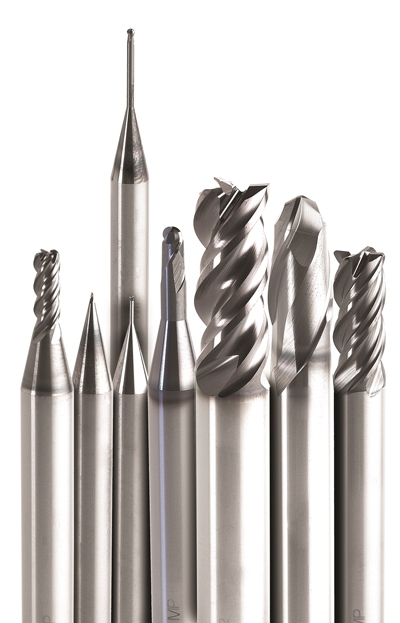
Moldmaking processes require innovative cutting tool technologies capable of delivering the highest degree of precision, flexibility and efficiency. With its latest line of endmills, NS Tool equips manufacturers with capabilities for boosting productivity and maximizing output in high-performance hard milling, according to distributor Single Source Technologies.
"NS Tool specializes in very high-precision, small-diameter tools," said Darrell Johnson, product manager milling consumables at SST. "Their intense focus on the tiniest detail in creating their product translates into products that perform consistently. The fine details of quality are so precise that one must magnify the cutting edge thousands of times to see how flawless each cutting surface is."
Endmills from NS Tool feature a variety of coatings and flute designs, offering a solution for any modern mold-making challenge. Many of them have NS Tool's patented MUGEN premium coating, which features a hardness of 3,600HV for longer and more stable tool life in the machining of hardened steel (48 to 65 HRC) applications. MUGEN premium coating is widely known for its excellent heat resistance, making it ideal for dry, high-speed-cutting operations. Although originally designed to cut hardened steels, MUGEN premium coating has proven to provide excellent wear resistance to machine steels in the lower hardness range. Tools with this coating are designed to reportedly deliver superior levels of accuracy and finish.
Combining NS Tool's attention to quality with advanced coating technology equips the MUGEN premium coating with outstanding characteristics. These high-precision, small-diameter tools can consistently create the tiniest details for excellent finishing capability.
The MSBH230 ball endmill features a 2-flute, 30-degree helix design with MUGEN premium coating. This tool is capable of producing superior surface finishes in hardened materials ranging from 48 to 65 HRc. Its unique cutting-edge design reduces chatter and increases strength to eliminate possibility of chipping.
The MRBH230 long-neck ball endmill also has MUGEN premium coating, and it is ideal for machining rib features in hardened materials ranging from 48 to 65 HRC. Similar to the MSBH230, this model features a unique 2-flute, 30-degree helix design that reduces chatter and increase cutting-edge strength to eliminate possibility of chipping.
The MSB345H is a 3-flute ballnose endmill. Its spiral shape, coupled with unequal flute spacing, reduces chatter and yields stable cutting at increased feedrates. The additional flute enables increased productivity without sacrificing finish. MUGEN premium coating supplies the wear resistance and toughness to machine steels and other materials with hardness up to 65 HRC.
The MRBTNH345 is a 3-flute, long-neck ballnose endmill. The additional flute enables increased productivity without sacrificing finish. With unequal flute spacing and spiral design, chatter is greatly reduced while stable cutting at increased feed rates is achieved. MUGEN premium coating provides the wear resistance and toughness to machine steels and other materials with hardness up to 65HRC.
The variable helix angles and pitched flute design of the MSXH440R micrograin solid-carbide corner radius endmill has the ability to suppress chatter for stable milling conditions in a variety of applications. The 40- and 42-degree helix angles of this MUGEN-coated tool deliver excellent performance in alloy steels, stainless steels, titanium and other heat-resistant materials.
The MSZ345 is a MUGEN-coated square endmill with Z-axis plunging capability. Its ability to center cut, drill and side mill in the same tool makes the MSZ345 an ideal solution for opening up pockets. The tool has a three-flute, 45-degree helix design with chipbreaker in the end that provides efficient cutting in steels, stainless steels and prehardened steels.
