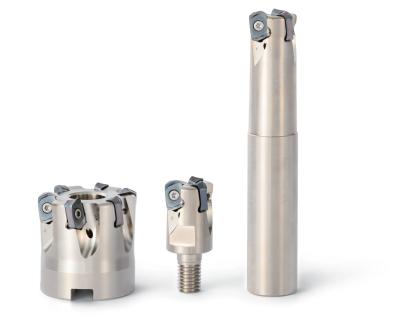
Kyocera Precision Tools introduces a new expansion to their most versatile indexable high-feed milling line. The MFH-MAX provides excellent chip removal performance in various applications, including automotive parts, difficult-to-cut materials, and mold machining. With the ability to take on deeper depths of cut (max. 0.098” / 2.5mm), the MFH-MAX wastes little time getting to work and reduces the number of passes needed to machine the workpiece. The MFH-MAX also supports various milling operations including shouldering, slotting, helical milling, and ramping applications.
After the previous success of the MFH-RAPTOR, MFH-Mini, and MFH-Micro, Kyocera’s introduction of the MFH-MAX provides a new alternative to conventional 90° end mills when roughing to medium-finishing. The MFH-MAX also provides more capabilities than conventional high-feed mills by reducing the number of tool paths and machining time when cutting workpieces with large variations in machining margins.
The MFH-MAX utilizes economical, 4-edge, double-sided inserts with a unique convex cutting edge design. These inserts are available in PR15-series PVD insert grades with Kyocera’s proprietary MEGACOAT NANO coating technology and a wear resistant CVD grade to cover a wide range of materials from steel, stainless, cast iron, and difficult-to-cut-materials.
Benefits:
- Large max depth of cut dramatically improves machining efficiency
- High chip removal ratio
- Long tool life and stable machining with anti-vibration design
- Rigid, chatter-resistant body design
- Convex insert cutting edge reduces impact when entering the workpiece
Features:
- Cutting Diameters: 1” – 3” / 22mm – 80mm
- Double-sided Insert: 4 cutting edges
- Max D.O.C. = 0.098” (2.5mm)
- GM Chipbreaker: General Purpose
- Toolholder Lineup: Face mills, end mills, modular end mills
Applications:
- Facing and shouldering
- Slot milling
- Ramping
- Helical milling
- Plunge milling
Contact Details
Related Glossary Terms
- chemical vapor deposition ( CVD)
chemical vapor deposition ( CVD)
High-temperature (1,000° C or higher), atmosphere-controlled process in which a chemical reaction is induced for the purpose of depositing a coating 2µm to 12µm thick on a tool’s surface. See coated tools; PVD, physical vapor deposition.
- depth of cut
depth of cut
Distance between the bottom of the cut and the uncut surface of the workpiece, measured in a direction at right angles to the machined surface of the workpiece.
- gang cutting ( milling)
gang cutting ( milling)
Machining with several cutters mounted on a single arbor, generally for simultaneous cutting.
- milling
milling
Machining operation in which metal or other material is removed by applying power to a rotating cutter. In vertical milling, the cutting tool is mounted vertically on the spindle. In horizontal milling, the cutting tool is mounted horizontally, either directly on the spindle or on an arbor. Horizontal milling is further broken down into conventional milling, where the cutter rotates opposite the direction of feed, or “up” into the workpiece; and climb milling, where the cutter rotates in the direction of feed, or “down” into the workpiece. Milling operations include plane or surface milling, endmilling, facemilling, angle milling, form milling and profiling.
- physical vapor deposition ( PVD)
physical vapor deposition ( PVD)
Tool-coating process performed at low temperature (500° C), compared to chemical vapor deposition (1,000° C). Employs electric field to generate necessary heat for depositing coating on a tool’s surface. See CVD, chemical vapor deposition.
- plunge milling
plunge milling
Highly productive method of metal removal in which an axial machining operation is performed in a single tool sequence. The tool makes a series of overlapping, drill-like plunges to remove part of a cylindrical plug of material one after another. Because of the increased rigidity of a Z-axis move, the tool can cover a large cross-section of material.
- slotting
slotting
Machining, normally milling, that creates slots, grooves and similar recesses in workpieces, including T-slots and dovetails.
- toolholder
toolholder
Secures a cutting tool during a machining operation. Basic types include block, cartridge, chuck, collet, fixed, modular, quick-change and rotating.