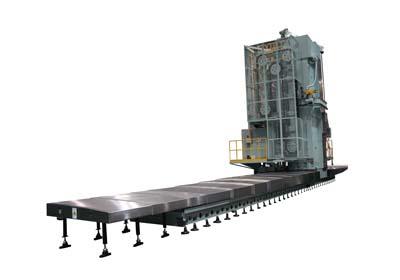
Mitsubishi Heavy Industries, Ltd. (MHI) has developed two floor-type horizontal boring mills, the MAF150C and MAF180C, with 150 millimeter (mm) and 180mm boring spindle diameters, respectively. The two machines in the new MAF-C Series have achieved a high level of cutting performance. This achievement has been enabled by adoption of the company's proprietary balance mechanism incorporating column tension bars, significant enhancement of the machines' structural rigidity, and increased spindle power output.
The two new machines employ a compact 420mm square-shaped ram (Z-axis) that extends and retracts in two stages while supporting the boring spindle, enabling horizontal milling up to 2,250mm deep within a narrow work space (1,250mm ram length in Z-axis + 1,000mm boring spindle length in W-axis). The powerful output of the machines' boring spindle motor is 55 kW (continuous), which is 1.8 times greater maximum power than previous models, enabling fast and stable milling.
The new machines are capable of stable and powerful machining even at a workpiece height of 5,000mm, using an optional vertical stroke saddle (Y-axis). To achieve high rigidity in the new machines, major structures are cast-finished and hydrostatic guide surfaces are employed for all sliding surfaces. In particular, ram rigidity is enhanced through the adoption of ductile cast iron, which has a high elastic modulus equivalent to steel, and a hydrostatic slide-guide mechanism to constrain the ram's four faces. For the column, a double-walled structure is employed. Together these features enable the new machines to achieve more than 1.5 times higher rigidity — both static and dynamic — compared with earlier machines, and to realize enhanced heavy-cutting capacity at a high position in the Y-axis, which effectively improves productivity.
High-accuracy cutting is supported by a new "perfect balance mechanism" in which the tension bars are incorporated vertically into the column and horizontally in the ram to improve straightness, augmented by a mechanism to adjust the suspension force of the saddle. With these mechanisms, the new machines are capable of precise adjustment or compensation of bending of the column, bowing of the ram or slanting of the saddle, ensuring high-precision cutting and high-quality surface machining in horizontal boring of any part of a workpiece.
To further enhance machining efficiency, the MAF150C and MAF180C also realize arapid traverse rate/spindle rotation speeds: 15,000mm/minute (mm/min) for the ram and boring spindle (Z- and W-axis), 20,000mm/min for the column and saddle (Y- and X-axis), and a maximum spindle speed of 2,500 revolutions per minute (rpm). Times required for automatic tool changing and attachment changing have also be reduced to less than half: 30 and 60 seconds, respectively. MHI expects demand for the MAF-C Series for use in shops that manufacture industrial machinery such as press machines, construction machinery, and advanced power generation equipment. Going forward, the company will further strengthen its aggressive marketing activities not only in Japan, Europe and the U.S., but also in the newly emerging economies, including China and India.
Contact Details
Related Glossary Terms
- boring
boring
Enlarging a hole that already has been drilled or cored. Generally, it is an operation of truing the previously drilled hole with a single-point, lathe-type tool. Boring is essentially internal turning, in that usually a single-point cutting tool forms the internal shape. Some tools are available with two cutting edges to balance cutting forces.
- gang cutting ( milling)
gang cutting ( milling)
Machining with several cutters mounted on a single arbor, generally for simultaneous cutting.
- milling
milling
Machining operation in which metal or other material is removed by applying power to a rotating cutter. In vertical milling, the cutting tool is mounted vertically on the spindle. In horizontal milling, the cutting tool is mounted horizontally, either directly on the spindle or on an arbor. Horizontal milling is further broken down into conventional milling, where the cutter rotates opposite the direction of feed, or “up” into the workpiece; and climb milling, where the cutter rotates in the direction of feed, or “down” into the workpiece. Milling operations include plane or surface milling, endmilling, facemilling, angle milling, form milling and profiling.