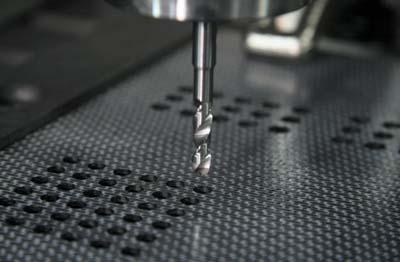
Engineers from Precision Dormer are working with customers all over the world to develop a variety of tooling solutions for a wide range of composite machining needs. Typical clients include not just leading manufacturers of commercial aircraft but also companies involved in the construction of luxury yachts and production of satellites.
Ricky Payling, one of Precision Dormer's key account managers for aerospace and composites, has spearheaded the company's growing reputation in this field. Ricky said: "Precision Dormer's research technology center has enabled us to gain a unique insight into the properties and machining characteristics of composite materials, which can differ greatly from application to application. Consequently, our tooling solutions can be tailored to each individual application. This is where our substantial knowledge and experience of composites really counts."
One of the more common problems faced by Ricky's team is the machining of "stack" materials when two different materials, such as aluminum and carbon fiber, are machined together. The key here is in finding a one-shot drilling solution that provides a clean hole without causing damage to the component or necessitating additional machining processes. One such challenge was addressed by Precision Dormer when they were asked to advise on a drilling application involving a wing skin assembly. Here, the customer needed to drill a stack material comprising of 10mm-thick aluminum and 4mm-thick carbon fiber.
"Ordinarily," Ricky says, "the customer would have to cut a small diameter hole first, gradually opening this out to the finished size. This not only takes time but also involves the use of several different tools. However, with our R790 carbide composite drill we were able to machine through-holes with no delamination or splintering on the carbon fibre and no exit burr on the aluminum." Other significant achievements have included machining composite stacks with a glass cloth exit face. "With this type of material," Ricky explains, "it is extremely difficult to produce a hole with a perfectly clean periphery. However, after consideration of the required geometry, we were able to manufacture prototype tools that consistently delivered holes with excellent exit quality, with no signs of delamination, splintering or fraying of the glass cloth."
Contact Details
Related Glossary Terms
- burr
burr
Stringy portions of material formed on workpiece edges during machining. Often sharp. Can be removed with hand files, abrasive wheels or belts, wire wheels, abrasive-fiber brushes, waterjet equipment or other methods.
- composites
composites
Materials composed of different elements, with one element normally embedded in another, held together by a compatible binder.