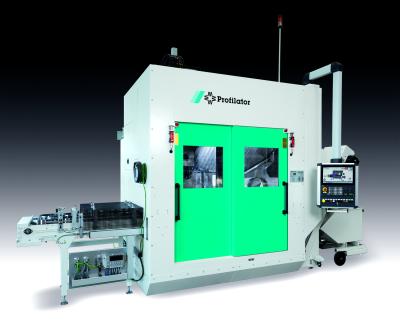
German Machine Tools of America (GMTA) (Ann Arbor, MI) is now selling Profilator 300-V with linear drives in the North American market.
This modular machine platform used to cut gears, is equipped with one or two workpiece spindles in a compact design. It offers maximum flexibility due to modular design and is individually configurable for various machining processes (i.e. SCUDDING®, hobbing, cycloidal milling, pointing, chamfering and deburring). State-of-the-art linear drives in the X and Y axis, as well as a torque drive in the A axis offers high machine dynamics for short cycle times and maximum accuracy/low costs. High machine rigidity is available for HARD SCUDDING® of inner and outer diameters.
Additional features include an intuitive user interface for easy setup and programming and is industry 4.0 ready (optionally equipped with additional sensors). Various automation concepts are easily adaptable. The 300-V is easy to set up and maintain due to the “walk-in” machining area. An optional tool charger is available for maximum machining efficiency.
All Profilator machines are designed for dry machining. This brings several advantages such as: an optimized machining area, no coolant and no coolant mist. The inverted, vertical spindle(s) allow free chip fall into the central chip conveyor at the bottom, while no coolant means no washing of the workpiece is required and the lack of coolant mist signifies an extraction system isn’t needed.
Users of the Profilator 300-V reap benefits regarding the environment, energy efficiency, investment and operating costs. There is no carryover of the coolant outside the machine. Therefore, no disposal is required for this environmentally friendly machine. It saves energy and money by not requiring a coolant and extraction system. Lower operating costs are achieved thanks to a reduction in energy costs and media supply.
To download the full catalog go to: https://bernardandcompany.com/wp-content/uploads/2023/09/Profilator-300-V.pdf
Contact Details
Related Glossary Terms
- arbor
arbor
Shaft used for rotary support in machining applications. In grinding, the spindle for mounting the wheel; in milling and other cutting operations, the shaft for mounting the cutter.
- chamfering
chamfering
Machining a bevel on a workpiece or tool; improves a tool’s entrance into the cut.
- coolant
coolant
Fluid that reduces temperature buildup at the tool/workpiece interface during machining. Normally takes the form of a liquid such as soluble or chemical mixtures (semisynthetic, synthetic) but can be pressurized air or other gas. Because of water’s ability to absorb great quantities of heat, it is widely used as a coolant and vehicle for various cutting compounds, with the water-to-compound ratio varying with the machining task. See cutting fluid; semisynthetic cutting fluid; soluble-oil cutting fluid; synthetic cutting fluid.
- gang cutting ( milling)
gang cutting ( milling)
Machining with several cutters mounted on a single arbor, generally for simultaneous cutting.
- milling
milling
Machining operation in which metal or other material is removed by applying power to a rotating cutter. In vertical milling, the cutting tool is mounted vertically on the spindle. In horizontal milling, the cutting tool is mounted horizontally, either directly on the spindle or on an arbor. Horizontal milling is further broken down into conventional milling, where the cutter rotates opposite the direction of feed, or “up” into the workpiece; and climb milling, where the cutter rotates in the direction of feed, or “down” into the workpiece. Milling operations include plane or surface milling, endmilling, facemilling, angle milling, form milling and profiling.
- modular design ( modular construction)
modular design ( modular construction)
Manufacturing of a product in subassemblies that permits fast and simple replacement of defective assemblies and tailoring of the product for different purposes. See interchangeable parts.