Contact Details
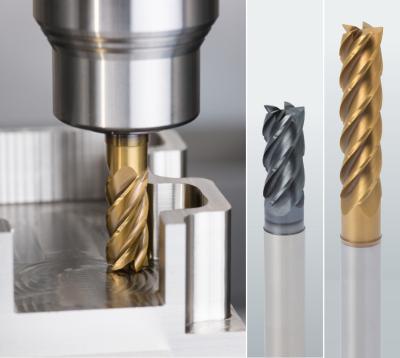
Emuge Corp. has introduced a new line of solid-carbide endmills with geometry and chipbreakers designed specifically for trochoidal milling. Emuge’s new Trochoidal endmills provide increased metal-removal rates of more than 30 percent, fewer toolpaths and longer tool life, while enabling a high axial depth of cut of up to 4XD. The Trochoidal endmill series was developed specifically for advanced milling strategies available in modern CAM software to optimize the calculation of milling paths and avoid unproductive tool motion.
Trochoidal milling is a cutting strategy growing in use that involves the overlapping of circular cutting paths with linear movement and is especially suitable for difficult-to-machine materials and thin-walled components. The small contact angle on the tool reduces heat generation during machining and promotes less thermal stress, reportedly increasing tool life. The endmill is fully utilized over the entire flute length, resulting in wear that is evenly spaced over the full cutting edge, which also contributes to longer tool life. In addition, high MRR can be generated even on low-powered machines and wear is reduced during full slot milling.
Emuge Trochoidal endmills feature low-vibration characteristics, such as variable spacing, variable helix angles and improved micro-geometries, along with high-performance coatings of TiN/TiALN or ALCR and a submicrograin carbide substrate. In addition, the newly developed chipbreaker geometry reduces axial pull-out force and minimizes the risk of chip build-up in pockets, because the resulting smaller chips can be easily removed with compressed air or coolant.
The tools are available in two cutting geometries: Jet-Cut for roughing and finishing steel , and through-coolant TiNox-Cut for process-reliable roughing in tough materials, such as Inconel, titanium and stainless steel. Standard and long-length rougher/finishers with flute length/diameter ratios of 2:1, 3:1 and 4:1 are available for applications in a range of materials.
Related Glossary Terms
- chipbreaker
chipbreaker
Groove or other tool geometry that breaks chips into small fragments as they come off the workpiece. Designed to prevent chips from becoming so long that they are difficult to control, catch in turning parts and cause safety problems.
- computer-aided manufacturing ( CAM)
computer-aided manufacturing ( CAM)
Use of computers to control machining and manufacturing processes.
- coolant
coolant
Fluid that reduces temperature buildup at the tool/workpiece interface during machining. Normally takes the form of a liquid such as soluble or chemical mixtures (semisynthetic, synthetic) but can be pressurized air or other gas. Because of water’s ability to absorb great quantities of heat, it is widely used as a coolant and vehicle for various cutting compounds, with the water-to-compound ratio varying with the machining task. See cutting fluid; semisynthetic cutting fluid; soluble-oil cutting fluid; synthetic cutting fluid.
- depth of cut
depth of cut
Distance between the bottom of the cut and the uncut surface of the workpiece, measured in a direction at right angles to the machined surface of the workpiece.
- endmill
endmill
Milling cutter held by its shank that cuts on its periphery and, if so configured, on its free end. Takes a variety of shapes (single- and double-end, roughing, ballnose and cup-end) and sizes (stub, medium, long and extra-long). Also comes with differing numbers of flutes.
- gang cutting ( milling)
gang cutting ( milling)
Machining with several cutters mounted on a single arbor, generally for simultaneous cutting.
- milling
milling
Machining operation in which metal or other material is removed by applying power to a rotating cutter. In vertical milling, the cutting tool is mounted vertically on the spindle. In horizontal milling, the cutting tool is mounted horizontally, either directly on the spindle or on an arbor. Horizontal milling is further broken down into conventional milling, where the cutter rotates opposite the direction of feed, or “up” into the workpiece; and climb milling, where the cutter rotates in the direction of feed, or “down” into the workpiece. Milling operations include plane or surface milling, endmilling, facemilling, angle milling, form milling and profiling.