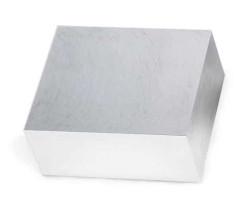
TCI Precision Metals announced, today, the addition of specialized round stock conversion to squared, high precision Machine-Ready Blanks.
Depending on job specifications or customer preference, round and square, precision Machine-Ready Blanks are now available, starting from round raw stock. “Some customers prefer to start with round stock material even when the finished machine-ready material needs to be square, but most of the time it comes down to alloy selection and availability,” said Ben Belzer, President and COO of TCI Precision Metals. "For example, 144 Cold Finished Carbon Steel and 465 Stainless Steel are both far more readily available in round stock. There tends to be more waste converting round materials to square machine-ready blanks, but if specifications or material availability dictate, TCI can now efficiently deliver on the request with our ‘round to square’ milling services,” added Belzer. TCI sawing, milling, and grinding equipment are all designed for high volume production and are configured to convert and prep virtually all materials to precision machine-ready specifications much more efficiently than most shops can do in-house.
Machine-Ready Blanks from TCI Precision Metals help shops increase throughput up to 25%. With a single purchase order customer receive custom precision blanks ready to load directly into their CNC machining centers. Precision blanks eliminate the need for in-house sawing, grinding, flattening, squaring operations and outside processing. Each blank arrives deburred, clean and to customer specifications – guaranteed as close as +/- .0005” dimensionally and as close as .002” flatness, squareness, and parallelism. Customers are able to use the time they previously spent in setup and prep for more productive use of CNC machining centers, adding to their bottom-line profitability.
Contact Details
Related Glossary Terms
- centers
centers
Cone-shaped pins that support a workpiece by one or two ends during machining. The centers fit into holes drilled in the workpiece ends. Centers that turn with the workpiece are called “live” centers; those that do not are called “dead” centers.
- computer numerical control ( CNC)
computer numerical control ( CNC)
Microprocessor-based controller dedicated to a machine tool that permits the creation or modification of parts. Programmed numerical control activates the machine’s servos and spindle drives and controls the various machining operations. See DNC, direct numerical control; NC, numerical control.
- gang cutting ( milling)
gang cutting ( milling)
Machining with several cutters mounted on a single arbor, generally for simultaneous cutting.
- grinding
grinding
Machining operation in which material is removed from the workpiece by a powered abrasive wheel, stone, belt, paste, sheet, compound, slurry, etc. Takes various forms: surface grinding (creates flat and/or squared surfaces); cylindrical grinding (for external cylindrical and tapered shapes, fillets, undercuts, etc.); centerless grinding; chamfering; thread and form grinding; tool and cutter grinding; offhand grinding; lapping and polishing (grinding with extremely fine grits to create ultrasmooth surfaces); honing; and disc grinding.
- milling
milling
Machining operation in which metal or other material is removed by applying power to a rotating cutter. In vertical milling, the cutting tool is mounted vertically on the spindle. In horizontal milling, the cutting tool is mounted horizontally, either directly on the spindle or on an arbor. Horizontal milling is further broken down into conventional milling, where the cutter rotates opposite the direction of feed, or “up” into the workpiece; and climb milling, where the cutter rotates in the direction of feed, or “down” into the workpiece. Milling operations include plane or surface milling, endmilling, facemilling, angle milling, form milling and profiling.
- sawing
sawing
Machining operation in which a powered machine, usually equipped with a blade having milled or ground teeth, is used to part material (cutoff) or give it a new shape (contour bandsawing, band machining). Four basic types of sawing operations are: hacksawing (power or manual operation in which the blade moves back and forth through the work, cutting on one of the strokes); cold or circular sawing (a rotating, circular, toothed blade parts the material much as a workshop table saw or radial-arm saw cuts wood); bandsawing (a flexible, toothed blade rides on wheels under tension and is guided through the work); and abrasive sawing (abrasive points attached to a fiber or metal backing part stock, could be considered a grinding operation).