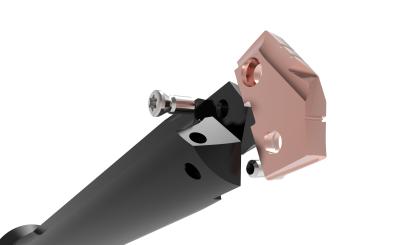
Allied Machine & Engineering says its line of replaceable tip Original T-A drill systems significantly reduces downtime compared to solid tools. The T-A drill system features high-performance inserts and holders ideal for automotive holemaking applications used in manufacturing engine blocks, crankshafts, piston and suspension parts. Cost per hole using T-A drill systems can be 25-50 percent lower than other options in the marketplace.
With the T-A drill line, operators reportedly get a perfect factory-ground surface or drill point every time they insert the drill tip – with no downtime required to alter tool offsets due to regrinding operations. The replaceable tips are consistent every time, unlike variations often encountered when using drills reground by different machinists.
Allied offers cast iron (-CI) geometries for its T-A drill that are ideal for automotive applications. Featuring lower rake angles and a tougher cutting edge to make them more resilient, the (-CI) drill tips are a good choice for blocks and heads made out of cast iron. Other application-specific drill tips are also available. Allied develops custom-configured shapes for tools, including a special form end for the end of a crankshaft.
Innovative coating options for the T-A drill include Allied’s exclusive AM200 coating, which improves performance and extends tool life. A variety of insert grades are available for automotive applications, including C3 carbide, a wear-resistant carbide offering the best life in gray cast iron and C2 carbide, a good choice for aluminum and other nonferrous applications.
C1 options are available for steel applications using the GEN2 T-A drill, which fits into the same holder as the Original T-A and provides even better performance and longer tool life for automotive applications.
Contact Details
Related Glossary Terms
- rake
rake
Angle of inclination between the face of the cutting tool and the workpiece. If the face of the tool lies in a plane through the axis of the workpiece, the tool is said to have a neutral, or zero, rake. If the inclination of the tool face makes the cutting edge more acute than when the rake angle is zero, the rake is positive. If the inclination of the tool face makes the cutting edge less acute or more blunt than when the rake angle is zero, the rake is negative.