Contact Details
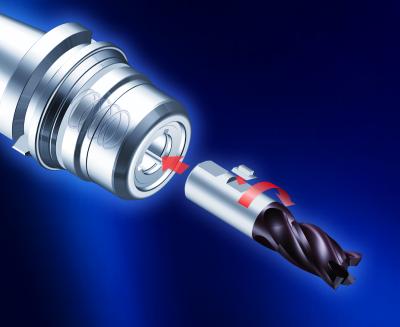
BIG KAISER introduces the Mega Perfect Grip from BIG Daishowa, a simple to handle, heavy-duty milling chuck for heat-resistant superalloys (HRSA) that eliminates endmill pullout under heavy torque loads. For manufacturers using milling chucks, pullout is a major issue, particularly when machining HRSAs, such as titanium or Inconel. In demanding applications, such as in the energy and aerospace markets, there is a need for guaranteed security against pullout, ensuring there is no costly damage to parts or delays in manufacturing processes.
The Mega Perfect Grip, with fully concentric clamping, combines the accuracy and cutting performance of heavy-duty milling chucks with the security against pullout of solid side-lock toolholders.
The concept is rather simple, and assembly is quick. To keep the system cost-effective, it is based around milling cutters with a standard Weldon flat (ASME B94.19-1997). No special grinding or threading of the milling cutter is required.
To assemble, insert the exclusive key grip into the Weldon flat of the endmill. Align the key grip with one of three key grip grooves inside the chuck body, and insert the cutting tool until it depresses a spring in the clamping bore. The spring functions to remove the gap between the key grip and the wall of the groove, and to provide a slight axial preload on the tool until final tightening is performed. Rotate the endmill approximately 20° until the grip stops securely against a stopping pin. This engagement prevents any slip under high torque. Finalize assembly by tightening the clamping nut until it contacts the positive stop of the chuck body.
The three key grip grooves in the chuck body also serve to provide channels for high-volume coolant to reach the cutter, which is required in milling HRSAs to dissipate heat and to remove chips efficiently.
“Pullout can be a big headache when working with HRSAs—costing time and money, and hitting manufacturers’ profitability,” said Jack Burley, vice president sales and engineering. “This innovative chuck solves the problem completely, combining innovation with ease-of-use and industry standards.”
The Mega Perfect Grip is available in BIG-PLUS BCV50 and HSK-A100 for diameters from 0.750” to 1.250”, and HSK-A125 for 1.000” and 1.250” diameters.
Related Glossary Terms
- chuck
chuck
Workholding device that affixes to a mill, lathe or drill-press spindle. It holds a tool or workpiece by one end, allowing it to be rotated. May also be fitted to the machine table to hold a workpiece. Two or more adjustable jaws actually hold the tool or part. May be actuated manually, pneumatically, hydraulically or electrically. See collet.
- coolant
coolant
Fluid that reduces temperature buildup at the tool/workpiece interface during machining. Normally takes the form of a liquid such as soluble or chemical mixtures (semisynthetic, synthetic) but can be pressurized air or other gas. Because of water’s ability to absorb great quantities of heat, it is widely used as a coolant and vehicle for various cutting compounds, with the water-to-compound ratio varying with the machining task. See cutting fluid; semisynthetic cutting fluid; soluble-oil cutting fluid; synthetic cutting fluid.
- endmill
endmill
Milling cutter held by its shank that cuts on its periphery and, if so configured, on its free end. Takes a variety of shapes (single- and double-end, roughing, ballnose and cup-end) and sizes (stub, medium, long and extra-long). Also comes with differing numbers of flutes.
- flat ( screw flat)
flat ( screw flat)
Flat surface machined into the shank of a cutting tool for enhanced holding of the tool.
- gang cutting ( milling)
gang cutting ( milling)
Machining with several cutters mounted on a single arbor, generally for simultaneous cutting.
- grinding
grinding
Machining operation in which material is removed from the workpiece by a powered abrasive wheel, stone, belt, paste, sheet, compound, slurry, etc. Takes various forms: surface grinding (creates flat and/or squared surfaces); cylindrical grinding (for external cylindrical and tapered shapes, fillets, undercuts, etc.); centerless grinding; chamfering; thread and form grinding; tool and cutter grinding; offhand grinding; lapping and polishing (grinding with extremely fine grits to create ultrasmooth surfaces); honing; and disc grinding.
- milling
milling
Machining operation in which metal or other material is removed by applying power to a rotating cutter. In vertical milling, the cutting tool is mounted vertically on the spindle. In horizontal milling, the cutting tool is mounted horizontally, either directly on the spindle or on an arbor. Horizontal milling is further broken down into conventional milling, where the cutter rotates opposite the direction of feed, or “up” into the workpiece; and climb milling, where the cutter rotates in the direction of feed, or “down” into the workpiece. Milling operations include plane or surface milling, endmilling, facemilling, angle milling, form milling and profiling.
- milling cutter
milling cutter
Loosely, any milling tool. Horizontal cutters take the form of plain milling cutters, plain spiral-tooth cutters, helical cutters, side-milling cutters, staggered-tooth side-milling cutters, facemilling cutters, angular cutters, double-angle cutters, convex and concave form-milling cutters, straddle-sprocket cutters, spur-gear cutters, corner-rounding cutters and slitting saws. Vertical cutters use shank-mounted cutting tools, including endmills, T-slot cutters, Woodruff keyseat cutters and dovetail cutters; these may also be used on horizontal mills. See milling.
- superalloys
superalloys
Tough, difficult-to-machine alloys; includes Hastelloy, Inconel and Monel. Many are nickel-base metals.
- threading
threading
Process of both external (e.g., thread milling) and internal (e.g., tapping, thread milling) cutting, turning and rolling of threads into particular material. Standardized specifications are available to determine the desired results of the threading process. Numerous thread-series designations are written for specific applications. Threading often is performed on a lathe. Specifications such as thread height are critical in determining the strength of the threads. The material used is taken into consideration in determining the expected results of any particular application for that threaded piece. In external threading, a calculated depth is required as well as a particular angle to the cut. To perform internal threading, the exact diameter to bore the hole is critical before threading. The threads are distinguished from one another by the amount of tolerance and/or allowance that is specified. See turning.