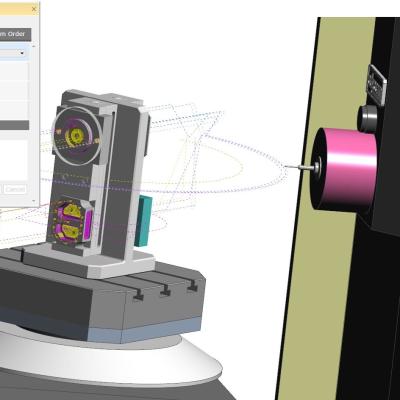
The new release of Edgecam, from Vero Software, contains 54 items of new or enhanced functionality that improve productivity for manufacturers by using a range of cutting technologies and machining strategies. They include significant changes to the Pre-Drill Approach Roughing cycle, creating features from wireframe entities, 3D milling cycles in mill-turn Rotary mode, 28 new technology databases in the Wire EDM module and Tombstone.
Edgecam Brand Manager John Buehler says that every user will benefit from at least one of the enhancements, the most significant of which is a complete transformation to the Tombstone Manger, thanks to 13 enhancements.
The new Add Tombstone function ensures users never overwrite their master tombstone assembly file (referred to as Seed file). The originating file is always protected, guaranteeing that vital information is never overwritten.
The number of components that can be inserted onto the Tombstone is now limitless, reflecting best industry practice. Once inserted, the toolpaths are not only automatically merged, but the enhanced Closest Next ordering further economizes the CAM toolpaths.
“Arguably the most significant individual enhancement is the ability to retrospectively edit the CAM toolpaths,” he says. Using the new ‘Edit’ and ‘Reload’ functions, Edgecam will independently open the inserted file, allowing the user to perform unlimited edits to the CAM instructions. Once finished, the seed file is automatically updated with the new editions.
The way the Pre-Drill approach strategy is handled has been significantly improved within the Roughing cycle. “Rather than manually create drill-hole positions, which is sometimes time consuming, Edgecam 2018 R2 automatically creates the hole position and keeps the drilling toolpath associative to the Roughing cycle," Buehler says. “Simply by activating the command, users can deploy the multilevel and depth functions within a hole cycle to automatically locate the best entry position for the drill cycle.”
The Rough Turn cycle includes several new lead parameters allowing the user to roll in and out of each cut with a tangential arc. A bidirectional toolpath can be created, allowing the cycle to be used in conjunction with Sandvik Coromant’s CoroTurn Prime turning inserts. Significant time savings and reduced tool wear can be achieved when adopting these methods.
Also, the cycle’s collision detection capability has been extended by automatically removing any potential crashes between the tool and the tailstock.
Edgecam Inspection module’s evolution continues with 14 enhancements, including full postprocessor support with the Code Wizard.
Major items include the introduction of NC Gateway, which communicates with the machine tool, plus Best Fit calculation, which allows alignment of the workpiece. In addition to the new Inspect Rectangle feature, both the Options and Inspect Toolpath dialogs include new features. Users may now influence both the Work Datum and the Tool Offset and view the status from within the NC output and the Inspection Report.
Edgecam Designer’s 2D Drawing Module creates views and sections of the 3D model in the Designer file. Features include dynamic view creation, shaded and wireframe views, fixed and variable sections, detailed views, and outbreaks. The 2D drawing and its associative dimensions can be updated when changes are made to the 3D model.
The many sketching and modelling enhancements throughout Edgecam Designer include the Active Sketch Plane, which allows wireframe to be created directly onto solid and surface models, without the need for workplanes.
Additionally, it is now possible to create the Projected Area of solid and surface models, and new analysis functionality calculates aspects such as area, volume, perimeter, and center of gravity.
Through improvements in the toolpath algorithm, Edgecam 2018 R2 provides a significant performance improvement with the Pick Solid Faces function. Time savings of over 50 percent can be achieved thanks to the manner in which the cycle gathers data for toolpath calculation.
“Users will also gain further benefits when using the Multi-Pass function, as the strategy is now supported with helical capability,” Buehler says.
Buehler says it wasn’t previously possible to create a feature from wireframe entities. “In certain situations, such as creating automation routines, that would have been desirable, so Edgecam 2018 R2 now unlocks the ability to deploy workflow strategies, where ordinarily a feature couldn’t be created, by converting line and arc data into a solid Feature. Once machined, the new feature can be edited and the toolpath will remain associative.”
Found in both the milling and turning environments, the Thread Mill cycle has been enhanced to allow closer toolpath control and greater flexibility. Five new parameters allow users to deploy "peck" and "multipass" toolpaths. This will especially help when machining hard materials or when a better surface finish is required.
Further new options found in the Lead tab deliver additional control with toolpath ordering.
3D milling cycles in the mill-turn environment have now become available while working in Rotary mode. Previously, these cycles were restricted to Planar mode. “This enhancement offers greater flexibility in not only unlocking the seven milling cycles which were normally unavailable, but allows users to overcome machine-tool limit issues,” Buehler says.
