Contact Details
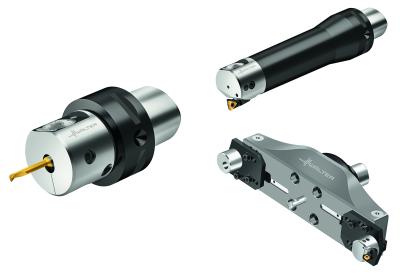
Walter has extended its line of precision boring tools with new members of the Walter Precision Boring XT family: The Walter Precision XT B5110, B5115, B5120, and B5125. The B5110 is ideal for fine boring of small diameters. It uses either a solid carbide boring bar option for diameters of 0.039-0.323 in (1-8.2 mm) or an indexable insert boring bar design for diameters 0.315-0.787 (8-20 mm).The B5115 is designed for precision boring of medium range diameters of 0.748-6.575 in. (19-167 mm). Unlike the B5110 which uses the boring bar design, the B5115 utilizes the cartridge style design, as larger space is available for the tool design to accommodate the cartridges.
The B5120, with diameters of 5.827-25.00 in. (148-625 mm) expertly covers the large diameters with its bridge and cartridge design. The bridges are made of aluminum to accommodate the weight constraints of machine tool spindles. A separate line of “reduced weight” boring bars in medium range diameters is also offered through B5125-LWS. The LWS stands for “Light Weight Selection.” The B5125 uses the same cartridges as the B5115 and B5120 thus reducing cost through modular use of cartridges across the systems. The precision dial for all the new systems boasts a dual inch/metric unit dial thus not requiring separate tools for global customers that work with dual unit systems.
These new vibration-free tools provide finish machining of precise bores (IT6–IT8) up to 6 × D, with high surface quality and are up to three times more reliable and flexible than comparable models. Their flexibility is boosted by the fact that the new Walter boring tools employ modular components such as cartridge holders and extensions, which are matched to the system, utilize an extensive range of indexable inserts suited for precision boring, and can be used for all material groups. These XT System boring tools are available tin Capto connection as well as Walter proprietary NCT and screw-fit adaptions.
There is internal coolant supply up to the cutting edge, and cartridges
for CC and TC with indexable inserts adapted for precision boring. The tools include an option for reverse machining (reverse boring) and are suitable for general metalworking, production of precision parts, and mold and die making.
Related Glossary Terms
- boring
boring
Enlarging a hole that already has been drilled or cored. Generally, it is an operation of truing the previously drilled hole with a single-point, lathe-type tool. Boring is essentially internal turning, in that usually a single-point cutting tool forms the internal shape. Some tools are available with two cutting edges to balance cutting forces.
- boring bar
boring bar
Essentially a cantilever beam that holds one or more cutting tools in position during a boring operation. Can be held stationary and moved axially while the workpiece revolves around it, or revolved and moved axially while the workpiece is held stationary, or a combination of these actions. Installed on milling, drilling and boring machines, as well as lathes and machining centers.
- coolant
coolant
Fluid that reduces temperature buildup at the tool/workpiece interface during machining. Normally takes the form of a liquid such as soluble or chemical mixtures (semisynthetic, synthetic) but can be pressurized air or other gas. Because of water’s ability to absorb great quantities of heat, it is widely used as a coolant and vehicle for various cutting compounds, with the water-to-compound ratio varying with the machining task. See cutting fluid; semisynthetic cutting fluid; soluble-oil cutting fluid; synthetic cutting fluid.
- indexable insert
indexable insert
Replaceable tool that clamps into a tool body, drill, mill or other cutter body designed to accommodate inserts. Most inserts are made of cemented carbide. Often they are coated with a hard material. Other insert materials are ceramic, cermet, polycrystalline cubic boron nitride and polycrystalline diamond. The insert is used until dull, then indexed, or turned, to expose a fresh cutting edge. When the entire insert is dull, it is usually discarded. Some inserts can be resharpened.
- metalworking
metalworking
Any manufacturing process in which metal is processed or machined such that the workpiece is given a new shape. Broadly defined, the term includes processes such as design and layout, heat-treating, material handling and inspection.
- titanium nitride ( TiN)
titanium nitride ( TiN)
Added to titanium-carbide tooling to permit machining of hard metals at high speeds. Also used as a tool coating. See coated tools.