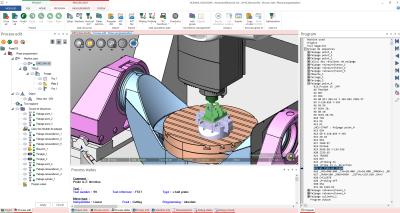
SPRING Technologies announces the latest version of its flagship NCSIMUL SOLUTIONS. The new version sets a benchmark for comprehensive control of the machining process, allying ease of use, flexibility and automation to build the Factory of the Future, according to the company.
SPRING has focused its R&D on optimizing the performance of NCSIMUL 4CAM, the CAM add-on module in its offering. Based on SPRING’s expertise in the field, NCSIMUL 4CAM 2017 effectively brings users more efficient processes and integrates their best practice. With the new version of NCSIMUL 4CAM, manufacturers now have a decision-making tool that is reliable, flexible, secured and automated for selecting the production resources they want to deploy.
New features of Version 2017 of NCSIMUL SOLUTIONS and the NCSIMUL 4CAM module:
- New probing strategies with checking and measurement of intermediary rough stocks:
- User benefits: automatic compensation, taking into account tool wear during machining, where applicable;
- Support for turning after milling, for one-click NC machine turnaround.
- User benefits: automatic reprogramming for all NC tool and machine changes, delivering real flexibility and significant time-saving for CAM programmers and workshop scheduling.
- The OPTITOOL option is built into NCSIMUL 4CAM 2017 enabling automation and optimization, especially all rapid motion, with graphic analysis enabling quick before/after comparison of improvements.
- User benefits: one-click time-saving on each single machining cycle.
- The NCSIMUL TOOL cutting tool management with 3D definitions, attachments and cutting conditions has been enriched, standardized and stored by material, machine and operation.
- User benefits: operational time-saving on project go-live and capitalized best practices for cutting conditions and automated reuse.
- One-click project update (phase calculation, simulation and ISO code restart, etc.); phase export/import to exchange project information with other customer sites or external partners.
- User benefits: enhanced inter-company collaboration with sub-contractors, suppliers and customers, covering all or part of a project, enabling data exchange and securing the whole project.
- Automatic performance analysis of the assembly for 5-axis NC machines. Automatic graphic detection of machining risk zones and less than optimal cutting conditions.
- User benefits: automatic prediction of non-quality risks for 5-axis machining (surface condition, finishing).
- 3 new CAM programs have been added to the list of Workpackages available with NCSIMUL SOLUTIONS 2017: Alphacam, CATIA, Cimatron, Creo, Edgecam, ESPRIT, FeatureCAM, GibbsCAM, hyperMILL Mastercam, NX, PowerMILL, and TopSolid’Cam.
Gilles Battier, CEO of SPRING Technologies, said: “We have developed a product that is truly unique on the market. Ours is effectively the only approach that uses data from the workshop to deliver maximum productivity for NC machine tools, cutting costs and factoring in the four key parameters that set the cost price of a part: machine cost, material cost, cutting tool cost and programming/workshop costs. Manufacturers know the score and trust us. Going forward, it’s our job to continue developing NCSIMUL SOLUTIONS and its NCSIMUL 4CAM module to offer our customers the very best, bringing them tools that will deliver the extra competitive edge they need.
Contact Details
Related Glossary Terms
- computer-aided manufacturing ( CAM)
computer-aided manufacturing ( CAM)
Use of computers to control machining and manufacturing processes.
- gang cutting ( milling)
gang cutting ( milling)
Machining with several cutters mounted on a single arbor, generally for simultaneous cutting.
- milling
milling
Machining operation in which metal or other material is removed by applying power to a rotating cutter. In vertical milling, the cutting tool is mounted vertically on the spindle. In horizontal milling, the cutting tool is mounted horizontally, either directly on the spindle or on an arbor. Horizontal milling is further broken down into conventional milling, where the cutter rotates opposite the direction of feed, or “up” into the workpiece; and climb milling, where the cutter rotates in the direction of feed, or “down” into the workpiece. Milling operations include plane or surface milling, endmilling, facemilling, angle milling, form milling and profiling.
- numerical control ( NC)
numerical control ( NC)
Any controlled equipment that allows an operator to program its movement by entering a series of coded numbers and symbols. See CNC, computer numerical control; DNC, direct numerical control.
- turning
turning
Workpiece is held in a chuck, mounted on a face plate or secured between centers and rotated while a cutting tool, normally a single-point tool, is fed into it along its periphery or across its end or face. Takes the form of straight turning (cutting along the periphery of the workpiece); taper turning (creating a taper); step turning (turning different-size diameters on the same work); chamfering (beveling an edge or shoulder); facing (cutting on an end); turning threads (usually external but can be internal); roughing (high-volume metal removal); and finishing (final light cuts). Performed on lathes, turning centers, chucking machines, automatic screw machines and similar machines.