When being forced to use the same tool number, but for different tools, programmers in the turning environment can now use the Replace Active Tool function so that the simulator will only display a single tool in the turret during playback. Users can now also increase playback performance by using the new "simplify solid mill cutters" command. When using complicated solid-model cutters, the function will simplify the profile by converting it into a silhouette.
Buehler says, “When viewed individually, small enhancements don’t appear to have a significant impact. However, when added together, their sum total has an important effect on the day-to-day operation of the software. And all the updates here were driven by customer requests/feedback.”
A good example are the three enhancements found in the Preferences section of Edgecam 2018 R2. Users now have the choice to activate a toolkit by simply using the new Automatically Create Toolkit check-box. They can also use the new Job/Toolkit Update preferences settings when generating NC output. Additionally, the new "technology warning" check-box helps avoid misrepresenting tool feed and speed settings.
Manufacturers working with turning tools can now pre-state the CSS condition from the tool store. This avoids individually setting the status every time the tool is chosen.
In the case of Face Grooving tools, programmers can now add further detail to the description of the tool by adding Maximum/Minimum Diameter, which is particularly useful for Strategy Manager authors. An additional turning enhancement, Edgecam 2018 R2 allows any tool type to be deployed when executing the Thread Turning cycle.
Edgecam 2018 R2 introduces 28 new technology databases to the Wire EDM module, including the popular Agie, FANUC, Makino and Mitsubishi controllers.
During the machine simulation stage, the "start hole" (entry position for the wire) is created automatically, alleviating the need to manually create the hole in the stock.
Related Glossary Terms
- computer-aided manufacturing ( CAM)
computer-aided manufacturing ( CAM)
Use of computers to control machining and manufacturing processes.
- electrical-discharge machining ( EDM)
electrical-discharge machining ( EDM)
Process that vaporizes conductive materials by controlled application of pulsed electrical current that flows between a workpiece and electrode (tool) in a dielectric fluid. Permits machining shapes to tight accuracies without the internal stresses conventional machining often generates. Useful in diemaking.
- feed
feed
Rate of change of position of the tool as a whole, relative to the workpiece while cutting.
- gang cutting ( milling)
gang cutting ( milling)
Machining with several cutters mounted on a single arbor, generally for simultaneous cutting.
- grooving
grooving
Machining grooves and shallow channels. Example: grooving ball-bearing raceways. Typically performed by tools that are capable of light cuts at high feed rates. Imparts high-quality finish.
- milling
milling
Machining operation in which metal or other material is removed by applying power to a rotating cutter. In vertical milling, the cutting tool is mounted vertically on the spindle. In horizontal milling, the cutting tool is mounted horizontally, either directly on the spindle or on an arbor. Horizontal milling is further broken down into conventional milling, where the cutter rotates opposite the direction of feed, or “up” into the workpiece; and climb milling, where the cutter rotates in the direction of feed, or “down” into the workpiece. Milling operations include plane or surface milling, endmilling, facemilling, angle milling, form milling and profiling.
- milling machine ( mill)
milling machine ( mill)
Runs endmills and arbor-mounted milling cutters. Features include a head with a spindle that drives the cutters; a column, knee and table that provide motion in the three Cartesian axes; and a base that supports the components and houses the cutting-fluid pump and reservoir. The work is mounted on the table and fed into the rotating cutter or endmill to accomplish the milling steps; vertical milling machines also feed endmills into the work by means of a spindle-mounted quill. Models range from small manual machines to big bed-type and duplex mills. All take one of three basic forms: vertical, horizontal or convertible horizontal/vertical. Vertical machines may be knee-type (the table is mounted on a knee that can be elevated) or bed-type (the table is securely supported and only moves horizontally). In general, horizontal machines are bigger and more powerful, while vertical machines are lighter but more versatile and easier to set up and operate.
- numerical control ( NC)
numerical control ( NC)
Any controlled equipment that allows an operator to program its movement by entering a series of coded numbers and symbols. See CNC, computer numerical control; DNC, direct numerical control.
- toolpath( cutter path)
toolpath( cutter path)
2-D or 3-D path generated by program code or a CAM system and followed by tool when machining a part.
- turning
turning
Workpiece is held in a chuck, mounted on a face plate or secured between centers and rotated while a cutting tool, normally a single-point tool, is fed into it along its periphery or across its end or face. Takes the form of straight turning (cutting along the periphery of the workpiece); taper turning (creating a taper); step turning (turning different-size diameters on the same work); chamfering (beveling an edge or shoulder); facing (cutting on an end); turning threads (usually external but can be internal); roughing (high-volume metal removal); and finishing (final light cuts). Performed on lathes, turning centers, chucking machines, automatic screw machines and similar machines.
- wire EDM
wire EDM
Process similar to ram electrical-discharge machining except a small-diameter copper or brass wire is used as a traveling electrode. Usually used in conjunction with a CNC and only works when a part is to be cut completely through. A common analogy is wire electrical-discharge machining is like an ultraprecise, electrical, contour-sawing operation.