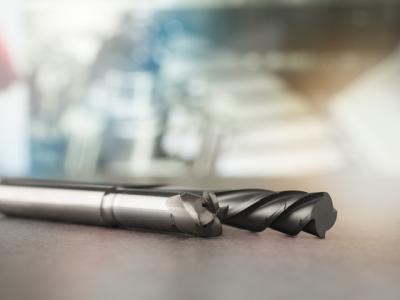
For aerospace shops struggling with holemaking and milling operations in hybrid stacked materials, the new JC899 Hybrid Stack finisher and JC898 rougher from Seco Tools are ideal solutions. The finisher, JC899, features a patented two-in-one geometry that eliminates problems with delamination and fiber pulling out when working with stacked materials such as carbon fibre reinforced polymer (CFRP) combined with titanium or aluminum. Together with the JC898 rougher, the JC899 finisher offers three to six times more tool life over conventional drill/reamer combinations and generates pollution-free holes and side walls with perfect surface finishes to deliver up to 300 percent greater process efficiency.
The JC898 offers an advanced frontal teeth design suitable for helical interpolation, which reduces cutting forces and minimizes the risk of delamination when working with hybrid stacked materials that can put lots of pressure on Z-axis drilling operations and generate chips that can damage the machined hole’s surface finish. The new tools achieve faster, cleaner holes and side wall finishes without the extra time-consuming step of removing chips that lodge in between the stacked material layers.
The patented JC899 finishing tool utilizes a two-in-one geometry to eliminate chip pollution, removing the need for manufacturers to unstack and clean hybrid stacked materials after machining. The diamond-based STAX coating ensures reliable processes and high-quality products, while the double geometry’s left-hand helix prevents delamination, fiber pullout and chip marks from damaging the workpiece’s surface.
As opposed to boring tools that involve time-consuming benchwork and complicated measuring for proper part repositioning, the JC898 and JC899 eliminate such post-machining work to significantly simplify CFRP-titanium and CFRP-aluminum hybrid material holemaking operations. The resulting processes are twice as fast as those performed with alternative solutions and tool life has been doubled as well.
In addition, the JC898 and JC899 offer numerous advantages for helical interpolation and side milling applications, increasing process stability and speed at the same time they minimize the need for post-machining operations and benchwork. By reducing stress imparted to stacked materials during machining, these tools improve workpiece quality, particularly for CFRP-titanium applications that are otherwise likely to produce burrs.
The JC898 and JC899 handle lengths or stack heights ranging from 15 to 60 mm. The JC898 is available in diameters of 8 or 15 mm, while the JC899 is available in 8.5 and 14.8 mm (finisher), as well as in a 0.375" diameter.
Contact Details
Related Glossary Terms
- boring
boring
Enlarging a hole that already has been drilled or cored. Generally, it is an operation of truing the previously drilled hole with a single-point, lathe-type tool. Boring is essentially internal turning, in that usually a single-point cutting tool forms the internal shape. Some tools are available with two cutting edges to balance cutting forces.
- finishing tool
finishing tool
Tool, belt, wheel or other cutting implement that completes the final, precision machining step/cut on a workpiece. Often takes the form of a grinding, honing, lapping or polishing tool. See roughing cutter.
- gang cutting ( milling)
gang cutting ( milling)
Machining with several cutters mounted on a single arbor, generally for simultaneous cutting.
- interpolation
interpolation
Process of generating a sufficient number of positioning commands for the servomotors driving the machine tool so the path of the tool closely approximates the ideal path. See CNC, computer numerical control; NC, numerical control.
- milling
milling
Machining operation in which metal or other material is removed by applying power to a rotating cutter. In vertical milling, the cutting tool is mounted vertically on the spindle. In horizontal milling, the cutting tool is mounted horizontally, either directly on the spindle or on an arbor. Horizontal milling is further broken down into conventional milling, where the cutter rotates opposite the direction of feed, or “up” into the workpiece; and climb milling, where the cutter rotates in the direction of feed, or “down” into the workpiece. Milling operations include plane or surface milling, endmilling, facemilling, angle milling, form milling and profiling.