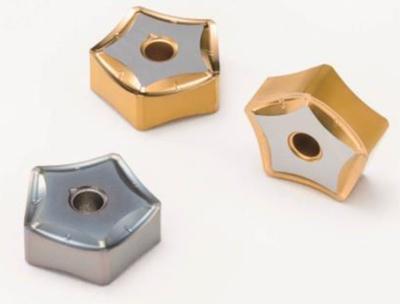
Kyocera Precision Tools Inc. unveiled its new MFK indexable milling cutter for cast iron, a milling system that will allow machinists to reduce costs and improve their milling operations through the use of double-sided, 10-edge negative inserts.
Automotive engines, construction equipment and machine tools require metal components in complex shapes that are commonly created by casting molten metal in specialized molds. Castings taken from these molds require difficult finish machining. Many workpieces are challenging to hold securely during the machining process because their complex shapes limit clamping rigidity. Insufficient clamping rigidity causes vibration and chattering due to the cutting forces of the machining process.
In addition, cast iron workpieces are susceptible to a phenomenon known as "breakout," in which the edge of the workpiece chips away rather than being cut cleanly. Cutting tool inserts that can improve machining quality by reducing the cutting forces and preventing chipping are therefore in great demand.
Kyocera's new MFK cast iron milling cutter utilizes a newly developed double-sided insert with 10 cutting edges. Although negative inserts offer cost benefits because cutting edges can be formed on both sides of the insert, they tend to increase cutting resistance, causing a decrease in sharpness or an increase in chattering. To address this challenge, Kyocera has developed uniquely shaped inserts using its proprietary molding technology, which reduces both cutting resistance and chattering.
The inserts also improve machining quality through a double-edge structure in which two cutting edges are provided for the insert corners. Kyocera's MFK milling cutters offer improved quality and better cost performance in machining cast iron, with higher productivity in conditions ranging from roughing to finishing.
New Product Features:
1. Double-sided, 10-corner negative inserts provide quality and cost benefits
1-A. Proprietary edge shape reduces cutting resistance The newly developed negative inserts utilize two lead angles per corner. Using molding technology developed by Kyocera, a large axial rake angle is provided on cutting edges, reducing cutting resistance and facilitating smoother machining. Increasing the lead angle also reduces cutting resistance in an axial direction of the workpiece, vibration and chattering.
1-B. Double-edged structure helps prevent inserts from fracturing and breakout A proprietary double-edged structure using two main cutting edges is utilized on each corner to cushion initial shock at the moment of workpiece contact, the onset of cutting. This helps prevent inserts from fracturing and breakout, helping to stabilize the machining process and improve finish quality.
2. Newly developed CVD material for cast-iron milling offers long tool life and stable machining Kyocera has added the new CA420M CVD1 material for cast iron milling to its insert grade lineup. CA420M is comprised of a newly developed, high-toughness base substrate with a new CVD coating developed using proprietary crystal-control and film-formation technologies. Improved abrasion resistance, essential in machining cast iron, will allow CA420M to deliver better cost performance, longer tool life and a more stable machining process.
3. Accommodates a wide range of cast-iron machining conditions, from roughing to finishing Kyocera's extensive lineup of milling cutters, insert shapes, and grades ensures an ideal combination to cover a wide range of conditions, from cast iron roughing to finishing.
Contact Details
Related Glossary Terms
- axial rake
axial rake
On angular tool flutes, the angle between the tooth face and the axial plane through the tool point.
- chemical vapor deposition ( CVD)
chemical vapor deposition ( CVD)
High-temperature (1,000° C or higher), atmosphere-controlled process in which a chemical reaction is induced for the purpose of depositing a coating 2µm to 12µm thick on a tool’s surface. See coated tools; PVD, physical vapor deposition.
- gang cutting ( milling)
gang cutting ( milling)
Machining with several cutters mounted on a single arbor, generally for simultaneous cutting.
- lead angle
lead angle
Angle between the side-cutting edge and the projected side of the tool shank or holder, which leads the cutting tool into the workpiece.
- milling
milling
Machining operation in which metal or other material is removed by applying power to a rotating cutter. In vertical milling, the cutting tool is mounted vertically on the spindle. In horizontal milling, the cutting tool is mounted horizontally, either directly on the spindle or on an arbor. Horizontal milling is further broken down into conventional milling, where the cutter rotates opposite the direction of feed, or “up” into the workpiece; and climb milling, where the cutter rotates in the direction of feed, or “down” into the workpiece. Milling operations include plane or surface milling, endmilling, facemilling, angle milling, form milling and profiling.
- milling cutter
milling cutter
Loosely, any milling tool. Horizontal cutters take the form of plain milling cutters, plain spiral-tooth cutters, helical cutters, side-milling cutters, staggered-tooth side-milling cutters, facemilling cutters, angular cutters, double-angle cutters, convex and concave form-milling cutters, straddle-sprocket cutters, spur-gear cutters, corner-rounding cutters and slitting saws. Vertical cutters use shank-mounted cutting tools, including endmills, T-slot cutters, Woodruff keyseat cutters and dovetail cutters; these may also be used on horizontal mills. See milling.
- rake
rake
Angle of inclination between the face of the cutting tool and the workpiece. If the face of the tool lies in a plane through the axis of the workpiece, the tool is said to have a neutral, or zero, rake. If the inclination of the tool face makes the cutting edge more acute than when the rake angle is zero, the rake is positive. If the inclination of the tool face makes the cutting edge less acute or more blunt than when the rake angle is zero, the rake is negative.