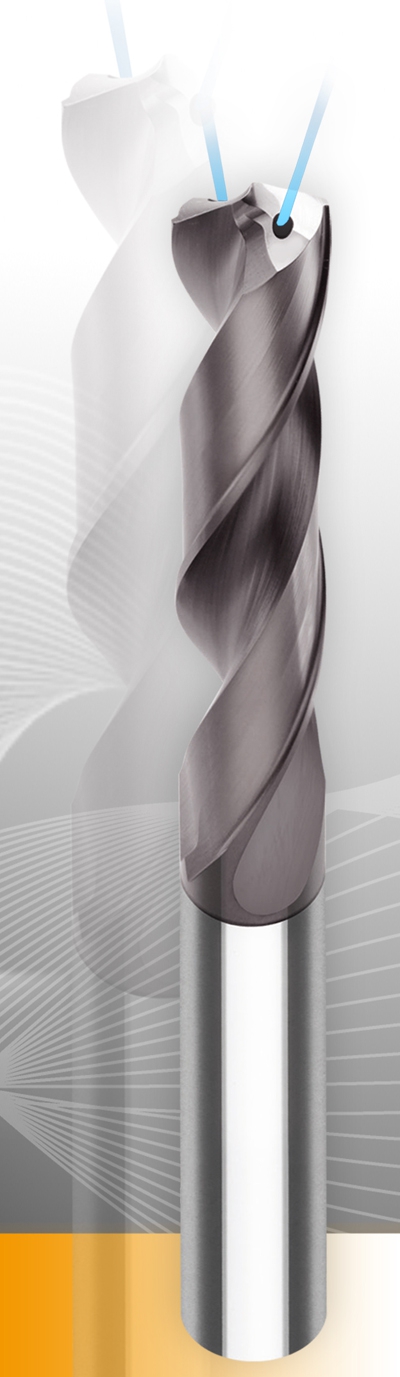
If you want to drill stainless steel, titanium and alloy steels quickly and cost-effectively, you will rapidly reach the limits of conventional tools. What is required is a high-performance, resilient sprinter such as the SPEEDMAX from Inovatools, according to the company. The tool manufacturer offers just such a powerful package in the form of the SC twist drill. Thanks to cutting edge preparation and the special tool design in terms of geometry, chip control and high-performance coating, it can be operated at much higher feed rates for a significantly longer service life than conventional tools.
Hardness, excellent mechanical and thermal durability and good corrosion and erosion resistance make stainless steel and its alloys, as well as low-density hard titanium, materials with outstanding functional characteristics. Consequently, these materials are used for industrial component manufacture in many areas.
"However, drilling into tough stainless steel, for example, places certain demands on the tools used," says Jochen Eckerle, Head of Production at Inovatools. "If geometry, chip control, coating and cooling are not optimally aligned to the respective application and/or material, cost-effectiveness and quality can quickly fall by the wayside. With our SPEEDMAX HA, HB, and HE shanks with h6 shank tolerance, manufacturers can now be on the safe side."
Maximum cutting capacity due to high feed rates with better quality and service life than standard tools was the focus for development of the SPEEDMAX. One crucial element of the improved performance of the SPEEDMAX is the interplay of various special design features. As a substrate, Inovatools uses selected, tough micro-grain carbide and chamfers the cutting edges after cutting. This special preparation eliminates any tiny nicks and anomalies at µm scale. This makes the cutting edges more stable and hence more resistant to premature wear due to edge breakouts and micro-cracks.
The lifting frontal polished section and the six-surface point thinning, for example, also boost performance. This means that SPEEDMAX not only has outstanding self-centering capabilities but also generates the optimal chip shape required for the high level of cutting data. A special groove chip space with extremely flat surfaces helps to remove chips from the contact zone quickly. This controlled-speed chip removal is aided by the precise internal cooling. Depending on the application, SPEEDMAX is equipped with a high-performance coating that also has a positive impact on wear behavior and service life.
As Jochen Eckerle explains, "Thanks to its special design, SPEEDMAX ensures that the tool runs smoothly even at greater drilling depths. That means that with SPEEDMAX, users can really move up a gear. It is possible to operate at higher feed rates than with conventional SC drills, yet with lower axial force and minimal cutting pressure."
