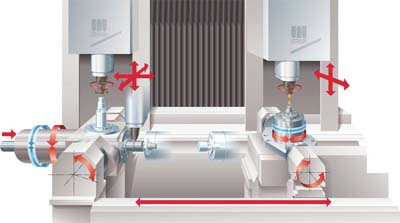
Stama America announces the introduction of its MC 726/MT-2C mill/turn, twin spindle machining centers for the automotive, fluid power, tooling, medical and other industries, where parts needs to be milled and turned in production operations. This new machining center is the latest iteration of the popular TANDEM concept mill/turn centers, introduced by Stama in 2007.
Two independent spindles are onboard, each on a traveling column assembly and each supporting an independent swivel table, one of which acts with a bar feeder mechanism. Workpieces are introduced to the turning spindle, then transitioned by a conveyorized gripper assembly to the milling indexer and fed to the milling spindle, before finally exiting the work area.
Complete six-sided machining is possible between the two cutting operations, all on one machine with approximately twice the speed of a conventional m/t center in 30 percent less footprint. Since the first part is being milled simultaneously to the next part being turned, the overall production operation is greatly enhanced, nearly doubling in many applications.
Contact Details
Related Glossary Terms
- centers
centers
Cone-shaped pins that support a workpiece by one or two ends during machining. The centers fit into holes drilled in the workpiece ends. Centers that turn with the workpiece are called “live” centers; those that do not are called “dead” centers.
- gang cutting ( milling)
gang cutting ( milling)
Machining with several cutters mounted on a single arbor, generally for simultaneous cutting.
- machining center
machining center
CNC machine tool capable of drilling, reaming, tapping, milling and boring. Normally comes with an automatic toolchanger. See automatic toolchanger.
- milling
milling
Machining operation in which metal or other material is removed by applying power to a rotating cutter. In vertical milling, the cutting tool is mounted vertically on the spindle. In horizontal milling, the cutting tool is mounted horizontally, either directly on the spindle or on an arbor. Horizontal milling is further broken down into conventional milling, where the cutter rotates opposite the direction of feed, or “up” into the workpiece; and climb milling, where the cutter rotates in the direction of feed, or “down” into the workpiece. Milling operations include plane or surface milling, endmilling, facemilling, angle milling, form milling and profiling.
- turning
turning
Workpiece is held in a chuck, mounted on a face plate or secured between centers and rotated while a cutting tool, normally a single-point tool, is fed into it along its periphery or across its end or face. Takes the form of straight turning (cutting along the periphery of the workpiece); taper turning (creating a taper); step turning (turning different-size diameters on the same work); chamfering (beveling an edge or shoulder); facing (cutting on an end); turning threads (usually external but can be internal); roughing (high-volume metal removal); and finishing (final light cuts). Performed on lathes, turning centers, chucking machines, automatic screw machines and similar machines.