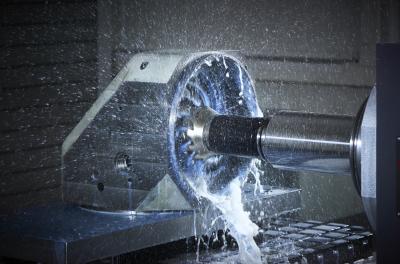
UnionChemnitz has developed a new precision boring mill. The KCG was developed to fill the gap in the market between a classic boring mill and a jig boring machine in terms of precision and price-performance ratio. The oldest existing machine tool manufacturer in Europe used its 160 years of experience to design a precision boring mill whose accuracy is significantly higher than that of a classic horizontal boring mill, yet comes with a classic HBM’s flexibility.
“Machine shops in the USA as well as Europe struggle with their classic boring mills when they have to meet the tight tolerances that more demanding machining tasks require,” says Thomas Grimm, senior sales manager at UnionChemnitz. “That is why we designed a boring mill that unites the advantages of a classic boring mill with those of a jig boring machine.” The precision boring mill KCG is based on the reliable planer-type boring mills by UnionChemnitz. “These offer the best design preconditions for highly precise machining results. A myriad of small optimizations and the introduction of a special thermal management result in a completely new level of machining performance. We are the first to enter a vacant market segment here.”
The excellent precision regarding both positioning accuracy and geometrical precision is achieved by optimized ribbing for an increased stiffness of the machine bed and column, linear guideways and hand-scraped guides. The increased table stability (GGG50) and the precision-ground table surface allow for extremely accurate machining of the most demanding workpieces. In addition, high-precision measuring devices in all axes monitor the machining performance at all times.
“We have increased the thermal stability of the machine through various optimizations,” Grimm explains. “One example is the longitudinal compensation of the boring spindle.” The improved thermal management also features a cooling unit with a heating and a cooling device, temperature-controlled gear oil cooling, water-cooled main spindle and Y-axis and an air-cooled head assembly.
The precision boring mill meets tolerances of less than 10 µ/2,500 mm (98”) in terms of planeness and less than 8 µ/m2 in terms of evenness. At the same time, the KCG is flexible thanks to the boring spindle, which allows for the machining of contours deep within workpieces. Compared to a jig boring machine, it offers greater degrees of freedom and, therefore, a broader range of machining applications. However, the investment cost is significantly lower than that of a jig boring machine.
Thorsten Mehlhorn, president and COO of Germany-based gearbox manufacturer RSGetriebe, decided to invest in the new precision boring mill in 2015. He found himself in a predicament that is familiar to many machine shops: “Machining our products requires tight tolerances, which cannot be met using a classic boring mill”, he says. “Acquiring a jig boring machine was not an option for us, due to the disproportionately high investment costs on the one hand and the limited degrees of freedom on the other.”
Instead, Mehlhorn looked for an alternative solution and found the new precision boring mill developed by UnionChemnitz. Precision is crucial for the products machined at RSGetriebe: the company is an expert in manufacturing high-quality special gearboxes for a broad range of industries, as well as milling heads. Its high-performance custom gearboxes are used by leading companies in the plastics and machine tool industries among others, and for test stands in the automotive industry.
RSGetriebe decided to invest in a new machine tool to increase its vertical range of manufacture. The goal: to expand the product range and reduce the number of components acquired by external suppliers. It soon became clear, however, that a classic boring mill would not fulfill RSGetriebe’s high machining standards: “The size of the workpieces and the metalcutting performance had to be considered in the choice of machine tool, but the required flexibility was a very important factor in the decision process, too. On the one hand, a broad range of workpieces had to be machined; besides milling units, that includes our entire gearbox portfolio. On the other hand, we also needed increased precision, especially for the production of milling heads,” Mehlhorn recounts.
At times, the workpieces at RSGetriebe have to be machined with a precision of under 0.005 mm (0.0002”) regarding parallelism and coaxiality of surfaces and boring holes. “A classic boring mill cannot meet our precision standards without an appropriate measuring strategy,” Mehlhorn says. “The KCG, however, reliably obtains the outstanding precision we required and saved us the investment in a costly jig boring machine.”
The KCG with a spindle diameter of 125 mm (5”) machines even the most demanding workpieces with repeatable precision. The new precision boring mill was installed at the RSGetriebe headquarters in Sonthofen in 2015. Since then, it has demonstrated its outstanding accuracy and reliability while machining the housings of milling units for boring mills, as well as many different types of gear housings. Gearboxes with volumes of 1.5 to 2 m3 (5 to 7 ft3) and weights of up to 6 tons can now be manufactured effortlessly.
An additional challenge for the machine tool is the mix of different materials which have to be machined at RSGetriebe. For that reason, it is equipped for dry and wet machining. “We can machine both steel and cast-iron workpieces with these two modes. That significantly expands the application range of the KCG 125,” Mehlhorn states.
