Contact Details
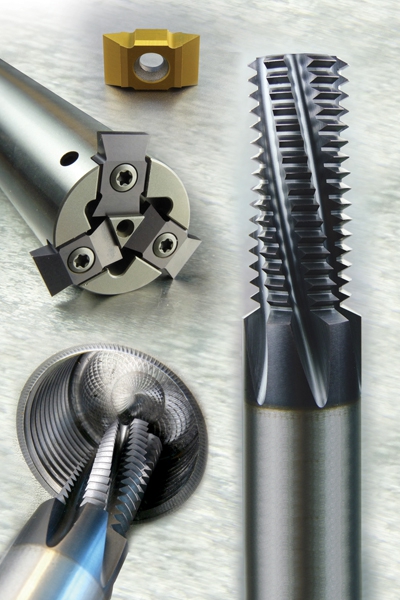
Emuge Corp. announced the introduction of an extensive, expanded thread milling program for oil and gas manufacturing applications, including a new line of solid carbide thread mills and insert thread milling systems. The recent additions to the Emuge product offering for energy applications significantly broaden the range of high performance solutions for users to meet and exceed growing oil, gas and petrochemical manufacturing challenges.
Emuge solid carbide thread mills feature a unique left hand spiral flute design, increased flute count and core diameter, and advanced multilayered TiALN-T46 coating. The combined effect of the new design features results in exceptionally high feed rates, reduced cycle times, vibration-free machining, reduced tool wear and excellent thread surface finishes, according to the company. Thread mills are available with internal coolant capability for UNC, 8UN and 12UNF thread forms. In addition, thread mills for NPT and API LP thread form sizes with extended milling section and external coolant are available. These thread mills are also capable of machining multiple thread sizes with one tool. The solid carbide thread mill program includes twenty in-stock tools, available in inch and metric shanks, in a complete range of thread form/sizes.
Emuge Insert Thread Milling Systems feature a full range of uniquely designed insert and tool bar bodies. Inserts have four usable cutting edges for long tool life and maximum cutting efficiency and are available in Acme, Stub Acme, NPT and API LP design specifications. Advanced NPT and API LP full and partial profile insert technology enhances the versatility and economy of the Emuge system. Precision ground rake and relief angles allow for high chip-per-tooth load for increased productivity.
The inserts' free cutting geometry produces low radial cutting pressure, ensuring excellent thread quality. Deep thread access and vibration-free machining are ideal for large, threaded subsea components and more. Tool bar bodies feature a modular, rigid design with precision-machined insert pockets and are available in four sizes for easy interchangeability on CNC machines with Weldon-style shanks. CAT50 and DIN/SK 50 shank designs are also offered. An internal coolant supply is also featured in the bar design, for optimal tool life, chip evacuation and thread quality.
"The oil and gas industry requires highly secure, predictable machining processes for accurate threads in demanding materials such as chrome-moly steels, stainless and nickel alloys. Our new oil and gas thread milling program exceeds these requirements with high feed rates, innovative features and more cutting edges for today's complex parts such as blowout preventers, valves, frack pumps and more," said Mark Hatch, Emuge Corp. Product Director, Taps and Thread Mills.
Related Glossary Terms
- alloys
alloys
Substances having metallic properties and being composed of two or more chemical elements of which at least one is a metal.
- computer numerical control ( CNC)
computer numerical control ( CNC)
Microprocessor-based controller dedicated to a machine tool that permits the creation or modification of parts. Programmed numerical control activates the machine’s servos and spindle drives and controls the various machining operations. See DNC, direct numerical control; NC, numerical control.
- coolant
coolant
Fluid that reduces temperature buildup at the tool/workpiece interface during machining. Normally takes the form of a liquid such as soluble or chemical mixtures (semisynthetic, synthetic) but can be pressurized air or other gas. Because of water’s ability to absorb great quantities of heat, it is widely used as a coolant and vehicle for various cutting compounds, with the water-to-compound ratio varying with the machining task. See cutting fluid; semisynthetic cutting fluid; soluble-oil cutting fluid; synthetic cutting fluid.
- feed
feed
Rate of change of position of the tool as a whole, relative to the workpiece while cutting.
- gang cutting ( milling)
gang cutting ( milling)
Machining with several cutters mounted on a single arbor, generally for simultaneous cutting.
- milling
milling
Machining operation in which metal or other material is removed by applying power to a rotating cutter. In vertical milling, the cutting tool is mounted vertically on the spindle. In horizontal milling, the cutting tool is mounted horizontally, either directly on the spindle or on an arbor. Horizontal milling is further broken down into conventional milling, where the cutter rotates opposite the direction of feed, or “up” into the workpiece; and climb milling, where the cutter rotates in the direction of feed, or “down” into the workpiece. Milling operations include plane or surface milling, endmilling, facemilling, angle milling, form milling and profiling.
- milling machine ( mill)
milling machine ( mill)
Runs endmills and arbor-mounted milling cutters. Features include a head with a spindle that drives the cutters; a column, knee and table that provide motion in the three Cartesian axes; and a base that supports the components and houses the cutting-fluid pump and reservoir. The work is mounted on the table and fed into the rotating cutter or endmill to accomplish the milling steps; vertical milling machines also feed endmills into the work by means of a spindle-mounted quill. Models range from small manual machines to big bed-type and duplex mills. All take one of three basic forms: vertical, horizontal or convertible horizontal/vertical. Vertical machines may be knee-type (the table is mounted on a knee that can be elevated) or bed-type (the table is securely supported and only moves horizontally). In general, horizontal machines are bigger and more powerful, while vertical machines are lighter but more versatile and easier to set up and operate.
- rake
rake
Angle of inclination between the face of the cutting tool and the workpiece. If the face of the tool lies in a plane through the axis of the workpiece, the tool is said to have a neutral, or zero, rake. If the inclination of the tool face makes the cutting edge more acute than when the rake angle is zero, the rake is positive. If the inclination of the tool face makes the cutting edge less acute or more blunt than when the rake angle is zero, the rake is negative.
- relief
relief
Space provided behind the cutting edges to prevent rubbing. Sometimes called primary relief. Secondary relief provides additional space behind primary relief. Relief on end teeth is axial relief; relief on side teeth is peripheral relief.
- shank
shank
Main body of a tool; the portion of a drill or similar end-held tool that fits into a collet, chuck or similar mounting device.