One example is drilling in non-rusting, austenitic steel, 1.4301, X5CrNI18-10, cutting depth 45mm, drill diameter 9.5mm. In contrast to a standard stainless-steel drill, which reaches its limits at a maximum cutting speed of vc = 50 m/min, a feed rate of vf = 251mm and a feed rate per revolution of f = 0.15mm/rev, the SPEEDMAX achieves vc = 90 m/min, vf = 753mm and f = 0.22mm/rev. "In addition to the increase in feed rate of approximately 200 percent, SPEEDMAX has a considerably longer service life and delivers better hole quality," comments Jochen Eckerle.
Contact Details
Related Glossary Terms
- Brinell hardness number ( HB)
Brinell hardness number ( HB)
Number related to the applied load (usually, 500 kgf and 3,000 kgf) and to the surface area of the permanent impression made by a 10mm ball indenter. The Brinell hardness number is a calculated value of the applied load (kgf) divided by the surface area of the indentation (mm2). Therefore, the unit of measure of a Brinell hardness number is kgf/mm2, but it is always omitted.
- alloy steels
alloy steels
Steel containing specified quantities of alloying elements (other than carbon and the commonly accepted amounts of manganese, sulfur and phosphorus) added to cause changes in the metal’s mechanical and/or physical properties. Principal alloying elements are nickel, chromium, molybdenum and silicon. Some grades of alloy steels contain one or more of these elements: vanadium, boron, lead and copper.
- alloys
alloys
Substances having metallic properties and being composed of two or more chemical elements of which at least one is a metal.
- axial force
axial force
When drilling, a force that is directed axially—along the direction of machining. The magnitude of an axial force rises with the drill’s diameter and the chisel edge’s width. Axial force is also known as thrust. When turning and boring, the term “feed force” is commonly used instead of “axial force.” See cutting force.
- cutting speed
cutting speed
Tangential velocity on the surface of the tool or workpiece at the cutting interface. The formula for cutting speed (sfm) is tool diameter 5 0.26 5 spindle speed (rpm). The formula for feed per tooth (fpt) is table feed (ipm)/number of flutes/spindle speed (rpm). The formula for spindle speed (rpm) is cutting speed (sfm) 5 3.82/tool diameter. The formula for table feed (ipm) is feed per tooth (ftp) 5 number of tool flutes 5 spindle speed (rpm).
- edge preparation
edge preparation
Conditioning of the cutting edge, such as a honing or chamfering, to make it stronger and less susceptible to chipping. A chamfer is a bevel on the tool’s cutting edge; the angle is measured from the cutting face downward and generally varies from 25° to 45°. Honing is the process of rounding or blunting the cutting edge with abrasives, either manually or mechanically.
- feed
feed
Rate of change of position of the tool as a whole, relative to the workpiece while cutting.
- flat ( screw flat)
flat ( screw flat)
Flat surface machined into the shank of a cutting tool for enhanced holding of the tool.
- hardness
hardness
Hardness is a measure of the resistance of a material to surface indentation or abrasion. There is no absolute scale for hardness. In order to express hardness quantitatively, each type of test has its own scale, which defines hardness. Indentation hardness obtained through static methods is measured by Brinell, Rockwell, Vickers and Knoop tests. Hardness without indentation is measured by a dynamic method, known as the Scleroscope test.
- shank
shank
Main body of a tool; the portion of a drill or similar end-held tool that fits into a collet, chuck or similar mounting device.
- tolerance
tolerance
Minimum and maximum amount a workpiece dimension is allowed to vary from a set standard and still be acceptable.
- twist drill
twist drill
Most common type of drill, having two or more cutting edges, and having helical grooves adjacent thereto for the passage of chips and for admitting coolant to the cutting edges. Twist drills are used either for originating holes or for enlarging existing holes. Standard twist drills come in fractional sizes from 1¼16" to 11¼2", wire-gage sizes from 1 to 80, letter sizes A to Z and metric sizes.