Contact Details
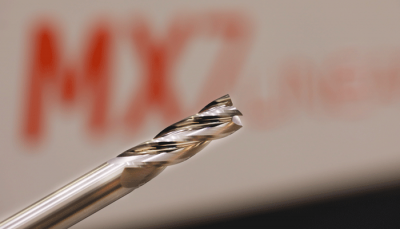
Highly polished flutes and gash surfaces improve chip evacuation and aid tool performance. The smoother surface enables swarf (or chips) to exit more freely, preventing chip packing and material build up during machining. ANCA has addressed this goal with innovations reportedly found only at the ANCA Group.
ANCA has equipped its rigid tool and cutter grinding machines with ANCA Motion’s LinX linear motor technology to provide manufacturers a new, higher level of quality toolmaking capability.
“Tools ground on our machines have a consistently high-quality cutting edge and surface finish,” reports Simon Richardson, ANCA product manager “Since the LinX motor technology was launched, customers have reported dramatically better results using the duel technologies.
“High-quality tool surface finish is a great advantage when machining softer or ductile materials, chips can stick to the carbide. If the chips created are not removed faster than they are being produced, the tool may not perform effectively. However, a better surface finish on the flute prevents the swarf from sticking onto the flute face of the tool while reducing the amount of heat that is generated when machining.”
“We realized that having a highly rigid machine with a cylindrical linear motor that assures a smooth axis movement would greatly improve the final surface finish on the tool,” Mr. Richardson. “The research and development team conducted many hours of test grinding to rigorously test our assumption of what surface finish quality we thought was possible.”
An Alicona infinite-focus XL metrology machine in ANCA’s Grinding Centre of Excellence was used to verify the results to nanometer accuracy, finding that a surface finish roughness average as low as 164.7nm, which translates to 0.16 Ra, was achieved.
“The LinX cylindrical linear motor advantage for surface finish quality is that it assures no loss of preload or rigidity when grinding tools. Also, reversal errors are eliminated and higher contouring accuracy can be maintained due to a control algorithm we use which is unique to ANCA,” Richardson said. “Tools with highly polished surfaces means better cutting edges, which will ensure extended tool life and improve the finish on the machined part. We have seen the demand for tools with a superior surface finish continue to increase and cutting tool manufacturers are producing more highly polished tools in larger quantities.”
Tips on achieving a superior tooling surface finish:
• A fine-grit wheel can form small chips during grinding, which could impart fine marks on the flute face and gash.
• Using a fine-grit also poses a challenge as the wheel must be fine enough to produce the required surface finish while maintaining a good toroid radius over a batch of tools.
• Ensure the wheel is properly trued and dressed, and balanced so that it performs as expected.
• Ensure efficient coolant delivery and fine filtration systems are in place.
Related Glossary Terms
- coolant
coolant
Fluid that reduces temperature buildup at the tool/workpiece interface during machining. Normally takes the form of a liquid such as soluble or chemical mixtures (semisynthetic, synthetic) but can be pressurized air or other gas. Because of water’s ability to absorb great quantities of heat, it is widely used as a coolant and vehicle for various cutting compounds, with the water-to-compound ratio varying with the machining task. See cutting fluid; semisynthetic cutting fluid; soluble-oil cutting fluid; synthetic cutting fluid.
- flutes
flutes
Grooves and spaces in the body of a tool that permit chip removal from, and cutting-fluid application to, the point of cut.
- grinding
grinding
Machining operation in which material is removed from the workpiece by a powered abrasive wheel, stone, belt, paste, sheet, compound, slurry, etc. Takes various forms: surface grinding (creates flat and/or squared surfaces); cylindrical grinding (for external cylindrical and tapered shapes, fillets, undercuts, etc.); centerless grinding; chamfering; thread and form grinding; tool and cutter grinding; offhand grinding; lapping and polishing (grinding with extremely fine grits to create ultrasmooth surfaces); honing; and disc grinding.
- linear motor
linear motor
Functionally the same as a rotary motor in a machine tool, a linear motor can be thought of as a standard permanent-magnet, rotary-style motor slit axially to the center and then peeled back and laid flat. The major advantage of using a linear motor to drive the axis motion is that it eliminates the inefficiency and mechanical variance caused by the ballscrew assembly system used in most CNC machines.
- metrology
metrology
Science of measurement; the principles on which precision machining, quality control and inspection are based. See precision machining, measurement.
- swarf
swarf
Metal fines and grinding wheel particles generated during grinding.