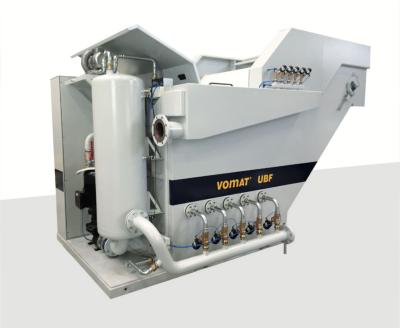
Talking ultrafine filtration of water-soluble, fully synthetic coolants, emulsions or oils contaminated by sludge or chips - the use of a suitable filter system in industrial metalworking, such as tool grinding, turning and milling, is an important parameter for success. This is because ultrafine filtration plays a key role in ensuring that the machining process produces high quality, is sustainable and economical, and keeps the wear on the installed coolant system components low. With the new UBF vacuum belt filter, filter manufacturer Vomat is presenting a high-performance system that filters grinding residues, of metals and nonferrous alloys, from a wide variety of lubricants and coolants.
Vomat systems are ideal for the filtration of ultrafine particles from oil and water-based coolants, such as those produced by grinding, turning, milling, drilling, honing, lapping, eroding and other machining processes. Vomat offers companies in the metalworking industry individually tailored concepts for the filtration of cooling lubricants in their machining processes, as well as special filtration solutions for a wide variety of materials based on their many years of experience.
With the UBF vacuum belt filter, Vomat is now expanding its product portfolio with a new high-performance filtration system. The Vomat UBF filters modern cooling lubricants and grinding oils to high purity standards combined with low operating costs and minimal space requirements, which is a great plus for the metal industry.
Mike Groh, sales manager at Vomat, said: "Our new UBF is truly versatile. It can be used for filtering various ferrous and nonferrous alloys, hard metals, disc abrasives, binders, etc. without the need of a special pre-separation system. Depending on the material to be filtered and the characteristics of the filter cake, the filter fineness is between 10 and 30 µm. If desired a fine filter system can be installed downstream to further increase the filter fineness.
Vomat offers the new vacuum belt filter in different volume flow capacities of 200 l/min to 2,000 l/min. During operation, a vacuum is generated and the system pumps suck the cooling lubricant to be cleaned through a high-performance filter belt and makes the cleaned medium continuously available to the process without interruption.
The disposal of machining sludge with low residual moisture is automatic via several filter belts. More over the UBF can efficiently filter larger chips, from turning or milling operations. The fully automatic belt cleaning system allows for user-friendly sludge disposal directly into transport containers provided by recycling companies. The integrated or external cooling system, can be cooled by means of a compressor or plant provided cold water. It has a control accuracy of +/-1.0 K and guarantees constant low fluid temperatures.
An important advantage is the low-maintenance concept Vomat technology offers. The UBF is designed in such a way that a company's own maintenance personnel can easily service the machines on site at set intervals. Thanks to an integrated remote control system, the UBF filtration system can be monitored via the Internet by Vomat. This means a reduction of possible system failures through early detection.
Groh stated, "If the worst comes to worst, Vomat employees can trouble shoot the machine immediately after the occurrence without delay. In real-time communication with Vomat staff in Germany, they are able to eliminate problems quickly."
The high technical standard with regard to operational reliability and energy efficiency is reflected among other things, in the use of frequency-controlled drives and pumps, as well as in design solutions for saving in energy-intensive processes such as vacuum generation. In addition, the UBF also scores with energy efficiency in cooling: Vomat equips the UBF with chilled water or compressor cooling systems which have a much better coefficient of performance than conventional cooling systems with switch-on and switch-off thermostatic controls.
Groh said: "The compact UBF unit is extremely easy to maintain thanks to well thought-out design features. Due to a special belt guide, the vacuum belt filter, which can be used in a variety of filtration scenarios, requires about 70 percent less space than other systems on the market, while providing 100 percent performance. In comparison to the competition we have three times the filtration performance per square meter of production area. This is a significant cost benefit in times of expensive production space"
Contact Details
Related Glossary Terms
- alloys
alloys
Substances having metallic properties and being composed of two or more chemical elements of which at least one is a metal.
- coolant
coolant
Fluid that reduces temperature buildup at the tool/workpiece interface during machining. Normally takes the form of a liquid such as soluble or chemical mixtures (semisynthetic, synthetic) but can be pressurized air or other gas. Because of water’s ability to absorb great quantities of heat, it is widely used as a coolant and vehicle for various cutting compounds, with the water-to-compound ratio varying with the machining task. See cutting fluid; semisynthetic cutting fluid; soluble-oil cutting fluid; synthetic cutting fluid.
- gang cutting ( milling)
gang cutting ( milling)
Machining with several cutters mounted on a single arbor, generally for simultaneous cutting.
- grinding
grinding
Machining operation in which material is removed from the workpiece by a powered abrasive wheel, stone, belt, paste, sheet, compound, slurry, etc. Takes various forms: surface grinding (creates flat and/or squared surfaces); cylindrical grinding (for external cylindrical and tapered shapes, fillets, undercuts, etc.); centerless grinding; chamfering; thread and form grinding; tool and cutter grinding; offhand grinding; lapping and polishing (grinding with extremely fine grits to create ultrasmooth surfaces); honing; and disc grinding.
- lapping
lapping
Finishing operation in which a loose, fine-grain abrasive in a liquid medium abrades material. Extremely accurate process that corrects minor shape imperfections, refines surface finishes and produces a close fit between mating surfaces.
- metalworking
metalworking
Any manufacturing process in which metal is processed or machined such that the workpiece is given a new shape. Broadly defined, the term includes processes such as design and layout, heat-treating, material handling and inspection.
- milling
milling
Machining operation in which metal or other material is removed by applying power to a rotating cutter. In vertical milling, the cutting tool is mounted vertically on the spindle. In horizontal milling, the cutting tool is mounted horizontally, either directly on the spindle or on an arbor. Horizontal milling is further broken down into conventional milling, where the cutter rotates opposite the direction of feed, or “up” into the workpiece; and climb milling, where the cutter rotates in the direction of feed, or “down” into the workpiece. Milling operations include plane or surface milling, endmilling, facemilling, angle milling, form milling and profiling.
- turning
turning
Workpiece is held in a chuck, mounted on a face plate or secured between centers and rotated while a cutting tool, normally a single-point tool, is fed into it along its periphery or across its end or face. Takes the form of straight turning (cutting along the periphery of the workpiece); taper turning (creating a taper); step turning (turning different-size diameters on the same work); chamfering (beveling an edge or shoulder); facing (cutting on an end); turning threads (usually external but can be internal); roughing (high-volume metal removal); and finishing (final light cuts). Performed on lathes, turning centers, chucking machines, automatic screw machines and similar machines.