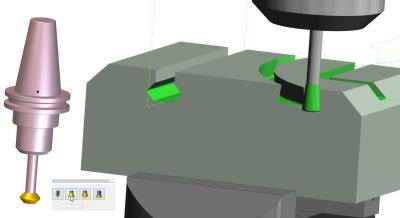
The introduction of a specific 5-axis ‘Tilt’ control strategy, combined with a ‘Barrel Cutter,’ is said to be the most significant enhancement in the latest release of SURFCAM, from Hexagon Manufacturing Intelligence’s Production Software division.
Brand Manager John Buehler says barrel cutters are recognized as one of the fastest tools when 5-axis machining, and are now fully supported in the SURFCAM Toolstore.
As well as the new ‘side tilt by contact point’ capability, the Advanced 5-axis cycle also offers further gouge checking in the Swarf command, along with extra control in all strategies.
A number of new and enhanced features in SURFCAM 2020.0 provide increased productivity for both milling and turning users. And the recently introduced SURFCAM Inspect module includes 13 upgrades.
Mindful of the need to generate quick toolpaths to reduce production costs, SURFCAM 2020.0 offers a significant performance boost when either roughing or profiling a solid model. “Essentially, the machining engine will only compute data constrained within the boundary, ignoring the rest of the model. This significantly decreases the cache size while generating faster toolpaths.”
Formerly introduced in the Hole cycle in the 2018 R1 release, the ‘Deep Hole” strategy has been enhanced, justifying the creation of its own individual cycle. The original modifiers have been improved and further control tabs have been added to the cycle, giving greater control over the toolpath.
The Turning environment offers a new machining cycle – Thread Profiling. “Reacting to a high frequency of enhancement requests from customers in this area, SURFCAM 2020.0 allows users to effortlessly machine complex form threads such as VAM and Acme,” Buehler says. “The cycle provides both roughing and finishing strategies, allowing users to specify their own thread forms.”
The ever-popular Waveform Machining Strategy has been enhanced with ‘Chip Prevention’ control. Under certain conditions, a toolpath can generate a thin island of material (chip), which, as it gets thinner can cause machining stresses, and potentially break the tool.
“We’ve found that to compensate for this risk, users tend to sacrifice productivity by reducing feeds and speeds. So, we’ve introduced the ‘Chip Prevention’ option, which alters the toolpath pattern by machining across the island of material, removing the possibility of machining stresses, allowing users to maintain optimum feeds and speeds.”
Supporting the growing number of machine tools possessing an ‘Auxiliary Z’ (Quill), SURFCAM 2020.0 introduces a Code Wizard enhancement, letting users add a secondary working spindle. This supports multi-task machines, along with any combination of Table/Head Milling machines. Coupled with that, a new ‘Quill Command’ (Move menu), offers greater control when commanding the second working axis.
When using the Finish Grooving cycle, users can now control the ‘Break Edge’ angle. In previous SURFCAM releases, the break angle was set at 45-degrees.
In the Finish Turning cycle, a ‘stand-off’ value can now be defined when using ‘Up Cut’ control.
An XY Offset can be set when deploying the Hole Cycle’s ‘Helical’ strategy, allowing users to control both surface finish and tool wear. “It also leads to reduced CAD preparation time, while guaranteeing that the cycle is associative to the solid model.”
Two new tool types – Dovetail, and Double Angle – have been added to the Toolstore. This does away with the need to create custom graphics for them, saving time and programming costs. And the tools work automatically with the Slot Cycle.
Moving on to SURFCAM Inspect, Brand Manager for Research and Development Andy Mears says developers have responded to numerous customer requests by expanding the ability of Inspect components in both the turning and mill-turn environments.
The overall interface has been upgraded to adopt the work-flow ribbon toolbar, improving interactivity. The ‘Probing Options’ menu has been split into two separate dialogs, meaning users can concentrate on Output and Inspect preferences individually.
Safe Retract controls have been added to the inspection cycles for users to state multiple positions while controlling the probe’s movement. The ‘Index’ command now contains the ability for further positional manipulation, where an alternative angle may now be specified in order to view the components on the machine tool.
The new ‘Angle To Line’ feature merges three previous commands into one function, allowing the Angle Direction to be specified in the Data Report.
Amongst other enhancements to the SURFCAM Inspect module: Constructed features have been updated, so that ‘Straightness’ can now be specified while editing the ‘Constructed Line’ feature. And both the Circular and Arc features can now be converted and re-specified when edited.
Finally, around 50 enhancements have been made to the optional SURFCAM Designer module, which bridges the gap between CAD and CAM, focusing on the specific needs of machinist programmers.
Contact Details
Related Glossary Terms
- computer-aided design ( CAD)
computer-aided design ( CAD)
Product-design functions performed with the help of computers and special software.
- computer-aided manufacturing ( CAM)
computer-aided manufacturing ( CAM)
Use of computers to control machining and manufacturing processes.
- gang cutting ( milling)
gang cutting ( milling)
Machining with several cutters mounted on a single arbor, generally for simultaneous cutting.
- grooving
grooving
Machining grooves and shallow channels. Example: grooving ball-bearing raceways. Typically performed by tools that are capable of light cuts at high feed rates. Imparts high-quality finish.
- milling
milling
Machining operation in which metal or other material is removed by applying power to a rotating cutter. In vertical milling, the cutting tool is mounted vertically on the spindle. In horizontal milling, the cutting tool is mounted horizontally, either directly on the spindle or on an arbor. Horizontal milling is further broken down into conventional milling, where the cutter rotates opposite the direction of feed, or “up” into the workpiece; and climb milling, where the cutter rotates in the direction of feed, or “down” into the workpiece. Milling operations include plane or surface milling, endmilling, facemilling, angle milling, form milling and profiling.
- profiling
profiling
Machining vertical edges of workpieces having irregular contours; normally performed with an endmill in a vertical spindle on a milling machine or with a profiler, following a pattern. See mill, milling machine.
- solid model
solid model
3-D model created using “building blocks.” This is the most accurate way of representing real-world objects in CAD.
- swarf
swarf
Metal fines and grinding wheel particles generated during grinding.
- toolpath( cutter path)
toolpath( cutter path)
2-D or 3-D path generated by program code or a CAM system and followed by tool when machining a part.
- turning
turning
Workpiece is held in a chuck, mounted on a face plate or secured between centers and rotated while a cutting tool, normally a single-point tool, is fed into it along its periphery or across its end or face. Takes the form of straight turning (cutting along the periphery of the workpiece); taper turning (creating a taper); step turning (turning different-size diameters on the same work); chamfering (beveling an edge or shoulder); facing (cutting on an end); turning threads (usually external but can be internal); roughing (high-volume metal removal); and finishing (final light cuts). Performed on lathes, turning centers, chucking machines, automatic screw machines and similar machines.