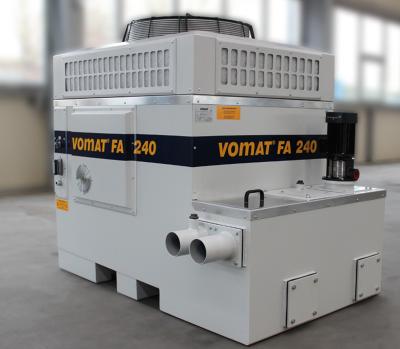
Fine filtered cooling lubricants represent an important cornerstone in tool manufacturing and are instrumental in achieving high tool quality quickly and economically. Tool manufacturers, who rely on the right technology and competence of their filtration system manufacturer, capitalize optimally on the many advantages offered by efficient coolant filtration.
Unsatisfactory grinding results, pump damage, blocked pipes, and more – this is often the result of poorly filtered cooling lubricants. Economical, reliable grinding to absolute highest standards is only possible with extremely clean grinding oils.
The cleaner and the finer the filtration results are, the better the production quality. More over if the filtration system is capable of filtering the coolant at high quality levels with prolonged service intervals; the whole process will become very economical.
Steffen Strobel, technical sales manager of the German filtration system manufacturer VOMAT, who is also very successful in the U.S. market states: "Filtered metal coolants are an important component in the value chain and should therefore not be seen as an unnecessary and negligible cost center. This way of thinking can quickly become dangerous. Working with inadequate filtration systems and outdated technology can turn out to be a quality risk and a cost burden."
An important parameter in filtration is the particle size and thus the degree of purity of the cooling lubricant after the filtration process. VOMAT fine filtration systems filter to NAS 7 (3 - 5 μm) quality and particle size. VOMAT filters operate in full-flow mode and separate dirty and clean oil. This is the prerequisite to permanently provide the manufacturing process with the cleanest grinding oil. At the same time, the system filters and cleans the machine as required. This means that the backflush cycle is initiated automatically for each individual filter element, depending on need. The other filter elements ensure a continuous clean-oil supply to the work piece while the soiled filter element is cleaned. Low heat transfer into the cooling medium, reduced energy consumption as well as economical, problem-free waste disposal is further strengths of the VOMAT technology.
In addition, the user benefits from further advantages: the wear and tear of the grinding wheel is greatly reduced when clean coolants are being used during tool grinding. As a result, fewer abrasive particles are circulated in the coolant and the grinding tools last longer. In this way, more drills or cutters can be ground by one grinding wheel. Another positive side effect is the fact, that the grinding machine's downtimes are reduced as the grinding wheels do not have to be changed and adjusted as often.
Steffen Strobel: "With optimum VOMAT filtration of his metal coolant, the tool grinder achieves long service life of his cutting tools as well as high process reliability and operating stability of his entire production system. Furthermore, it saves coolant costs and minimizes drag out through the high-performance pre-coat filters. VOMAT's filtration, cooling and disposal solutions ensure the right balance between economic and environmental issues."
VOMAT micro filtration systems are available in various sizes from 70 to 960 liters/minute (18 to 254 gpm) filter capacity. Thanks to a variety of add-on modules, VOMAT systems can be tailored to every conceivable plant configuration. From smaller stand alone units to plant wide high capacity central systems can be realized without major problems.
Steffen Strobel: "Especially high volume production of milling and drilling tools, warrant the use of a central system in more than one respect. From clean oil to profitable carbide sludge collection and disposal VOMAT filtration specialists provide individual solutions to enable the tool manufacturer to tap into these advantages."
Contact Details
Related Glossary Terms
- abrasive
abrasive
Substance used for grinding, honing, lapping, superfinishing and polishing. Examples include garnet, emery, corundum, silicon carbide, cubic boron nitride and diamond in various grit sizes.
- coolant
coolant
Fluid that reduces temperature buildup at the tool/workpiece interface during machining. Normally takes the form of a liquid such as soluble or chemical mixtures (semisynthetic, synthetic) but can be pressurized air or other gas. Because of water’s ability to absorb great quantities of heat, it is widely used as a coolant and vehicle for various cutting compounds, with the water-to-compound ratio varying with the machining task. See cutting fluid; semisynthetic cutting fluid; soluble-oil cutting fluid; synthetic cutting fluid.
- gang cutting ( milling)
gang cutting ( milling)
Machining with several cutters mounted on a single arbor, generally for simultaneous cutting.
- grinding
grinding
Machining operation in which material is removed from the workpiece by a powered abrasive wheel, stone, belt, paste, sheet, compound, slurry, etc. Takes various forms: surface grinding (creates flat and/or squared surfaces); cylindrical grinding (for external cylindrical and tapered shapes, fillets, undercuts, etc.); centerless grinding; chamfering; thread and form grinding; tool and cutter grinding; offhand grinding; lapping and polishing (grinding with extremely fine grits to create ultrasmooth surfaces); honing; and disc grinding.
- grinding wheel
grinding wheel
Wheel formed from abrasive material mixed in a suitable matrix. Takes a variety of shapes but falls into two basic categories: one that cuts on its periphery, as in reciprocating grinding, and one that cuts on its side or face, as in tool and cutter grinding.
- milling
milling
Machining operation in which metal or other material is removed by applying power to a rotating cutter. In vertical milling, the cutting tool is mounted vertically on the spindle. In horizontal milling, the cutting tool is mounted horizontally, either directly on the spindle or on an arbor. Horizontal milling is further broken down into conventional milling, where the cutter rotates opposite the direction of feed, or “up” into the workpiece; and climb milling, where the cutter rotates in the direction of feed, or “down” into the workpiece. Milling operations include plane or surface milling, endmilling, facemilling, angle milling, form milling and profiling.
- tap
tap
Cylindrical tool that cuts internal threads and has flutes to remove chips and carry tapping fluid to the point of cut. Normally used on a drill press or tapping machine but also may be operated manually. See tapping.