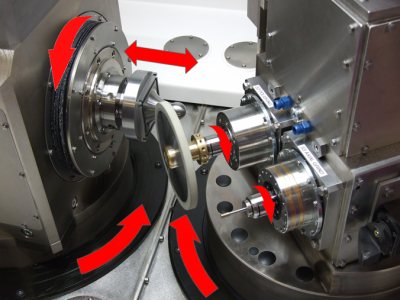
Fives’ Universal Landis Twin Turret grinding machine’s newly configured design provides a common platform for multiple machine configurations and processes. It is far stiffer than conventional machines, features remarkable thermal stability, and offers a compact machine footprint, according to the company.
Fives’ longtime grinding expertise, in conjunction with its history alongside the Landis and Cranfield Precision range of products, led to the development of the Universal Twin Turret grinder.
The Landis Twin Turret (LTT) series machines are designed for superabrasives, and perfectly suited to process extremely challenging materials and geometries common in various industries and markets such as aerospace, automotive, fuel systems as well as optics and precision components. This model provides a common platform for multiple machine configurations and processes, including OD, ID and profile grinding, milling, polishing, hard and diamond turning, dicing, and in-situ metrology. Supplied in two sizes, the LTT-100 and LTT-400 are multifunctional machines that handle workpieces as large as 100 mm and 400 mm in diameter, respectively.
The Universal Twin Turret grinder enables sub-micron position control. Two rotary axes are rigidly mounted on a fixed center distance and provide relative motion between the component and cutting tool, with the linear axis used to control the depth of cut and profile shape of the component being machined. Its unique combination of rotary and linear axes produce relative motion between tool and workpiece over a swept working area.
This machine concept is radically different, as it coordinates the two rotary axes and a short linear axis in a Twin Turret design to provide far stiffer results than standard machines, as well as remarkable thermal stability. Gone are the inherent thermal stability and stiffness issues that plague conventional machine platforms using stacked linear axes.
The twin turret design enables a simple non-contacting labyrinth seal, making the machine base almost immune to distortions. A far cry from traditional machine designs that suffer from the ever-changing coolant return path and heat transference from the grinding process, resulting in constant variable machine distortions.
The LTT was designed to use the minimum number of bearing interfaces in the machining loop, to maximize machine loop stiffness. Two highly damped hydrostatic bearings are employed and the machine’s turrets are bolted together via a solid granite base plate to resist machining forces and improve precision and repeatability.
The unique configuration of the LTT also provides a compact machine footprint that is typically 40 percent smaller than similar machines. This frees up more room on the job shop floor for other workpieces, additional work-flow margin, and/or space for inventory.
Related Glossary Terms
- coolant
coolant
Fluid that reduces temperature buildup at the tool/workpiece interface during machining. Normally takes the form of a liquid such as soluble or chemical mixtures (semisynthetic, synthetic) but can be pressurized air or other gas. Because of water’s ability to absorb great quantities of heat, it is widely used as a coolant and vehicle for various cutting compounds, with the water-to-compound ratio varying with the machining task. See cutting fluid; semisynthetic cutting fluid; soluble-oil cutting fluid; synthetic cutting fluid.
- depth of cut
depth of cut
Distance between the bottom of the cut and the uncut surface of the workpiece, measured in a direction at right angles to the machined surface of the workpiece.
- gang cutting ( milling)
gang cutting ( milling)
Machining with several cutters mounted on a single arbor, generally for simultaneous cutting.
- grinding
grinding
Machining operation in which material is removed from the workpiece by a powered abrasive wheel, stone, belt, paste, sheet, compound, slurry, etc. Takes various forms: surface grinding (creates flat and/or squared surfaces); cylindrical grinding (for external cylindrical and tapered shapes, fillets, undercuts, etc.); centerless grinding; chamfering; thread and form grinding; tool and cutter grinding; offhand grinding; lapping and polishing (grinding with extremely fine grits to create ultrasmooth surfaces); honing; and disc grinding.
- inner diameter ( ID)
inner diameter ( ID)
Dimension that defines the inside diameter of a cavity or hole. See OD, outer diameter.
- metrology
metrology
Science of measurement; the principles on which precision machining, quality control and inspection are based. See precision machining, measurement.
- milling
milling
Machining operation in which metal or other material is removed by applying power to a rotating cutter. In vertical milling, the cutting tool is mounted vertically on the spindle. In horizontal milling, the cutting tool is mounted horizontally, either directly on the spindle or on an arbor. Horizontal milling is further broken down into conventional milling, where the cutter rotates opposite the direction of feed, or “up” into the workpiece; and climb milling, where the cutter rotates in the direction of feed, or “down” into the workpiece. Milling operations include plane or surface milling, endmilling, facemilling, angle milling, form milling and profiling.
- outer diameter ( OD)
outer diameter ( OD)
Dimension that defines the exterior diameter of a cylindrical or round part. See ID, inner diameter.
- polishing
polishing
Abrasive process that improves surface finish and blends contours. Abrasive particles attached to a flexible backing abrade the workpiece.
- stiffness
stiffness
1. Ability of a material or part to resist elastic deflection. 2. The rate of stress with respect to strain; the greater the stress required to produce a given strain, the stiffer the material is said to be. See dynamic stiffness; static stiffness.
- turning
turning
Workpiece is held in a chuck, mounted on a face plate or secured between centers and rotated while a cutting tool, normally a single-point tool, is fed into it along its periphery or across its end or face. Takes the form of straight turning (cutting along the periphery of the workpiece); taper turning (creating a taper); step turning (turning different-size diameters on the same work); chamfering (beveling an edge or shoulder); facing (cutting on an end); turning threads (usually external but can be internal); roughing (high-volume metal removal); and finishing (final light cuts). Performed on lathes, turning centers, chucking machines, automatic screw machines and similar machines.