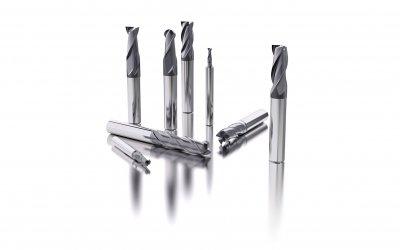
In its continued effort to provide the most cost-effective tooling solutions available, Seco Tools has announced a new family of flexible, highly productive solid end mills, the Seco JSE510 series. Redesigned to offer the rigidity, chip control and tool life to achieve the lowest possible costs per meter machined in steels, stainless steels, cast iron, titanium and some aluminums, these solid end mills provide exceptional process reliability across a broad application range.
New design combines reliability and unparalleled versatility
The reoptimized design of the new JSE510 offers unparalleled versatility based on the previous version of this product range. The new series targets general engineering, contract manufacturers and job shops, as well as the aerospace, medical and automotive industries. The design is reoptimized to stand up to tough milling applications with a versatile carbide grade, advanced polished SIRA coatings and a strong, sharp cutting edge. To extend tool life further, these tools offer vibration-damping variable pitch design and optimized helix.
"These solid end mills offer productivity in less-stable machining conditions or when pushed hard to balance productivity and tool life cost effectively," said Rob Mulders, Solid End Mills Global Product Manager. "This versatility makes the JSE510 series particularly useful when shops face increased costs in required tooling because of a greater variety of applications and materials. For these shops, the new tool series’ expanded application window allows them to reduce their tooling inventory without affecting their ability to maximize throughput."
Multiple tools, geometries and lengths
The Seco JSE510 family includes 216 tools in four geometries, with two length variants in the three and four-flute version, normal (LV2) and long (LV3). The two-flute JSE512 easily handles the large chips produced in helical interpolation or peck drilling, keyways and slotting applications, while the three-flute JSE513 offers universal milling performance for ramping, full slotting and side milling. The four-flute JSE514 is ideal for optimized side milling and slotting, as well as dynamic milling. Finally, the ball-nose end mill geometry of the JSB512 offers the flexibility required for finishing parts and other ball-nose applications.
For additional information about the features and performance of the new Seco JSE510 series, visit the Seco solid end mills product page.
Contact Details
Related Glossary Terms
- gang cutting ( milling)
gang cutting ( milling)
Machining with several cutters mounted on a single arbor, generally for simultaneous cutting.
- interpolation
interpolation
Process of generating a sufficient number of positioning commands for the servomotors driving the machine tool so the path of the tool closely approximates the ideal path. See CNC, computer numerical control; NC, numerical control.
- milling
milling
Machining operation in which metal or other material is removed by applying power to a rotating cutter. In vertical milling, the cutting tool is mounted vertically on the spindle. In horizontal milling, the cutting tool is mounted horizontally, either directly on the spindle or on an arbor. Horizontal milling is further broken down into conventional milling, where the cutter rotates opposite the direction of feed, or “up” into the workpiece; and climb milling, where the cutter rotates in the direction of feed, or “down” into the workpiece. Milling operations include plane or surface milling, endmilling, facemilling, angle milling, form milling and profiling.
- milling machine ( mill)
milling machine ( mill)
Runs endmills and arbor-mounted milling cutters. Features include a head with a spindle that drives the cutters; a column, knee and table that provide motion in the three Cartesian axes; and a base that supports the components and houses the cutting-fluid pump and reservoir. The work is mounted on the table and fed into the rotating cutter or endmill to accomplish the milling steps; vertical milling machines also feed endmills into the work by means of a spindle-mounted quill. Models range from small manual machines to big bed-type and duplex mills. All take one of three basic forms: vertical, horizontal or convertible horizontal/vertical. Vertical machines may be knee-type (the table is mounted on a knee that can be elevated) or bed-type (the table is securely supported and only moves horizontally). In general, horizontal machines are bigger and more powerful, while vertical machines are lighter but more versatile and easier to set up and operate.
- pitch
pitch
1. On a saw blade, the number of teeth per inch. 2. In threading, the number of threads per inch.
- slotting
slotting
Machining, normally milling, that creates slots, grooves and similar recesses in workpieces, including T-slots and dovetails.
- stainless steels
stainless steels
Stainless steels possess high strength, heat resistance, excellent workability and erosion resistance. Four general classes have been developed to cover a range of mechanical and physical properties for particular applications. The four classes are: the austenitic types of the chromium-nickel-manganese 200 series and the chromium-nickel 300 series; the martensitic types of the chromium, hardenable 400 series; the chromium, nonhardenable 400-series ferritic types; and the precipitation-hardening type of chromium-nickel alloys with additional elements that are hardenable by solution treating and aging.