Contact Details
Related Glossary Terms
- alloy steels
alloy steels
Steel containing specified quantities of alloying elements (other than carbon and the commonly accepted amounts of manganese, sulfur and phosphorus) added to cause changes in the metal’s mechanical and/or physical properties. Principal alloying elements are nickel, chromium, molybdenum and silicon. Some grades of alloy steels contain one or more of these elements: vanadium, boron, lead and copper.
- chatter
chatter
Condition of vibration involving the machine, workpiece and cutting tool. Once this condition arises, it is often self-sustaining until the problem is corrected. Chatter can be identified when lines or grooves appear at regular intervals in the workpiece. These lines or grooves are caused by the teeth of the cutter as they vibrate in and out of the workpiece and their spacing depends on the frequency of vibration.
- chipbreaker
chipbreaker
Groove or other tool geometry that breaks chips into small fragments as they come off the workpiece. Designed to prevent chips from becoming so long that they are difficult to control, catch in turning parts and cause safety problems.
- endmill
endmill
Milling cutter held by its shank that cuts on its periphery and, if so configured, on its free end. Takes a variety of shapes (single- and double-end, roughing, ballnose and cup-end) and sizes (stub, medium, long and extra-long). Also comes with differing numbers of flutes.
- feed
feed
Rate of change of position of the tool as a whole, relative to the workpiece while cutting.
- gang cutting ( milling)
gang cutting ( milling)
Machining with several cutters mounted on a single arbor, generally for simultaneous cutting.
- hardness
hardness
Hardness is a measure of the resistance of a material to surface indentation or abrasion. There is no absolute scale for hardness. In order to express hardness quantitatively, each type of test has its own scale, which defines hardness. Indentation hardness obtained through static methods is measured by Brinell, Rockwell, Vickers and Knoop tests. Hardness without indentation is measured by a dynamic method, known as the Scleroscope test.
- milling
milling
Machining operation in which metal or other material is removed by applying power to a rotating cutter. In vertical milling, the cutting tool is mounted vertically on the spindle. In horizontal milling, the cutting tool is mounted horizontally, either directly on the spindle or on an arbor. Horizontal milling is further broken down into conventional milling, where the cutter rotates opposite the direction of feed, or “up” into the workpiece; and climb milling, where the cutter rotates in the direction of feed, or “down” into the workpiece. Milling operations include plane or surface milling, endmilling, facemilling, angle milling, form milling and profiling.
- milling machine ( mill)
milling machine ( mill)
Runs endmills and arbor-mounted milling cutters. Features include a head with a spindle that drives the cutters; a column, knee and table that provide motion in the three Cartesian axes; and a base that supports the components and houses the cutting-fluid pump and reservoir. The work is mounted on the table and fed into the rotating cutter or endmill to accomplish the milling steps; vertical milling machines also feed endmills into the work by means of a spindle-mounted quill. Models range from small manual machines to big bed-type and duplex mills. All take one of three basic forms: vertical, horizontal or convertible horizontal/vertical. Vertical machines may be knee-type (the table is mounted on a knee that can be elevated) or bed-type (the table is securely supported and only moves horizontally). In general, horizontal machines are bigger and more powerful, while vertical machines are lighter but more versatile and easier to set up and operate.
- stainless steels
stainless steels
Stainless steels possess high strength, heat resistance, excellent workability and erosion resistance. Four general classes have been developed to cover a range of mechanical and physical properties for particular applications. The four classes are: the austenitic types of the chromium-nickel-manganese 200 series and the chromium-nickel 300 series; the martensitic types of the chromium, hardenable 400 series; the chromium, nonhardenable 400-series ferritic types; and the precipitation-hardening type of chromium-nickel alloys with additional elements that are hardenable by solution treating and aging.
- wear resistance
wear resistance
Ability of the tool to withstand stresses that cause it to wear during cutting; an attribute linked to alloy composition, base material, thermal conditions, type of tooling and operation and other variables.