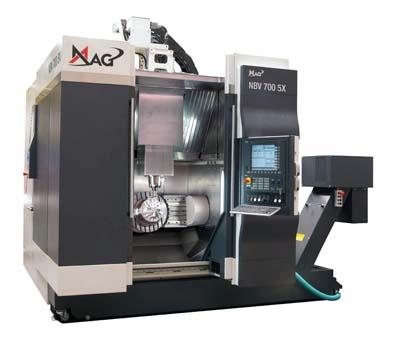
Shorter cycle times are one way of reducing costs; another way to be more productive actually involves longer cycle times: complete machining in a single setup. Clamping a part only once means reduced costs for fixtures, less time spent on setups for different machines, while improving quality by avoiding reclamping errors. This is exactly where the new vertical milling machine from MAG comes"
Configured as a 5-axis machine with an NC tilting/rotary table (C- on A-axis), the NBV 700 5X is capable of machining complex workpieces in a single setup. Whether it's angled cuts or complex free forms, even 5-axis simultaneous machining is possible with an A-axis tilting range of +90 degrees to -120 degrees. The NBV 700 MT (mill-turn) even turns the milling machine into a turning machine.
Equipped with a high speed rotary table, (C-axis up to 1,000/rpm) and the tilting/rotary axes for 5-axis machining; both precision components from CORCOM allow for drilling, milling, tapping and turning capabilities on just one machine. The machine was designed for tough jobs, with a heavily ripped, thick walled, cast iron construction machine bed, and an FEA optimized static and dynamic design. The highly dynamic tilting rotary table, driven by torque motors on both sides of the A-axis, ensures symmetrical delivery of power and torque to tilt the robust rotary table unit.
Endowed with these powerful components, even heavy machining jobs are no problem, delivering superior results for the die and mold, aerospace and other industries. The NBV 700 also sets standards regarding energy efficiency and the environment. The standard version of the machine runs without hydraulics; tools are clamped by disc springs and unclamped pneumatically. The same applies to the A-axis clamping on the tilting/rotary table.
A "green machining" feature of MAG machining centers is a new power saving mode that automatically levels speed and acceleration to provide an ideal balance of performance and energy consumption. Real-time energy consumption plus energy saving settings are displayed on a monitor during machine operation. The NBV delivers outstanding machine performance, with the ideal balance of processing time and energy consumption, while enhancing the service life of mechanical components and the machine's long-term accuracy.
Contact Details
Related Glossary Terms
- centers
centers
Cone-shaped pins that support a workpiece by one or two ends during machining. The centers fit into holes drilled in the workpiece ends. Centers that turn with the workpiece are called “live” centers; those that do not are called “dead” centers.
- gang cutting ( milling)
gang cutting ( milling)
Machining with several cutters mounted on a single arbor, generally for simultaneous cutting.
- milling
milling
Machining operation in which metal or other material is removed by applying power to a rotating cutter. In vertical milling, the cutting tool is mounted vertically on the spindle. In horizontal milling, the cutting tool is mounted horizontally, either directly on the spindle or on an arbor. Horizontal milling is further broken down into conventional milling, where the cutter rotates opposite the direction of feed, or “up” into the workpiece; and climb milling, where the cutter rotates in the direction of feed, or “down” into the workpiece. Milling operations include plane or surface milling, endmilling, facemilling, angle milling, form milling and profiling.
- milling machine ( mill)
milling machine ( mill)
Runs endmills and arbor-mounted milling cutters. Features include a head with a spindle that drives the cutters; a column, knee and table that provide motion in the three Cartesian axes; and a base that supports the components and houses the cutting-fluid pump and reservoir. The work is mounted on the table and fed into the rotating cutter or endmill to accomplish the milling steps; vertical milling machines also feed endmills into the work by means of a spindle-mounted quill. Models range from small manual machines to big bed-type and duplex mills. All take one of three basic forms: vertical, horizontal or convertible horizontal/vertical. Vertical machines may be knee-type (the table is mounted on a knee that can be elevated) or bed-type (the table is securely supported and only moves horizontally). In general, horizontal machines are bigger and more powerful, while vertical machines are lighter but more versatile and easier to set up and operate.
- numerical control ( NC)
numerical control ( NC)
Any controlled equipment that allows an operator to program its movement by entering a series of coded numbers and symbols. See CNC, computer numerical control; DNC, direct numerical control.
- tapping
tapping
Machining operation in which a tap, with teeth on its periphery, cuts internal threads in a predrilled hole having a smaller diameter than the tap diameter. Threads are formed by a combined rotary and axial-relative motion between tap and workpiece. See tap.
- turning
turning
Workpiece is held in a chuck, mounted on a face plate or secured between centers and rotated while a cutting tool, normally a single-point tool, is fed into it along its periphery or across its end or face. Takes the form of straight turning (cutting along the periphery of the workpiece); taper turning (creating a taper); step turning (turning different-size diameters on the same work); chamfering (beveling an edge or shoulder); facing (cutting on an end); turning threads (usually external but can be internal); roughing (high-volume metal removal); and finishing (final light cuts). Performed on lathes, turning centers, chucking machines, automatic screw machines and similar machines.
- turning machine
turning machine
Any machine that rotates a workpiece while feeding a cutting tool into it. See lathe.