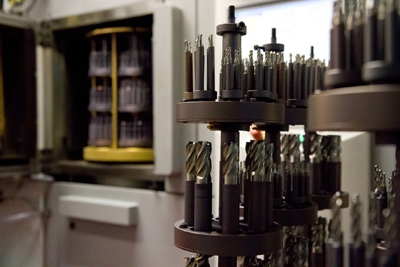
Optimized production conditions are an important factor for manufacturing cutting tools that are intended to meet not only the current challenges in metal processing, but also future ones as well. Tool manufacturer InovaTools from Kinding-Haunstetten, Germany, has reacted. The Bavaria-based company has invested around € 15 million to expand its production capacities and bring its grinding technology up to the latest technology standards. This is paying dividends. One example of this is the Starmax series for HPC end milling of steel materials. Following modifications to the design, the 3rd generation – the Starmax 3G – is now even more productive.
HPC end milling of steel materials is not for the faint-hearted, as the tools used must achieve high chip removal rates across large engagement widths and depths within a very short time. Despite the moderate cutting speeds, the cutting edge is subjected to enormous cutting forces and suddenly changing loads. The high levels of heat and huge chip volumes that have to be removed quickly and safely from the engagement zone also make life difficult for the tool.
With the VHM-HPC universal end mill concept Starmax (diameter: 3-25mm), tool manufacturer InovaTools from Kinding-Haunstetten has recently made the HPC end milling of steel materials – contour milling, angular infeed milling and pocket milling – quick and cost-effective. Jochen Eckerle, Head of Production at InovaTools: "Thanks to the numerous design advantages, our VHM-HPC Starmax end mills have been the leader of the pack in terms of service life, cutting volume and productivity for many years now compared to similar tools on the market. We have now upped our performance again. Because thanks to our investments in state-of-the-art production technologies as well as development capacities and manpower, we can offer a quick and targeted response to market requirements. The result is the latest-generation Starmax 3G end mill, which now offers even better performance."
InovaTools invests considerably in development and has a dedicated technology center for this purpose at its headquarters in Kinding-Haunstetten. Not only does this offer quick access to combined areas of expertise, it also shortens paths and development times. These advantages also bore fruit in the optimization of the current Starmax end mill, where the tool specialists have increased the core diameter. In addition, there are now four cutting edges with an unequal spiral pitch as well as a defined support chamfer for an even softer cut with even fewer vibrations than before. During the development, particular attention was paid to optimal chip control and removal. This is ensured by a special groove profile with extremely smooth chip grooves in a 40° spiral angle.
Jochen Eckerle: "Ultra-modern technology is required so that our Production department can implement the specifications of our Development department in the best possible way." To achieve this, InovaTools made high investments in new, ultra-modern technology for circular and tool grinding. This was complemented by new, innovative KSS ultra-fine filtration systems as well as progressive testing and measurement technology. Jochen Eckerle: "Once a tool has been well ground and pre-treated, it is completed with a first-class coating. It is therefore only logical that we, as an exacting tool manufacturer, guarantee this end quality ourselves, placing particular emphasis on our own areas of expertise and competence in the process." In keeping with this, the tools from InovaTools receive their high-performance coatings in the dedicated coating center using processes, including nano-composite coating.
This top class standard in coating technology is also used on the new Starmax 3G. Manufactured under temperature-stabilized conditions and using the very latest grinding machines, the special VAROCON smooth coating and the additional end finishing also help to promote the rapid removal of the very high chip volumes during HPC end milling. The high-performance coating also ensures a long service life for the tool.
The new Starmax 3G end mills are available as VHM tools in a short and long version and also as a long shank version with a release. The shank designs are based on DIN 6535 HA/HB, and there is also a special shank design to ensure additional hold. All tools can be used in dry as well as wet machining.
In practical applications, the new generation of the VHM-HPC Starmax 3G end mill really shows off its strengths over its competitors. An example of this can be seen in the manufacturing of a component for machine construction. During full grooving in the hardened and tempered tool steel 1.2312 (tool design z = 4 / Ø 12mm; ap = 12mm; ae 12mm; fz = 0.06mm), the Starmax 3G was operated (compared to the reference tool) with vc = 130 m/min instead of vc = 100 m/min and a feed of vf = 827mm/min compared to vf = 636mm/min. In the special application, the machining volume (Q) was 120 cm3/min, which is much higher than that of the reference tool (91.7 cm3/min). Jochen Eckerle: "With the Starmax 3G, feed motions up to 1.5×d can be achieved reliably, even during HPC end milling, and even during full grooving. The tools have such a precise concentricity that roughing and finishing is possible with the same end mill. The bottom line is that the new generation of Starmax 3G offers a potential increase in productivity of up to 30 percent in different applications."
Contact Details
Related Glossary Terms
- feed
feed
Rate of change of position of the tool as a whole, relative to the workpiece while cutting.
- gang cutting ( milling)
gang cutting ( milling)
Machining with several cutters mounted on a single arbor, generally for simultaneous cutting.
- grinding
grinding
Machining operation in which material is removed from the workpiece by a powered abrasive wheel, stone, belt, paste, sheet, compound, slurry, etc. Takes various forms: surface grinding (creates flat and/or squared surfaces); cylindrical grinding (for external cylindrical and tapered shapes, fillets, undercuts, etc.); centerless grinding; chamfering; thread and form grinding; tool and cutter grinding; offhand grinding; lapping and polishing (grinding with extremely fine grits to create ultrasmooth surfaces); honing; and disc grinding.
- grooving
grooving
Machining grooves and shallow channels. Example: grooving ball-bearing raceways. Typically performed by tools that are capable of light cuts at high feed rates. Imparts high-quality finish.
- milling
milling
Machining operation in which metal or other material is removed by applying power to a rotating cutter. In vertical milling, the cutting tool is mounted vertically on the spindle. In horizontal milling, the cutting tool is mounted horizontally, either directly on the spindle or on an arbor. Horizontal milling is further broken down into conventional milling, where the cutter rotates opposite the direction of feed, or “up” into the workpiece; and climb milling, where the cutter rotates in the direction of feed, or “down” into the workpiece. Milling operations include plane or surface milling, endmilling, facemilling, angle milling, form milling and profiling.
- milling machine ( mill)
milling machine ( mill)
Runs endmills and arbor-mounted milling cutters. Features include a head with a spindle that drives the cutters; a column, knee and table that provide motion in the three Cartesian axes; and a base that supports the components and houses the cutting-fluid pump and reservoir. The work is mounted on the table and fed into the rotating cutter or endmill to accomplish the milling steps; vertical milling machines also feed endmills into the work by means of a spindle-mounted quill. Models range from small manual machines to big bed-type and duplex mills. All take one of three basic forms: vertical, horizontal or convertible horizontal/vertical. Vertical machines may be knee-type (the table is mounted on a knee that can be elevated) or bed-type (the table is securely supported and only moves horizontally). In general, horizontal machines are bigger and more powerful, while vertical machines are lighter but more versatile and easier to set up and operate.
- pitch
pitch
1. On a saw blade, the number of teeth per inch. 2. In threading, the number of threads per inch.
- shank
shank
Main body of a tool; the portion of a drill or similar end-held tool that fits into a collet, chuck or similar mounting device.