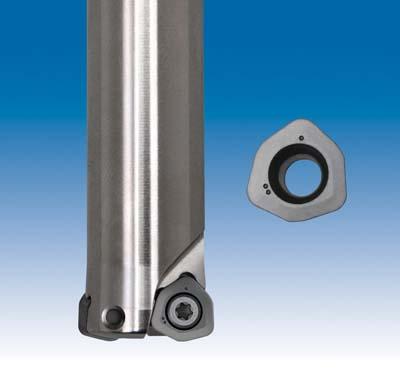
New Mini-Feed cutters and inserts, part of Dapra Corp.'s high-feed RHINO-FEED line, reportedly allow for feed rates up to five times faster than normal in light-DOC applications.
Dapra's Mini-Feed line is optimized for cuts of .500" to 1.000" diameter and a maximum depth of .030", with inserts featuring three usable edges. End mills and modular heads are available with one, two or three flutes. Mini-Feed inserts feature the smallest inscribed circle (8mm IC) of any of Dapra's RHINO-FEED options and operate at light to moderate FPT, making them ideal for detail roughing and high-speed machining, especially in small machines. Thanks to its positive geometry, Mini-Feed is suitable for use with all materials.
Dapra's RHINO-FEED line adjusts feed rates to compensate for the significant chip thinning that occurs during high-feed milling when an extreme lead angle is utilized. Mid-Feed and Heavy-Feed cutters and inserts are also available for diameters up to 4" and depths of cut up to .060".
Contact Details
Related Glossary Terms
- feed
feed
Rate of change of position of the tool as a whole, relative to the workpiece while cutting.
- flutes
flutes
Grooves and spaces in the body of a tool that permit chip removal from, and cutting-fluid application to, the point of cut.
- gang cutting ( milling)
gang cutting ( milling)
Machining with several cutters mounted on a single arbor, generally for simultaneous cutting.
- inscribed circle ( IC)
inscribed circle ( IC)
Imaginary circle that touches all sides of an insert. Used to establish size. Measurements are in fractions of an inch and describe the diameter of the circle.
- lead angle
lead angle
Angle between the side-cutting edge and the projected side of the tool shank or holder, which leads the cutting tool into the workpiece.
- milling
milling
Machining operation in which metal or other material is removed by applying power to a rotating cutter. In vertical milling, the cutting tool is mounted vertically on the spindle. In horizontal milling, the cutting tool is mounted horizontally, either directly on the spindle or on an arbor. Horizontal milling is further broken down into conventional milling, where the cutter rotates opposite the direction of feed, or “up” into the workpiece; and climb milling, where the cutter rotates in the direction of feed, or “down” into the workpiece. Milling operations include plane or surface milling, endmilling, facemilling, angle milling, form milling and profiling.