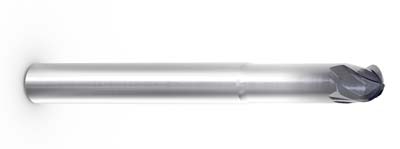
The latest Jabro-Solid2 JS530 Series of ball nose cutters from Seco brings increased flexibility, speed and efficiency to copy and profile milling, as well as slotting and side milling operations.
Consisting of the JS532, JS533 and JS534, the Jabro-Solid2 JS530 series is ideal for 2.5D and 3D machining applications in a broad range of materials, including steel, stainless steel, cast iron and titanium. All geometries are available in normal, long and extra long lengths.
Overall features of the JS530 series include radial relief for strong cutting edges, a polished Siron-A coating for reducing friction and heat buildup, increased core diameters related to the number of teeth for added stability, and edge prep for a controlled wear pattern.
Manufacturers incorporating the JS530 ball nose cutters benefit from stronger flutes for improved process stability, increased tool life, better surface finishes, accurate workpiece dimensions at higher feed rates and reduced re-work.
JS532 employs two flutes and cutting diameters that range from .031" to .750", easily handling roughing, semi-roughing, semi-finishing and finishing applications. JS533 features the same cutting diameters as the JS532, but uses three flutes for semiroughing, semi-finishing and finishing applications. Lastly, JS534 handles semifinishing and finishing applications with four flutes and a cutting diameter range of .063" to .750".
Contact Details
Related Glossary Terms
- feed
feed
Rate of change of position of the tool as a whole, relative to the workpiece while cutting.
- flutes
flutes
Grooves and spaces in the body of a tool that permit chip removal from, and cutting-fluid application to, the point of cut.
- gang cutting ( milling)
gang cutting ( milling)
Machining with several cutters mounted on a single arbor, generally for simultaneous cutting.
- milling
milling
Machining operation in which metal or other material is removed by applying power to a rotating cutter. In vertical milling, the cutting tool is mounted vertically on the spindle. In horizontal milling, the cutting tool is mounted horizontally, either directly on the spindle or on an arbor. Horizontal milling is further broken down into conventional milling, where the cutter rotates opposite the direction of feed, or “up” into the workpiece; and climb milling, where the cutter rotates in the direction of feed, or “down” into the workpiece. Milling operations include plane or surface milling, endmilling, facemilling, angle milling, form milling and profiling.
- relief
relief
Space provided behind the cutting edges to prevent rubbing. Sometimes called primary relief. Secondary relief provides additional space behind primary relief. Relief on end teeth is axial relief; relief on side teeth is peripheral relief.
- slotting
slotting
Machining, normally milling, that creates slots, grooves and similar recesses in workpieces, including T-slots and dovetails.