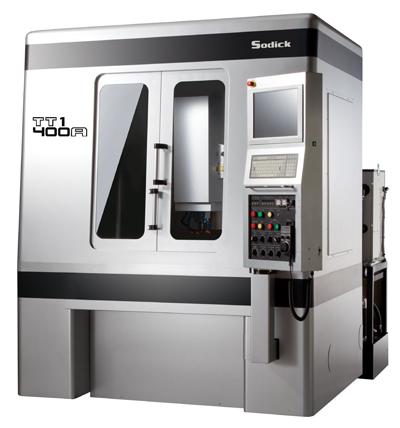
Sodick Inc. is expanding their product line with a new high speed electrode machining center, the TT1-400A. Designed and built in Japan, the TT1-400A is ideal for the milling of graphite and copper electrodes with extreme precision. Sodick developed the TT1-400A based on the advanced core technologies incorporated in the company's HS Series. The TT1-400A shares the same ultra precise motion control and linear motor drive platform that is utilized in the HS Series to reportedly achieve maximum speed and acceleration.
Sodick first introduced linear motor driven machines in 1999, replacing the ball screw technology. The TT1-400A benefits from the advantages of linear motor drives, including no ball screws, no backlash, no lost motion, increased cutting speed and no maintenance. The new LN3X controller, developed by Sodick America in San Jose, Calif., is designed to maximize the speed and acceleration of the Sodick linear motor drives, on the X, Y and Z axes and incorporates new features to simplify work setup.
The TT1-400A has an X, Y, Z travel of 15.75" x 9.84" x 11.81" (400 x 250 x 300mm), respectively. The maximum spindle RPM is 40,000 and the impressive maximum acceleration is 1.2G. Superior stability and the highest degree of precision, down to oneµm, are the top attributes of this new machine. Other standard features of the TT1-400A include Heidenhain Glass Scales, Blum Laser Tool Measurement, Integrated Torit Graphite Dust Collector, Air Purged Dust Protection, Oil Mist System with Mist Collector and an Integrated Part Probe. The Sodick TT1-400A heralds a new era in high precision electrode manufacturing.
Contact Details
Related Glossary Terms
- backlash
backlash
Reaction in dynamic motion systems where potential energy that was created while the object was in motion is released when the object stops. Release of this potential energy or inertia causes the device to quickly snap backward relative to the last direction of motion. Backlash can cause a system’s final resting position to be different from what was intended and from where the control system intended to stop the device.
- cutting speed
cutting speed
Tangential velocity on the surface of the tool or workpiece at the cutting interface. The formula for cutting speed (sfm) is tool diameter 5 0.26 5 spindle speed (rpm). The formula for feed per tooth (fpt) is table feed (ipm)/number of flutes/spindle speed (rpm). The formula for spindle speed (rpm) is cutting speed (sfm) 5 3.82/tool diameter. The formula for table feed (ipm) is feed per tooth (ftp) 5 number of tool flutes 5 spindle speed (rpm).
- gang cutting ( milling)
gang cutting ( milling)
Machining with several cutters mounted on a single arbor, generally for simultaneous cutting.
- linear motor
linear motor
Functionally the same as a rotary motor in a machine tool, a linear motor can be thought of as a standard permanent-magnet, rotary-style motor slit axially to the center and then peeled back and laid flat. The major advantage of using a linear motor to drive the axis motion is that it eliminates the inefficiency and mechanical variance caused by the ballscrew assembly system used in most CNC machines.
- machining center
machining center
CNC machine tool capable of drilling, reaming, tapping, milling and boring. Normally comes with an automatic toolchanger. See automatic toolchanger.
- milling
milling
Machining operation in which metal or other material is removed by applying power to a rotating cutter. In vertical milling, the cutting tool is mounted vertically on the spindle. In horizontal milling, the cutting tool is mounted horizontally, either directly on the spindle or on an arbor. Horizontal milling is further broken down into conventional milling, where the cutter rotates opposite the direction of feed, or “up” into the workpiece; and climb milling, where the cutter rotates in the direction of feed, or “down” into the workpiece. Milling operations include plane or surface milling, endmilling, facemilling, angle milling, form milling and profiling.