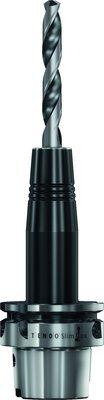
With the SCHUNK TENDO Slim 4ax hydraulic expansion toolholder, it is possible to combine the complete outside geometry of heat shrinking mountings with SCHUNK hydraulic expansion technology. The slim mounting makes it suitable for use in series production, particularly in the automotive industry.
It was designed for axial operations, and shows its strength during milling close to interfering contours, countersinking, and reaming in 5-axis centers and the die and mold industry. Test series prove that the mountings with the vibration-damping properties of the hydraulic expansion technology have considerably improved the process during milling operations.
The hydraulic expansion toolholder design reduces peak cutting amplitude of the force progression in Y-direction, which results in less deflection of the tool. By reducing the load of the cross cutter and the cutting edge, considerably longer service life can be achieved. Additionally, the user benefits from having DIN 69822-8 dimension features for maximum precision at the workpiece. The MQL-capable mounting is dirt-resistant and low-maintenance. In contrast to the shrink-fit toolholders, it has a permanently high runout accuracy of less than 0.003 mm at an unclamped length of 2.5 x D and a balance grade of G 2.5 at 25,000 rpm. Mountings are available for the interfaces HSK-A63 with diameters from 10 mm to 20 mm.
Contact Details
Related Glossary Terms
- centers
centers
Cone-shaped pins that support a workpiece by one or two ends during machining. The centers fit into holes drilled in the workpiece ends. Centers that turn with the workpiece are called “live” centers; those that do not are called “dead” centers.
- countersinking
countersinking
Cutting a beveled edge at the entrance of a hole so a screw head sits flush with the workpiece surface.
- gang cutting ( milling)
gang cutting ( milling)
Machining with several cutters mounted on a single arbor, generally for simultaneous cutting.
- milling
milling
Machining operation in which metal or other material is removed by applying power to a rotating cutter. In vertical milling, the cutting tool is mounted vertically on the spindle. In horizontal milling, the cutting tool is mounted horizontally, either directly on the spindle or on an arbor. Horizontal milling is further broken down into conventional milling, where the cutter rotates opposite the direction of feed, or “up” into the workpiece; and climb milling, where the cutter rotates in the direction of feed, or “down” into the workpiece. Milling operations include plane or surface milling, endmilling, facemilling, angle milling, form milling and profiling.
- toolholder
toolholder
Secures a cutting tool during a machining operation. Basic types include block, cartridge, chuck, collet, fixed, modular, quick-change and rotating.