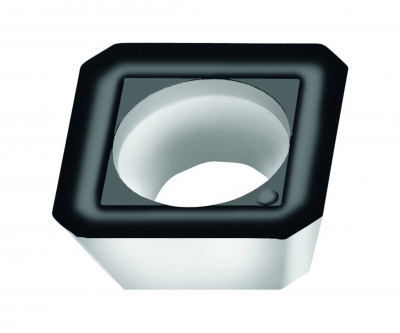
Walter has introduced the Tiger·tec Silver grade WSM45X, creating an indexable inserts with high-temperature resistance, improved wear resistance, outstanding toughness, and exceptional hardness. These key features of inserts in the new Tiger·tec Silver grade WSM45X can boost performance by up to 67 percent over comparable tools, according to the company. The special Tiger·tec Silver surface treatment coupled with Walter’s high-performance substrate ensure maximum process reliability when working with materials that have difficult cutting properties, such as titanium alloys.
The new grade’s unique coating enables users to increase their machining productivity, especially when using materials that are difficult to cut. The surfaces are also extremely smooth, which significantly reduce edge build up. In addition, the two-tone Tiger·tec Silver coating allows users to identify wear quickly and thus make sure that all cutting edges are used efficiently.
The indexable inserts in the Tiger·tec Silver grade WSM45X are available for all popular Xtra·tec and new M4000 face and shoulder mills, and the Walter F2334 copy milling cutter. WSM45X is suited to machining stainless steels (ISO M) and difficult-to-cut materials (ISO S). Typical components include exhaust-gas turbochargers, turbine blades and titanium frames for use in the aerospace industry.
Contact Details
Related Glossary Terms
- alloys
alloys
Substances having metallic properties and being composed of two or more chemical elements of which at least one is a metal.
- gang cutting ( milling)
gang cutting ( milling)
Machining with several cutters mounted on a single arbor, generally for simultaneous cutting.
- hardness
hardness
Hardness is a measure of the resistance of a material to surface indentation or abrasion. There is no absolute scale for hardness. In order to express hardness quantitatively, each type of test has its own scale, which defines hardness. Indentation hardness obtained through static methods is measured by Brinell, Rockwell, Vickers and Knoop tests. Hardness without indentation is measured by a dynamic method, known as the Scleroscope test.
- milling
milling
Machining operation in which metal or other material is removed by applying power to a rotating cutter. In vertical milling, the cutting tool is mounted vertically on the spindle. In horizontal milling, the cutting tool is mounted horizontally, either directly on the spindle or on an arbor. Horizontal milling is further broken down into conventional milling, where the cutter rotates opposite the direction of feed, or “up” into the workpiece; and climb milling, where the cutter rotates in the direction of feed, or “down” into the workpiece. Milling operations include plane or surface milling, endmilling, facemilling, angle milling, form milling and profiling.
- milling cutter
milling cutter
Loosely, any milling tool. Horizontal cutters take the form of plain milling cutters, plain spiral-tooth cutters, helical cutters, side-milling cutters, staggered-tooth side-milling cutters, facemilling cutters, angular cutters, double-angle cutters, convex and concave form-milling cutters, straddle-sprocket cutters, spur-gear cutters, corner-rounding cutters and slitting saws. Vertical cutters use shank-mounted cutting tools, including endmills, T-slot cutters, Woodruff keyseat cutters and dovetail cutters; these may also be used on horizontal mills. See milling.
- stainless steels
stainless steels
Stainless steels possess high strength, heat resistance, excellent workability and erosion resistance. Four general classes have been developed to cover a range of mechanical and physical properties for particular applications. The four classes are: the austenitic types of the chromium-nickel-manganese 200 series and the chromium-nickel 300 series; the martensitic types of the chromium, hardenable 400 series; the chromium, nonhardenable 400-series ferritic types; and the precipitation-hardening type of chromium-nickel alloys with additional elements that are hardenable by solution treating and aging.
- wear resistance
wear resistance
Ability of the tool to withstand stresses that cause it to wear during cutting; an attribute linked to alloy composition, base material, thermal conditions, type of tooling and operation and other variables.