Contact Details
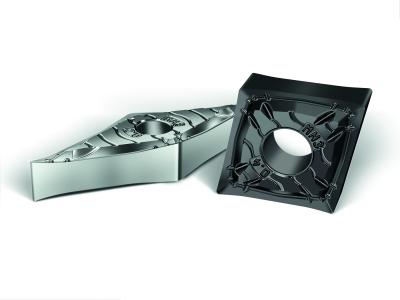
Walter has introduced the MN3 insert geometry specially designed for cost-effective machining of non-ferrous (ISO N) materials. The geometry is ideal for the medium machining of non-ferrous metals (for example aluminum, copper, or brass alloys) and secondarily for the fine finishing of small components made from steel, stainless-steel and high-temperature alloys.
Positive with four cutting edges, it can be used on both sides, thus combining long tool life and high metal removal rates with greater cost-efficiency. The polished rake face improves chip removal, and the extremely sharp cutting edge creates a softer cutting action, important factors in the insert's positive reception by the market. The softer cutting action enables successful machining of unstable components and components with long overhangs.
This double-sided insert is a powerful expansion of the existing Walter portfolio for non-ferrous (ISO N) machining with positive geometries, the FN2 and MN2. Walter is launching the new indexable insert in two grades; WN10 a cost-effective, uncoated, and polished grade; and WNN10 with a wear resistant HIPIMS PVD coating, with an extremely smooth surface, and an optimized layer bonding.
MN3 is the first Walter geometry to have double the number of cutting edges while also being highly positive. The rake angle on the radius is 29°. Thanks to the highly positive cutting edge, users benefit from improved chip breaking – even when working with "lead-free materials" like CuZn21Si3P. The surface roughness was also optimized, which allows for an increased tool life even when working with materials that tend to stick with built-up edges. The negative basic shape with double the number of cutting edges increases productivity and cost-efficiency.
Related Glossary Terms
- alloys
alloys
Substances having metallic properties and being composed of two or more chemical elements of which at least one is a metal.
- indexable insert
indexable insert
Replaceable tool that clamps into a tool body, drill, mill or other cutter body designed to accommodate inserts. Most inserts are made of cemented carbide. Often they are coated with a hard material. Other insert materials are ceramic, cermet, polycrystalline cubic boron nitride and polycrystalline diamond. The insert is used until dull, then indexed, or turned, to expose a fresh cutting edge. When the entire insert is dull, it is usually discarded. Some inserts can be resharpened.
- physical vapor deposition ( PVD)
physical vapor deposition ( PVD)
Tool-coating process performed at low temperature (500° C), compared to chemical vapor deposition (1,000° C). Employs electric field to generate necessary heat for depositing coating on a tool’s surface. See CVD, chemical vapor deposition.
- rake
rake
Angle of inclination between the face of the cutting tool and the workpiece. If the face of the tool lies in a plane through the axis of the workpiece, the tool is said to have a neutral, or zero, rake. If the inclination of the tool face makes the cutting edge more acute than when the rake angle is zero, the rake is positive. If the inclination of the tool face makes the cutting edge less acute or more blunt than when the rake angle is zero, the rake is negative.