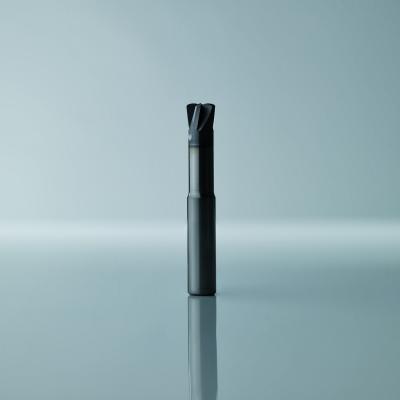
Seco has expanded the high-feed machining applicability of its Jabro-HFM JHF980 solid-carbide endmill with new 4- and 5-flute options. The additional flutes allow part manufacturers in industries such as aerospace and medical to achieve maximum productivity when performing face, slot and select plunge milling operations.
Seco applied the latest design and grinding developments to successfully increase the number of flutes on the JHF980, allowing it to provide double the feed rate capability of previous Jabro endmills. Test results indicate the JHF980 4- and 5- flute cutters also offer increased tool life over earlier designs when applied at the same table feed rates. Metal removal for the new JHF980 high-feed cutters is more aggressive compared to conventional tools and milling methods. As such, manufacturers can lower their production expenses and stay more competitive. High-feed machining pairs shallow axial depths of cut with accelerated table feed rates for increased metal removal.
Furthermore, cutting forces are directed axially into the spindle, thereby stabilizing the operation, minimizing vibration and lessening wear on the machine tool.
JHF980 end mills feature an ultrafine carbide grade and a monolayer TiAIN coating, which contributes to their success in high-feed applications. The coating also helps lower operating costs by eliminating the need for coolant in high-temperature situations. The TiAIN layer insulates the cutters and transfers heat into the chips. Cutting diameters for the 4-flute JHF980 range from 2 mm to 6 mm, while the 5-flute version spans 8 mm to 12 mm. Both cutters are available in 1.5xD, 5xD and 7xD lengths. Overall, JHF980 cutters cover a wide application area that involves processing a variety of parts from steel to exotic metals. Part examples include casing pockets, knee caps and 3D cavities. The cutters also reduce production costs when processing shallow and deep pockets.
Optimal application of the JHF980 cutters is dependent on several factors, from the age of the machine tool being used to the part size being cut. For example, the cutters can run at maximum feed rates when applied alongside a highly rigid, modern machine tool. Proper programming is also important to ensure optimisation of the cutter path. With the right CAM program, it is possible for the JHF980 to perform Z-level finishes on the sides of a part. Seco can assist manufacturers in developing the most appropriate high-feed machining strategies for their operations.
Contact Details
Related Glossary Terms
- computer-aided manufacturing ( CAM)
computer-aided manufacturing ( CAM)
Use of computers to control machining and manufacturing processes.
- coolant
coolant
Fluid that reduces temperature buildup at the tool/workpiece interface during machining. Normally takes the form of a liquid such as soluble or chemical mixtures (semisynthetic, synthetic) but can be pressurized air or other gas. Because of water’s ability to absorb great quantities of heat, it is widely used as a coolant and vehicle for various cutting compounds, with the water-to-compound ratio varying with the machining task. See cutting fluid; semisynthetic cutting fluid; soluble-oil cutting fluid; synthetic cutting fluid.
- endmill
endmill
Milling cutter held by its shank that cuts on its periphery and, if so configured, on its free end. Takes a variety of shapes (single- and double-end, roughing, ballnose and cup-end) and sizes (stub, medium, long and extra-long). Also comes with differing numbers of flutes.
- feed
feed
Rate of change of position of the tool as a whole, relative to the workpiece while cutting.
- flutes
flutes
Grooves and spaces in the body of a tool that permit chip removal from, and cutting-fluid application to, the point of cut.
- gang cutting ( milling)
gang cutting ( milling)
Machining with several cutters mounted on a single arbor, generally for simultaneous cutting.
- grinding
grinding
Machining operation in which material is removed from the workpiece by a powered abrasive wheel, stone, belt, paste, sheet, compound, slurry, etc. Takes various forms: surface grinding (creates flat and/or squared surfaces); cylindrical grinding (for external cylindrical and tapered shapes, fillets, undercuts, etc.); centerless grinding; chamfering; thread and form grinding; tool and cutter grinding; offhand grinding; lapping and polishing (grinding with extremely fine grits to create ultrasmooth surfaces); honing; and disc grinding.
- milling
milling
Machining operation in which metal or other material is removed by applying power to a rotating cutter. In vertical milling, the cutting tool is mounted vertically on the spindle. In horizontal milling, the cutting tool is mounted horizontally, either directly on the spindle or on an arbor. Horizontal milling is further broken down into conventional milling, where the cutter rotates opposite the direction of feed, or “up” into the workpiece; and climb milling, where the cutter rotates in the direction of feed, or “down” into the workpiece. Milling operations include plane or surface milling, endmilling, facemilling, angle milling, form milling and profiling.
- plunge milling
plunge milling
Highly productive method of metal removal in which an axial machining operation is performed in a single tool sequence. The tool makes a series of overlapping, drill-like plunges to remove part of a cylindrical plug of material one after another. Because of the increased rigidity of a Z-axis move, the tool can cover a large cross-section of material.
- toolpath( cutter path)
toolpath( cutter path)
2-D or 3-D path generated by program code or a CAM system and followed by tool when machining a part.