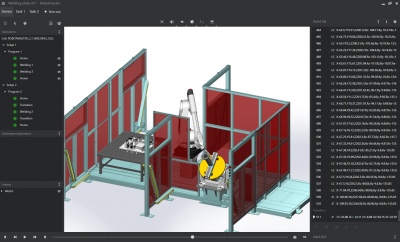
Hypertherm is launching Robotmaster V7, a task-based robot programming platform built from scratch on a new architecture. Robotmaster V7 caters to process experts to make robot programming easy and intuitive, even for first-time robot users. This new programming platform builds on the performance of Robotmaster’s offline programming CAD/CAM software that was first introduced in 2002.
To create this new architecture, Hypertherm’s Robotic Software group, the developers of Robotmaster, added new experts to its team in mathematical optimization who understand artificial intelligence and deep machine learning, as well as simulation and game experts who are passionate about user interaction and applying their skills in the industrial space.
Because Robotmaster V7 uses integrated CAD/CAM functionality, for the first time, the power of Robotmaster can be used by welding, cutting and other process experts without buying or learning complex CAD/CAM software. As in past versions, Robotmaster V7 imports paths, but now makes it even easier for end users to leverage any CAD/CAM tool choice. It is an intuitive tool that anyone could use, with or without robotics expertise. It bridges the gap between robots and manufacturing by providing easy programming solutions for part manufacturing.
“Robotics and CAD/CAM expertise are not a prerequisite to create error-free robot programs with Robotmaster V7 since it is a task-based robot programming platform built around the user, for the user,” said Chahe Bakmazjian, head of strategy, robotic software. “Robotmaster V7 also has unmatched flexibility and configurability and transfers the job to another robot brand or workcell, without task reprogramming. This is an industry first.”
The new Robotmaster V7 software release targets automatic integrated welding and contour programming including trimming, cutting, dispensing and deburring, as well as drilling and fastening. It navigates complex part geometries and optimizes robot paths while synchronizing movements and preventing collisions between one or more robots, parts and tooling. It can be used for offline robotic programming in a variety of industries including aerospace, automotive, consumer electronics, power generation/energy and welding. Subsequent modules will enable additional tasks, including surfacing, 3D milling, additive manufacturing and inspection. The current version of Robotmaster offers support for these applications; however once V7 support is available for these applications, they will be more automated and easier to use.
Future editions will incorporate specialized task sharing tools for multi-robot workcells and Industry 4.0 capability, enabling the Smart Factory.
“The Robotmaster team saw the trend for multi-robot cells, with robots performing a combination of processes, including material removal, welding and polishing,” said Bakmazjian. “Our prior software supported one robot for one task. Our next generation would need to support any number of anything – more than one robot, more than one tooling and process, in multiple types of settings, and with any number of tasks. This new framework allows our users to exploit the full capabilities of a multi-robot workcell with easy-to-use, advanced task sharing tools.”
Contact Details
Related Glossary Terms
- gang cutting ( milling)
gang cutting ( milling)
Machining with several cutters mounted on a single arbor, generally for simultaneous cutting.
- milling
milling
Machining operation in which metal or other material is removed by applying power to a rotating cutter. In vertical milling, the cutting tool is mounted vertically on the spindle. In horizontal milling, the cutting tool is mounted horizontally, either directly on the spindle or on an arbor. Horizontal milling is further broken down into conventional milling, where the cutter rotates opposite the direction of feed, or “up” into the workpiece; and climb milling, where the cutter rotates in the direction of feed, or “down” into the workpiece. Milling operations include plane or surface milling, endmilling, facemilling, angle milling, form milling and profiling.
- polishing
polishing
Abrasive process that improves surface finish and blends contours. Abrasive particles attached to a flexible backing abrade the workpiece.
- robotics
robotics
Discipline involving self-actuating and self-operating devices. Robots frequently imitate human capabilities, including the ability to manipulate physical objects while evaluating and reacting appropriately to various stimuli. See industrial robot; robot.
- sawing machine ( saw)
sawing machine ( saw)
Machine designed to use a serrated-tooth blade to cut metal or other material. Comes in a wide variety of styles but takes one of four basic forms: hacksaw (a simple, rugged machine that uses a reciprocating motion to part metal or other material); cold or circular saw (powers a circular blade that cuts structural materials); bandsaw (runs an endless band; the two basic types are cutoff and contour band machines, which cut intricate contours and shapes); and abrasive cutoff saw (similar in appearance to the cold saw, but uses an abrasive disc that rotates at high speeds rather than a blade with serrated teeth).