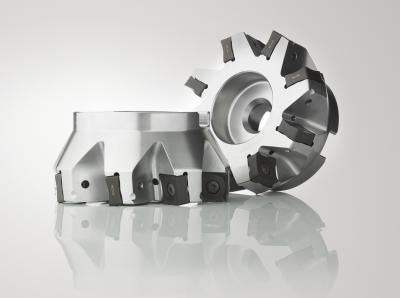
The new R220.88 facemilling cutter family from Seco features inserts with eight cutting edges and optimized geometries that provide excellent tool life and reduced cutting forces. The cutter body’s 88-degree lead angle allows for large depths of cut with smaller insert sizes, as compared to 45-degree lead angle facemills. Its design also allows the new cutter to machine closer to workpiece side walls as well as intricate part clamping workholding systems when necessary.
Designed for roughing and semifinishing applications, the R220.88 is ideal for machining cast iron and steels in the general machining and automotive segments. The cutter body is made of Idun material, a corrosion-resistant stainless steel that offers longevity and durability along with being environmentally friendly due to the elimination of the nickel coating process.
The cutter body is available in diameters ranging from 2.00" to 6.00" (50 mm to 160 mm) with the size 12 insert and 3.00" to 6.00" (63 mm to 160 mm) with the size 16 insert. Each diameter is offered with a standard pitch variant and a close-pitch variant to provide the best match to an application’s specific needs. The size 12 R220.88 achieves a maximum depth of cut of 0.35" (9 mm), while size 16 reaches an impressive 0.51" (13 mm) maximum depth of cut. Right-hand versions of the cutter body are standard with left-hand versions available on special order, allowing integration into systems with dual spindles performing simultaneous milling operations.
The R220.88 is compatible with Seco’s SNMU inserts, which are secured with a center lock screw, eliminating the need for wedges to secure the insert in the pocket. The eight cutting edges on these inserts offer double the cutting edges over four-edged inserts to help reduce tooling costs.
With its neutral design, the SNMU insert can be applied in right-hand or left-hand milling applications. Available insert geometries include M10 and MD13 for size 12 and M10 and MD16 for size 16, with an insert grade offering that includes MK1500, MK2050, MP1500, MP2500, MS2500 and F40M. An integrated wiper flat ensures a good surface finish for semifinishing applications, and optimized geometries for reduced cutting forces with the M10. The heavy edge protection with the MD13 and MD16 inserts are ideal for difficult facemilling operations, such as interrupted cuts.
Contact Details
Related Glossary Terms
- depth of cut
depth of cut
Distance between the bottom of the cut and the uncut surface of the workpiece, measured in a direction at right angles to the machined surface of the workpiece.
- facemilling
facemilling
Form of milling that produces a flat surface generally at right angles to the rotating axis of a cutter having teeth or inserts both on its periphery and on its end face.
- flat ( screw flat)
flat ( screw flat)
Flat surface machined into the shank of a cutting tool for enhanced holding of the tool.
- gang cutting ( milling)
gang cutting ( milling)
Machining with several cutters mounted on a single arbor, generally for simultaneous cutting.
- lead angle
lead angle
Angle between the side-cutting edge and the projected side of the tool shank or holder, which leads the cutting tool into the workpiece.
- milling
milling
Machining operation in which metal or other material is removed by applying power to a rotating cutter. In vertical milling, the cutting tool is mounted vertically on the spindle. In horizontal milling, the cutting tool is mounted horizontally, either directly on the spindle or on an arbor. Horizontal milling is further broken down into conventional milling, where the cutter rotates opposite the direction of feed, or “up” into the workpiece; and climb milling, where the cutter rotates in the direction of feed, or “down” into the workpiece. Milling operations include plane or surface milling, endmilling, facemilling, angle milling, form milling and profiling.
- pitch
pitch
1. On a saw blade, the number of teeth per inch. 2. In threading, the number of threads per inch.
- wiper
wiper
Metal-removing edge on the face of a cutter that travels in a plane perpendicular to the axis. It is the edge that sweeps the machined surface. The flat should be as wide as the feed per revolution of the cutter. This allows any given insert to wipe the entire workpiece surface and impart a fine surface finish at a high feed rate.