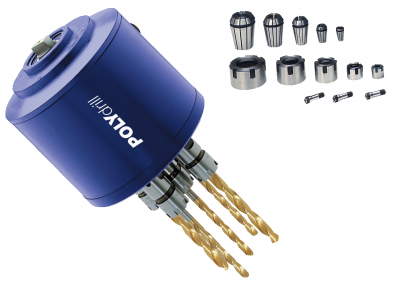
Who doesn’t know the old saw "Time is money?" Using POLYdrill multiple-spindle heads from SUHNER, many have taken advantage of this wisdom and made money the old fashioned way for 30 years and counting.
In its catalog in 1982, SUHNER introduced a new line of multiple spindle heads, which combined modern design features with high drilling performance in a fairly compact package.
Since then, SUHNER has built thousands of multiple spindle heads with gains in know-how invested in improved technology. This basic philosophy continues.
Significant gains in productivity and output are achieved through the application of standard and simultaneous multi-operation components at a relatively low investment cost.
The program range for POLYdrill multiple spindle heads is regularly up-dated and expanded. Today, our offering includes adjustable multiple spindle heads for two, three and four spindles in six different capacity classifications.
Custom-made, application-specific, fixed-spacing heads with up to 144 spindels are an enormous increase in productivity.
In addition to multiple spindle heads, SUHNER has a variety of other POLYdrill components including angle heads
for drilling, tapping and milling operations as well as back facing heads for drilling and countersinking operations.
Contact Details
Related Glossary Terms
- countersinking
countersinking
Cutting a beveled edge at the entrance of a hole so a screw head sits flush with the workpiece surface.
- gang cutting ( milling)
gang cutting ( milling)
Machining with several cutters mounted on a single arbor, generally for simultaneous cutting.
- milling
milling
Machining operation in which metal or other material is removed by applying power to a rotating cutter. In vertical milling, the cutting tool is mounted vertically on the spindle. In horizontal milling, the cutting tool is mounted horizontally, either directly on the spindle or on an arbor. Horizontal milling is further broken down into conventional milling, where the cutter rotates opposite the direction of feed, or “up” into the workpiece; and climb milling, where the cutter rotates in the direction of feed, or “down” into the workpiece. Milling operations include plane or surface milling, endmilling, facemilling, angle milling, form milling and profiling.
- sawing machine ( saw)
sawing machine ( saw)
Machine designed to use a serrated-tooth blade to cut metal or other material. Comes in a wide variety of styles but takes one of four basic forms: hacksaw (a simple, rugged machine that uses a reciprocating motion to part metal or other material); cold or circular saw (powers a circular blade that cuts structural materials); bandsaw (runs an endless band; the two basic types are cutoff and contour band machines, which cut intricate contours and shapes); and abrasive cutoff saw (similar in appearance to the cold saw, but uses an abrasive disc that rotates at high speeds rather than a blade with serrated teeth).
- tapping
tapping
Machining operation in which a tap, with teeth on its periphery, cuts internal threads in a predrilled hole having a smaller diameter than the tap diameter. Threads are formed by a combined rotary and axial-relative motion between tap and workpiece. See tap.