In order to ensure stable temperatures during the machining process, the precision boring mill is equipped with an air-conditioned housing, including a roof and an extraction system. The machining conditions are kept at a constant level; even large temperature variations in the production facility do not affect them. An operating platform is situated within the air-conditioned housing. “From here, the work area is easily accessible and the whole process can be monitored manually. That is a great advantage for our machine operators in their everyday routine,” Mehlhorn observes.
Since efficiency is an important factor in the manufacturing of gearboxes, UnionChemnitz installed a pick-up station for changing milling heads. Milling tools are changed automatically during the machining process via a 60-pocket tool changer. Mehlhorn is pleased with the increased efficiency in his production facility: “The pick-up station, the automatic toolchanger and the different milling units have significantly reduced the machining times.”
Thanks to the new precision boring mill, the vertical range of manufacture at RSGetriebe has been increased. “We have to purchase fewer components. On top of that, we have raised the quality of our products and reduced the unit costs at the same time. Thanks to the greater degrees of freedom, we were able to strongly improve on non-productive time,” Mehlhorn reports. His summary: “The KG series by UnionChemnitz with its increased accuracy is a very interesting investment option compared to a jig boring machine. The machine’s precision is nearly identical and it offers much higher degrees of freedom and greater traverse.”
Contact Details
Related Glossary Terms
- automatic toolchanger
automatic toolchanger
Mechanism typically included in a machining center that, on the appropriate command, removes one cutting tool from the spindle nose and replaces it with another. The changer restores the used tool to the magazine and selects and withdraws the next desired tool from the storage magazine. The changer is controlled by a set of prerecorded/predetermined instructions associated with the part(s) to be produced.
- boring
boring
Enlarging a hole that already has been drilled or cored. Generally, it is an operation of truing the previously drilled hole with a single-point, lathe-type tool. Boring is essentially internal turning, in that usually a single-point cutting tool forms the internal shape. Some tools are available with two cutting edges to balance cutting forces.
- boring machine
boring machine
Similar to a turning machine except that the cutting tool (single-point or multiple-cutting-edge), rather than the workpiece, rotates to perform internal cuts. However, boring can be accomplished by holding the tool stationary and turning the workpiece. Takes a variety of vertical, slanted and horizontal forms, and has one or more spindles. Typically a large, powerful machine, it can readily hold tolerances to 0.0001". See jig boring; lathe; turning machine.
- degrees of freedom
degrees of freedom
Number of axes along which a robot, and thus the object it is holding, can be manipulated. Most robots are capable of maneuvering along the three basic Cartesian axes (X, Y, Z). More sophisticated models may move in six or more axes. See axis.
- gang cutting ( milling)
gang cutting ( milling)
Machining with several cutters mounted on a single arbor, generally for simultaneous cutting.
- jig
jig
Tooling usually considered to be a stationary apparatus. A jig assists in the assembly or manufacture of a part or device. It holds the workpiece while guiding the cutting tool with a bushing. A jig used in subassembly or final assembly might provide assembly aids such as alignments and adjustments. See fixture.
- jig boring
jig boring
High-precision machining (a sophisticated form of milling) that originally pertained to jig and fixture manufacturing. Basic jig-boring processes include centering, drilling, reaming, through and step boring, counterboring and contouring.
- metalcutting ( material cutting)
metalcutting ( material cutting)
Any machining process used to part metal or other material or give a workpiece a new configuration. Conventionally applies to machining operations in which a cutting tool mechanically removes material in the form of chips; applies to any process in which metal or material is removed to create new shapes. See metalforming.
- milling
milling
Machining operation in which metal or other material is removed by applying power to a rotating cutter. In vertical milling, the cutting tool is mounted vertically on the spindle. In horizontal milling, the cutting tool is mounted horizontally, either directly on the spindle or on an arbor. Horizontal milling is further broken down into conventional milling, where the cutter rotates opposite the direction of feed, or “up” into the workpiece; and climb milling, where the cutter rotates in the direction of feed, or “down” into the workpiece. Milling operations include plane or surface milling, endmilling, facemilling, angle milling, form milling and profiling.
- milling machine ( mill)
milling machine ( mill)
Runs endmills and arbor-mounted milling cutters. Features include a head with a spindle that drives the cutters; a column, knee and table that provide motion in the three Cartesian axes; and a base that supports the components and houses the cutting-fluid pump and reservoir. The work is mounted on the table and fed into the rotating cutter or endmill to accomplish the milling steps; vertical milling machines also feed endmills into the work by means of a spindle-mounted quill. Models range from small manual machines to big bed-type and duplex mills. All take one of three basic forms: vertical, horizontal or convertible horizontal/vertical. Vertical machines may be knee-type (the table is mounted on a knee that can be elevated) or bed-type (the table is securely supported and only moves horizontally). In general, horizontal machines are bigger and more powerful, while vertical machines are lighter but more versatile and easier to set up and operate.
- stiffness
stiffness
1. Ability of a material or part to resist elastic deflection. 2. The rate of stress with respect to strain; the greater the stress required to produce a given strain, the stiffer the material is said to be. See dynamic stiffness; static stiffness.
- toolchanger
toolchanger
Carriage or drum attached to a machining center that holds tools until needed; when a tool is needed, the toolchanger inserts the tool into the machine spindle. See automatic toolchanger.