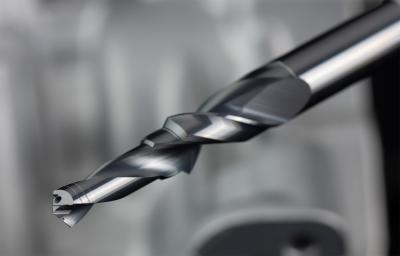
EMUGE-FRANKEN USA, a leading manufacturer of high-performance taps, thread mills, end mills, drills, and other rotary tools, has announced the introduction of PunchDrill, a totally new drill design offering high feed drilling which doubles the feed rate compared to standard drills without increasing the axial force or spindle speed. PunchDrill reduces machining forces and optimizes chip-breaking, producing cycle time savings of 50% or more when machining cast aluminum alloys with at least 7% Si content and magnesium alloys. EMUGE PunchDrill results in shorter machining times, fewer tool changes, and high metal removal rates, in addition to higher productivity and reduced power consumption.
“At a time when aluminum usage is steadily growing, we are pleased to offer our customers the fastest drill available on the market -- another innovative EMUGE cutting tool solution that significantly saves time and enhances productivity,” said Bob Hellinger, President of EMUGE-FRANKEN USA.
PunchDrill features patent-pending geometry with an innovative chip breaker which produces short chips to control machining forces. The new drill also has newly developed surface treatments and a hard diamond-like coating specially designed for this application to provide reliable chip removal and increased process reliability. When high-speed PunchDrill is used at the recommended feed and speed, axial force is reduced by half. The increase of the feed at the same rotational speed results in a significant decrease of machining time with less machine wear, while retaining tool life. This in turn reduces machine power consumption, saving costs and supporting sustainability.
The exceptional self-centering capability of the drill tip on PunchDrill enables the best possible positioning accuracy on holes. EMUGE PunchDrill is available in drilling depth ranges up to approximately 8 x D, the nominal diameter range from 0.129" to 0.472" (3.3 mm to 12 mm). Machining is done with a normal drilling cycle on CNC machines with cutting speeds and coolant pressures similar to conventional drilling. Even on unstable parts and clamping, PunchDrill can perform with greater process reliability. PunchDrill can also perform as a step tool.
Contact Details
Related Glossary Terms
- alloys
alloys
Substances having metallic properties and being composed of two or more chemical elements of which at least one is a metal.
- aluminum alloys
aluminum alloys
Aluminum containing specified quantities of alloying elements added to obtain the necessary mechanical and physical properties. Aluminum alloys are divided into two categories: wrought compositions and casting compositions. Some compositions may contain up to 10 alloying elements, but only one or two are the main alloying elements, such as copper, manganese, silicon, magnesium, zinc or tin.
- axial force
axial force
When drilling, a force that is directed axially—along the direction of machining. The magnitude of an axial force rises with the drill’s diameter and the chisel edge’s width. Axial force is also known as thrust. When turning and boring, the term “feed force” is commonly used instead of “axial force.” See cutting force.
- computer numerical control ( CNC)
computer numerical control ( CNC)
Microprocessor-based controller dedicated to a machine tool that permits the creation or modification of parts. Programmed numerical control activates the machine’s servos and spindle drives and controls the various machining operations. See DNC, direct numerical control; NC, numerical control.
- coolant
coolant
Fluid that reduces temperature buildup at the tool/workpiece interface during machining. Normally takes the form of a liquid such as soluble or chemical mixtures (semisynthetic, synthetic) but can be pressurized air or other gas. Because of water’s ability to absorb great quantities of heat, it is widely used as a coolant and vehicle for various cutting compounds, with the water-to-compound ratio varying with the machining task. See cutting fluid; semisynthetic cutting fluid; soluble-oil cutting fluid; synthetic cutting fluid.
- feed
feed
Rate of change of position of the tool as a whole, relative to the workpiece while cutting.