Contact Details
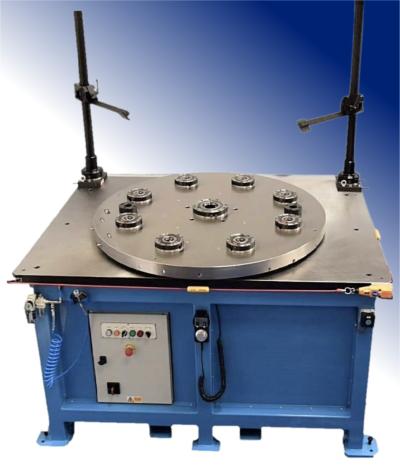
SMW Autoblok, a world leader in the design and manufacture of rotational chucks, stationary workholding, tooling and custom engineered solutions for the machine tool industry, introduces the Series 800 and 1200 custom Setup Stations that offer complete interchangeability across all machines with a common interface. Use Setup stations in a variety of standard and custom machining applications including turning, 5-axis machining, milling, inspection, and finishing operations.
With new custom Setup Stations featuring a variety of Zero Point stationary workholding systems, customers can quickly create a common interface from machine-to-machine using our offline Setup Station and the same Zero Point configuration on all machines.
Once the part is set, Setup Stations allow users to hold and locate the part and move the APS fixture from machine-to-machine with extremely high repeatability and zero setup time since there is a common interface across all machines. This is especially important due to the customization that is often required for special applications including automation.
Available in diameters of 800 mm and 1200 mm (custom sizes per application requirements), the Series 800 offers a maximum swing of 1100 mm and max weight of 1500 kg for the fixture plate and components. The Series 1200 features a maximum swing of 1700 mm and weight of 2000 kg. Both models feature an RPM of 0 to 3 and are available in voltages of 220, 240, 380 and 480.
The additional features and benefits of the APS and custom setup tables include:
- Repeatability within 0.005 mm
- Handset jogging function with 3 speed selections
- Safety pull cord
- Eliminates on-machine setup
- Dramatically increases machine productivity by loading and qualifying components offline
Related Glossary Terms
- fixture
fixture
Device, often made in-house, that holds a specific workpiece. See jig; modular fixturing.
- gang cutting ( milling)
gang cutting ( milling)
Machining with several cutters mounted on a single arbor, generally for simultaneous cutting.
- milling
milling
Machining operation in which metal or other material is removed by applying power to a rotating cutter. In vertical milling, the cutting tool is mounted vertically on the spindle. In horizontal milling, the cutting tool is mounted horizontally, either directly on the spindle or on an arbor. Horizontal milling is further broken down into conventional milling, where the cutter rotates opposite the direction of feed, or “up” into the workpiece; and climb milling, where the cutter rotates in the direction of feed, or “down” into the workpiece. Milling operations include plane or surface milling, endmilling, facemilling, angle milling, form milling and profiling.
- turning
turning
Workpiece is held in a chuck, mounted on a face plate or secured between centers and rotated while a cutting tool, normally a single-point tool, is fed into it along its periphery or across its end or face. Takes the form of straight turning (cutting along the periphery of the workpiece); taper turning (creating a taper); step turning (turning different-size diameters on the same work); chamfering (beveling an edge or shoulder); facing (cutting on an end); turning threads (usually external but can be internal); roughing (high-volume metal removal); and finishing (final light cuts). Performed on lathes, turning centers, chucking machines, automatic screw machines and similar machines.