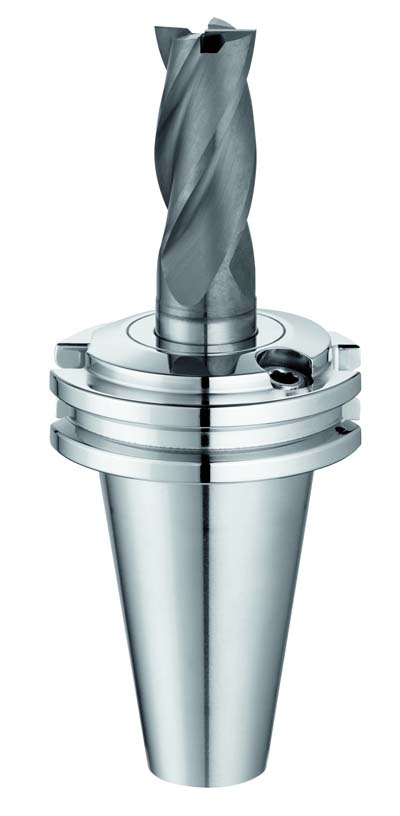
SCHUNK Inc.'s TENDO-ES is a short hydraulic expansion toolholder, which allows the tool to be clamped directly in the mounting taper. This way, the tool shank is supported via the spindle. The result is high holding forces for transferable high torques and a great deal of additional space in the machining area. The TENDOS-ES L1 is 26.0mm, has a runout accuracy of less than 0.003mm, and tools can be changed in seconds with an Allen key. TENDO-ES is reportedly for rough machining, HPC/HSC, drilling, reaming, tapping, thread milling, and thread forming. Flexibility is ensured due to the use of intermediate sleeves. The TENDO-ES is now available for the SK 40 and CAT 40 interfaces. The clamping diameter is 20mm, or ¾ inches, and standard TENDO sleeves can be used to clamp smaller tool shank diameters with a balancing grade of G 2.5 at 25,000 rpm.
Contact Details
Related Glossary Terms
- gang cutting ( milling)
gang cutting ( milling)
Machining with several cutters mounted on a single arbor, generally for simultaneous cutting.
- milling
milling
Machining operation in which metal or other material is removed by applying power to a rotating cutter. In vertical milling, the cutting tool is mounted vertically on the spindle. In horizontal milling, the cutting tool is mounted horizontally, either directly on the spindle or on an arbor. Horizontal milling is further broken down into conventional milling, where the cutter rotates opposite the direction of feed, or “up” into the workpiece; and climb milling, where the cutter rotates in the direction of feed, or “down” into the workpiece. Milling operations include plane or surface milling, endmilling, facemilling, angle milling, form milling and profiling.
- shank
shank
Main body of a tool; the portion of a drill or similar end-held tool that fits into a collet, chuck or similar mounting device.
- tapping
tapping
Machining operation in which a tap, with teeth on its periphery, cuts internal threads in a predrilled hole having a smaller diameter than the tap diameter. Threads are formed by a combined rotary and axial-relative motion between tap and workpiece. See tap.
- toolholder
toolholder
Secures a cutting tool during a machining operation. Basic types include block, cartridge, chuck, collet, fixed, modular, quick-change and rotating.