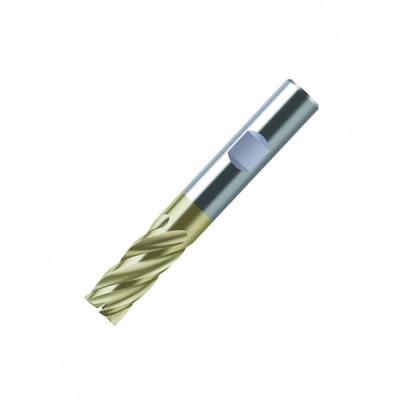
Walter has introduced a new version of its Walter Prototyp Proto▪maxST high-performance, solid-carbide milling tool designed for optimal performance on steel with secondary applications in stainless steel. This new entry in the Walter Prototyp lineup is called the Proto·maxST Z-5, available with the same tough yet wear-resistant TAZ coating that is offered in the original 3- and 4-flute variations of the Proto·maxST.
The new mill has five cutting edges, differing from the previous entries that were limited to three and four. It is available with a Weldon shank configuration for secure clamping, with or without corner radius, and without a reduced neck for greater stability by using the maximum amount of carbide. It possesses a helix angle of 35° and is offered in the diameter range of 6-25 mm.
The new Proto·maxST Z-5 delivers high productivity by reducing process times, along with high process reliability by significantly reducing the risk of tool breakage. In addition, the TAZ coating dramatically increases tool life, and costs are lowered because of savings on coolant, as dry machining is the recommended approach.
Importantly, the Proto·maxST Z-5 is well-suited for dynamic milling, a highly productive machining strategy that is growing in popularity. Dynamic milling is a method of defining toolpaths so as to maintain a constant tool engagement angle. This allows a large DOC to be taken, which fully utilizes the entire cutting edge of the tool. This is normally combined with radial chip thinning, accomplished by taking a small radial DOC; around 10-15 percent of the tool diameter is actually engaged in the cut. This combination allows for very high speeds, plus very high feed rates and deep DOCs, typically leading to high material-removal rates and lower cutting forces.
Contact Details
Related Glossary Terms
- coolant
coolant
Fluid that reduces temperature buildup at the tool/workpiece interface during machining. Normally takes the form of a liquid such as soluble or chemical mixtures (semisynthetic, synthetic) but can be pressurized air or other gas. Because of water’s ability to absorb great quantities of heat, it is widely used as a coolant and vehicle for various cutting compounds, with the water-to-compound ratio varying with the machining task. See cutting fluid; semisynthetic cutting fluid; soluble-oil cutting fluid; synthetic cutting fluid.
- feed
feed
Rate of change of position of the tool as a whole, relative to the workpiece while cutting.
- gang cutting ( milling)
gang cutting ( milling)
Machining with several cutters mounted on a single arbor, generally for simultaneous cutting.
- helix angle
helix angle
Angle that the tool’s leading edge makes with the plane of its centerline.
- milling
milling
Machining operation in which metal or other material is removed by applying power to a rotating cutter. In vertical milling, the cutting tool is mounted vertically on the spindle. In horizontal milling, the cutting tool is mounted horizontally, either directly on the spindle or on an arbor. Horizontal milling is further broken down into conventional milling, where the cutter rotates opposite the direction of feed, or “up” into the workpiece; and climb milling, where the cutter rotates in the direction of feed, or “down” into the workpiece. Milling operations include plane or surface milling, endmilling, facemilling, angle milling, form milling and profiling.
- milling machine ( mill)
milling machine ( mill)
Runs endmills and arbor-mounted milling cutters. Features include a head with a spindle that drives the cutters; a column, knee and table that provide motion in the three Cartesian axes; and a base that supports the components and houses the cutting-fluid pump and reservoir. The work is mounted on the table and fed into the rotating cutter or endmill to accomplish the milling steps; vertical milling machines also feed endmills into the work by means of a spindle-mounted quill. Models range from small manual machines to big bed-type and duplex mills. All take one of three basic forms: vertical, horizontal or convertible horizontal/vertical. Vertical machines may be knee-type (the table is mounted on a knee that can be elevated) or bed-type (the table is securely supported and only moves horizontally). In general, horizontal machines are bigger and more powerful, while vertical machines are lighter but more versatile and easier to set up and operate.
- shank
shank
Main body of a tool; the portion of a drill or similar end-held tool that fits into a collet, chuck or similar mounting device.