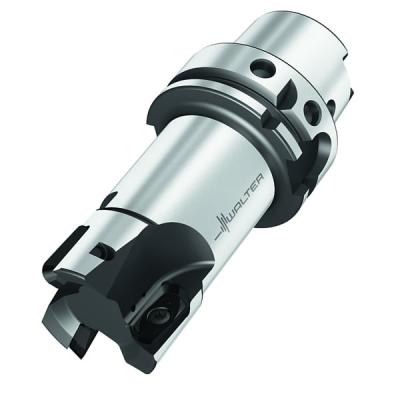
The new M2131 Sky·tec Ramping Cutter from Walter reportedly brings new, higher levels of process reliability to the machining of nonferrous metals such as the aluminum wrought alloys or aluminum lithium alloys often used in aircraft structural components. The cutter allows shorter machining time due to its high metal-removal rate and delivers long tool life thanks to the low build-up on the cutting edge.
The new M2131 boasts protection against centrifugal force at the insert contact surface, which helps ensure the tool’s high level of process reliability even at maximum speeds, and its V-shaped cutting edge for ramping promotes rough milling and semi-finishing of pockets with high chip volume.
This 90° shoulder milling cutter with ramping capability has a maximum cutting depth of 0.59 in. or 0.78 in. (15 or 20 mm), a diameter range of 0.98 in. to 3.14 in. (25 to 80 mm), and a high level of radial runout accuracy. The M2131, with integral cooling for MQL or emulsion, has a finely balanced basic body, with different interfaces such as HSK, ScrewFit, cylindrical shank or shell mill mount. It has two sizes of indexable inserts with various corner radii, and employs the new milling grade WNN15, known for its extremely long tool life.
Contact Details
Related Glossary Terms
- alloys
alloys
Substances having metallic properties and being composed of two or more chemical elements of which at least one is a metal.
- emulsion
emulsion
Suspension of one liquid in another, such as oil in water.
- gang cutting ( milling)
gang cutting ( milling)
Machining with several cutters mounted on a single arbor, generally for simultaneous cutting.
- metal-removal rate
metal-removal rate
Rate at which metal is removed from an unfinished part, measured in cubic inches or cubic centimeters per minute.
- milling
milling
Machining operation in which metal or other material is removed by applying power to a rotating cutter. In vertical milling, the cutting tool is mounted vertically on the spindle. In horizontal milling, the cutting tool is mounted horizontally, either directly on the spindle or on an arbor. Horizontal milling is further broken down into conventional milling, where the cutter rotates opposite the direction of feed, or “up” into the workpiece; and climb milling, where the cutter rotates in the direction of feed, or “down” into the workpiece. Milling operations include plane or surface milling, endmilling, facemilling, angle milling, form milling and profiling.
- milling cutter
milling cutter
Loosely, any milling tool. Horizontal cutters take the form of plain milling cutters, plain spiral-tooth cutters, helical cutters, side-milling cutters, staggered-tooth side-milling cutters, facemilling cutters, angular cutters, double-angle cutters, convex and concave form-milling cutters, straddle-sprocket cutters, spur-gear cutters, corner-rounding cutters and slitting saws. Vertical cutters use shank-mounted cutting tools, including endmills, T-slot cutters, Woodruff keyseat cutters and dovetail cutters; these may also be used on horizontal mills. See milling.
- milling machine ( mill)
milling machine ( mill)
Runs endmills and arbor-mounted milling cutters. Features include a head with a spindle that drives the cutters; a column, knee and table that provide motion in the three Cartesian axes; and a base that supports the components and houses the cutting-fluid pump and reservoir. The work is mounted on the table and fed into the rotating cutter or endmill to accomplish the milling steps; vertical milling machines also feed endmills into the work by means of a spindle-mounted quill. Models range from small manual machines to big bed-type and duplex mills. All take one of three basic forms: vertical, horizontal or convertible horizontal/vertical. Vertical machines may be knee-type (the table is mounted on a knee that can be elevated) or bed-type (the table is securely supported and only moves horizontally). In general, horizontal machines are bigger and more powerful, while vertical machines are lighter but more versatile and easier to set up and operate.
- shank
shank
Main body of a tool; the portion of a drill or similar end-held tool that fits into a collet, chuck or similar mounting device.