Contact Details
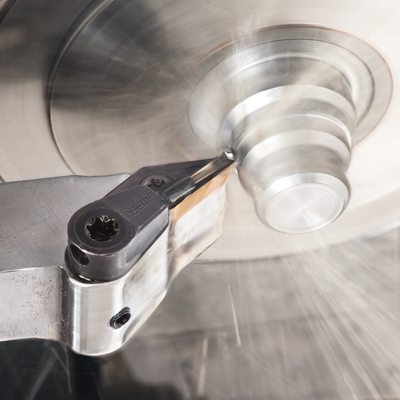
ISCAR is expanding the range of SWISSTURN square-shank toolholders by adding new tools for high pressure coolant and also tools without the internal coolant feature. The new tools were designed for Swiss-type automatics and CNC machines. They include tools for ISO standard screw-clamped and lever-lock rhombic 80 degree (C-type), 55 degree (D-type) and 35 degree (V-type) inserts, all with 7 degree positive flank relief inclination.
Due to the confined space and tight arrangement of the tools inside Swiss-type machines, the SWISSTURN tools feature small shank sizes with insert cutting edges "in line" with the shank (f=b), to avoid collision. The Swiss-type automatics and CNC machines are widely used in medical, aerospace, automotive, electronics and general metalworking, and for machining complex, precision parts with a length to diameter ratio that is subject to deflection in the turning process.
The new tools can be used for longitudinal, face and profiling applications on small diameter parts.
The use of high pressure coolant is growing as manufacturers are looking for ways to reduce cutting time, improve machining process reliability and achieve longer tool life. ISCAR's new JHP tools provide all of these advantages. Shorter chips are easily managed and they do not tangle around the workpiece or machine parts, so there is no need to stop the process frequently.
Usually, in conventional cooling, the chip prevents the coolant from reaching the insert rake face in the cutting zone. The coolant stream of the JHP tools is directed precisely between the insert rake face and the flowing chip. This results in longer tool life and a much more reliable process, according to the company.
Related Glossary Terms
- computer numerical control ( CNC)
computer numerical control ( CNC)
Microprocessor-based controller dedicated to a machine tool that permits the creation or modification of parts. Programmed numerical control activates the machine’s servos and spindle drives and controls the various machining operations. See DNC, direct numerical control; NC, numerical control.
- coolant
coolant
Fluid that reduces temperature buildup at the tool/workpiece interface during machining. Normally takes the form of a liquid such as soluble or chemical mixtures (semisynthetic, synthetic) but can be pressurized air or other gas. Because of water’s ability to absorb great quantities of heat, it is widely used as a coolant and vehicle for various cutting compounds, with the water-to-compound ratio varying with the machining task. See cutting fluid; semisynthetic cutting fluid; soluble-oil cutting fluid; synthetic cutting fluid.
- metalworking
metalworking
Any manufacturing process in which metal is processed or machined such that the workpiece is given a new shape. Broadly defined, the term includes processes such as design and layout, heat-treating, material handling and inspection.
- profiling
profiling
Machining vertical edges of workpieces having irregular contours; normally performed with an endmill in a vertical spindle on a milling machine or with a profiler, following a pattern. See mill, milling machine.
- rake
rake
Angle of inclination between the face of the cutting tool and the workpiece. If the face of the tool lies in a plane through the axis of the workpiece, the tool is said to have a neutral, or zero, rake. If the inclination of the tool face makes the cutting edge more acute than when the rake angle is zero, the rake is positive. If the inclination of the tool face makes the cutting edge less acute or more blunt than when the rake angle is zero, the rake is negative.
- relief
relief
Space provided behind the cutting edges to prevent rubbing. Sometimes called primary relief. Secondary relief provides additional space behind primary relief. Relief on end teeth is axial relief; relief on side teeth is peripheral relief.
- shank
shank
Main body of a tool; the portion of a drill or similar end-held tool that fits into a collet, chuck or similar mounting device.
- turning
turning
Workpiece is held in a chuck, mounted on a face plate or secured between centers and rotated while a cutting tool, normally a single-point tool, is fed into it along its periphery or across its end or face. Takes the form of straight turning (cutting along the periphery of the workpiece); taper turning (creating a taper); step turning (turning different-size diameters on the same work); chamfering (beveling an edge or shoulder); facing (cutting on an end); turning threads (usually external but can be internal); roughing (high-volume metal removal); and finishing (final light cuts). Performed on lathes, turning centers, chucking machines, automatic screw machines and similar machines.