Contact Details
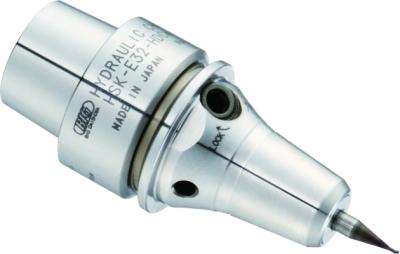
BIG KAISER announces the introduction of the world’s reportedly smallest hydraulic chuck for HSK-E25 machine spindles, thus completing its extensive range of BIG KAISER Super Slim hydraulic chucks. The Super Slim type of hydraulic chucks (HDC) are suitable toolholders for precision finishing processes in confined areas with drills, reamers, ball mills, endmills, diamond reamers and grinding tools. Cutting tools with shank diameters of 3mm or 4mm can be clamped directly and are suitable for high-speed micromachining applications in the automotive, aerospace, medical, die and electronics industries.
BIG KAISER designed the Super Slim HDC to require only a single wrench for clamping and unclamping. These chucks can clamp ultrasmall endmills and drills directly, without needing a reduction sleeve. The external body diameter of the chuck nose is a mere 0.551" (14mm), and a gauge length of 1.575” (40 mm) making it compact and precise. Each tool is precision balanced for speeds up to 60,000rpm and runout accuracy of less than 3 microns (.00012”) at 5xd.
“Our HSK-E25 tool holder lineup now includes BIG KAISER’s high precision, low runout, hydraulic chucks,” says Jack Burley, vice president of sales and engineering at BIG KAISER. “These ultraprecise hydraulic chucks, with their extremely slim design, are perfectly suited for high-precision finish milling work on ultrahigh speed spindles on machines with small work envelopes.”
The Super Slim HDCs for HSK-E25 machine spindles are available from stock; they are also available for the HSK-E 32 and HSK-E 40 spindle types.
Related Glossary Terms
- chuck
chuck
Workholding device that affixes to a mill, lathe or drill-press spindle. It holds a tool or workpiece by one end, allowing it to be rotated. May also be fitted to the machine table to hold a workpiece. Two or more adjustable jaws actually hold the tool or part. May be actuated manually, pneumatically, hydraulically or electrically. See collet.
- gang cutting ( milling)
gang cutting ( milling)
Machining with several cutters mounted on a single arbor, generally for simultaneous cutting.
- grinding
grinding
Machining operation in which material is removed from the workpiece by a powered abrasive wheel, stone, belt, paste, sheet, compound, slurry, etc. Takes various forms: surface grinding (creates flat and/or squared surfaces); cylindrical grinding (for external cylindrical and tapered shapes, fillets, undercuts, etc.); centerless grinding; chamfering; thread and form grinding; tool and cutter grinding; offhand grinding; lapping and polishing (grinding with extremely fine grits to create ultrasmooth surfaces); honing; and disc grinding.
- milling
milling
Machining operation in which metal or other material is removed by applying power to a rotating cutter. In vertical milling, the cutting tool is mounted vertically on the spindle. In horizontal milling, the cutting tool is mounted horizontally, either directly on the spindle or on an arbor. Horizontal milling is further broken down into conventional milling, where the cutter rotates opposite the direction of feed, or “up” into the workpiece; and climb milling, where the cutter rotates in the direction of feed, or “down” into the workpiece. Milling operations include plane or surface milling, endmilling, facemilling, angle milling, form milling and profiling.
- shank
shank
Main body of a tool; the portion of a drill or similar end-held tool that fits into a collet, chuck or similar mounting device.