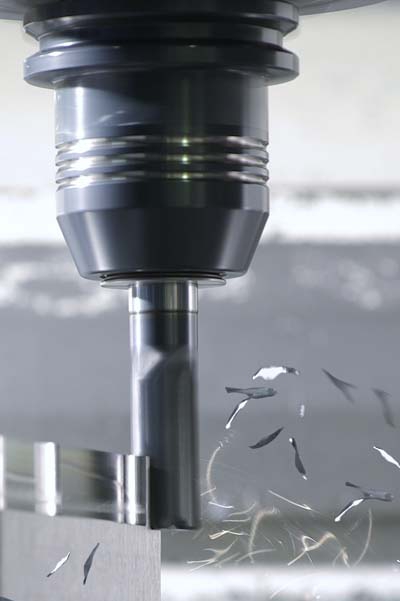
With the TENDO E compact, SCHUNK has reportedly started a new era in tool clamping. With this advanced toolholder it is no longer required to use different holder technologies for milling, drilling, and reaming. Hydraulic expansion toolholders can safely transfer torques of up to 520 Nm (384 ft-lbs) at a 20mm clamping diameter and are perfectly suited for high volume cutting. With excellent vibration damping and precise run out accuracy of less than 0.003mm (0.0001") at 2,5 x D, this innovative holder protects the machine spindle and the cutting tool from damage. The attractively-priced hydraulic expansion toolholder works well across the application range from rough milling to finish operations such as reaming and fine milling. Users who have previously used side lock holders can now breathe a sigh of relief: In roughing operations, tool cost reductions of up to 40 percent have been achieved with TENDO E compact. Tools can be quickly changed with an Allen key, making this powerful hydraulic expansion toolholder an excellent alternative for operations where the toolholder quantities do not justify peripheral equipment purchases. All common spindle connections are available for ¾" interfaces HSK-A63, SK40, BT40 and CAT40. For nearly all cutting tool shank diameters, other versions are scheduled for future release.
Contact Details
Related Glossary Terms
- gang cutting ( milling)
gang cutting ( milling)
Machining with several cutters mounted on a single arbor, generally for simultaneous cutting.
- milling
milling
Machining operation in which metal or other material is removed by applying power to a rotating cutter. In vertical milling, the cutting tool is mounted vertically on the spindle. In horizontal milling, the cutting tool is mounted horizontally, either directly on the spindle or on an arbor. Horizontal milling is further broken down into conventional milling, where the cutter rotates opposite the direction of feed, or “up” into the workpiece; and climb milling, where the cutter rotates in the direction of feed, or “down” into the workpiece. Milling operations include plane or surface milling, endmilling, facemilling, angle milling, form milling and profiling.
- shank
shank
Main body of a tool; the portion of a drill or similar end-held tool that fits into a collet, chuck or similar mounting device.
- toolholder
toolholder
Secures a cutting tool during a machining operation. Basic types include block, cartridge, chuck, collet, fixed, modular, quick-change and rotating.