is mounted vertically on the spindle. In horizontal milling, the cutting tool is mounted horizontally, either directly on the spindle or on an arbor. Horizontal milling is further broken down into conventional milling, where the cutter rotates opposite the direction of feed, or “up” into the workpiece; and climb milling, where the cutter rotates in the direction of feed, or “down” into the workpiece. Milling operations include plane or surface milling, endmilling, facemilling, angle milling, form milling and profiling.
- slotting
slotting
Machining, normally milling, that creates slots, grooves and similar recesses in workpieces, including T-slots and dovetails.