Contact Details
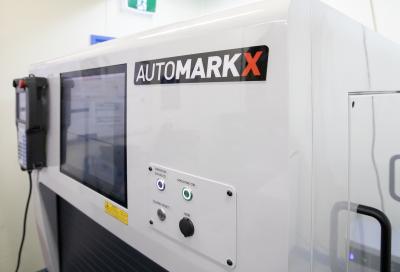
Traceability is a fast-emerging trend in the manufacturing industry. It is defined as the ability to retrieve the full history or location of an item or product by means of recorded identification. In the tool making industry, the requirement to trace an individual tool and the ability to determine its usage and/or re-grinding history has become an industry standard, allowing end users to maintain the highest tool quality and productivity.
In the tool making production process, tool laser marking is a necessary step that not only serves the purpose of providing basic tool geometry information, but also includes information pertaining to tool provenance and regrinding history. A basic requirement of laser marking is to have identification that is clear, and easy to read and understand.
Laser is the technology of choice for tool marking for several reasons. Firstly, laser produces an indelible mark which is crucial for easy identification throughout the lifetime of the tool. The quality is consistently excellent with high contrast and minimal surface disturbance – both of which are important for cutting tool performance. Secondly, laser technology is very mature which ensures consistent high reliability over many years.
A challenge with using standard manual laser marking stations is that it is among the most labor-intensive activities of any company. Automating the laser marking task is a direct solution to address this, with multiple benefits. Automation saves on labor cost, eliminates human error and frees up staff to perform more value-adding activities. After the initial investment, this asset will perform long-term over many years with a very low level of maintenance required.
ANCA offers two automatic laser marking options for a range of applications and individual requirements.
RoboMate LaserEtch
RoboMate LaserEtch is an integrated laser system that can be added to the ANCA RoboMate loader for the TX and MX platforms, allowing laser marking of individual tools in-process. This is a convenient, compact and flexible solution. After grinding, the tool is automatically laser marked, for example tool ID and graphics such as a company logo – all without any increase to tool takt time. This solution means:
- No need for additional equipment on the factory floor
- Reduction of Work in Progress thanks to smart utilization of robot loader idle cycle time
- Easy to use, friendly software
AutoMarkX
An automatic stand-alone laser marking station, the AutoMarkX is the latest addition to ANCA’s family of tool production solutions. The operator simply loads up to two full pallets of tools and the robot performs the laser marking operations, freeing up staff to take care of other tasks in the factory. The unit can accommodate a wide range of tool sizes, making it a versatile proposition for many manufacturers.
- AutoMarkX accepts up to two full pallets of tools, which means you can mark a large batch of tools unmanned.
- Flexible marking means the message could be etched on a single side of the shank or on opposite sides of the shank as well as at the end of tool. The last option is particularly useful for applications where a unique tool identification code (e.g. Datamatrix) needs to be etched on the tool. Codes like Datamatrix are usually etched on the shank where they risk the exposure to excessive surface wear, rendering them unreadable. The end of tool is the best location to etch this type of code to overcome this issue.
- AutoMarkX accepts different pallet standards which means it can be easily integrated into your production process and currently used pallets.
- It is ANCA Integrated Manufacturing System (AIMS) ready
ANCA’s laser marking systems can be integrated into the AIMS Server to become a part of a fully automated production cell. In this case, sequential tool production processes are fully automated right through to laser marking on the tool. AIMS also provides a platform for extended functionality including tool traceability and serialization.
Related Glossary Terms
- grinding
grinding
Machining operation in which material is removed from the workpiece by a powered abrasive wheel, stone, belt, paste, sheet, compound, slurry, etc. Takes various forms: surface grinding (creates flat and/or squared surfaces); cylindrical grinding (for external cylindrical and tapered shapes, fillets, undercuts, etc.); centerless grinding; chamfering; thread and form grinding; tool and cutter grinding; offhand grinding; lapping and polishing (grinding with extremely fine grits to create ultrasmooth surfaces); honing; and disc grinding.
- inner diameter ( ID)
inner diameter ( ID)
Dimension that defines the inside diameter of a cavity or hole. See OD, outer diameter.
- shank
shank
Main body of a tool; the portion of a drill or similar end-held tool that fits into a collet, chuck or similar mounting device.